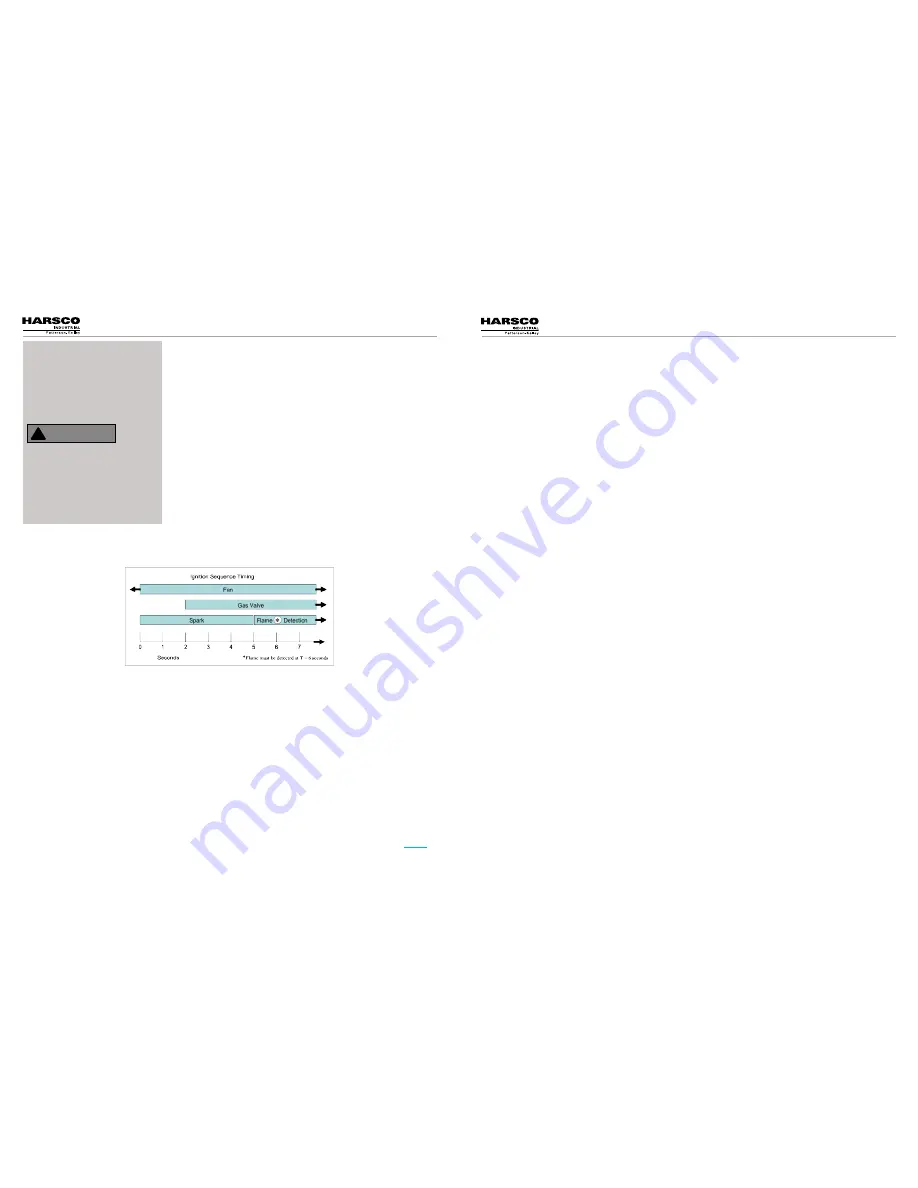
31
Harsco Industrial, Patterson-Kelley Technical Service 1.877.728.5351
M
a
INT
e
N
a
NC
e
Gas Fired Boiler
30
Harsco Industrial, Patterson-Kelley Technical Service 1.877.728.5351
M
a
INT
e
N
a
NC
e
Gas Fired Boiler
1. When the Boiler On/Off switch is turned on, power is provided through a circuit
breaker to the boiler control and the combustion blower.
2. If the high gas, low gas or low water level control is open, the boiler control
locks out and displays an error.
3. When the water temperature is below the boiler control setpoint minus the
hysteresis (On Differential), a heat request is generated.
4. Provided all limits are made, the boiler will attempt to start.
5. The controller checks that the air pressure switch is open indicating no airflow.
The blower is driven towards the prestart fan speed. When the air pressure
switch closes, the 25 second pre-purge time is started. After the pre-purge, the
blower is driven to the ignition speed.
6. A trial for ignition begins. The sequence of events is illustrated graphically
below.
7. After ignition, the fan may be driven to low fire before the boiler is released to
modulation.
8. The control modulates the firing rate between low and high fire to maintain the
desired outlet water temperature.
9. The burner will continue firing until the outlet water temperature reaches set point plus hysteresis (Off Differential). At this
temperature the fuel supply is shut off and the combustion air fan continues to run for a 30 second post-purge.
10. When the water temperature is reduced by the load on the system, a heat request is generated. The operating sequence
will recycle to
Step 4
.
The ENVI® boiler control will display text based error descriptions to indicate any problems with the boiler. There
are two types of lockouts the control may experience: manual reset lockouts requiring an operator to press the
reset button, and automatic reset lockouts that will self reset when the error condition clears. A listing of errors
and their service codes is included at the end of this section.
Should the unit fail to operate, call a qualified service technician to troubleshoot the problem and implement
corrective actions.
5.6.1 loss of Power
In the event of a power failure, the display panel is not illuminated and the entire system is de-energized, closing
all automatic valves and halting all boiler operations. When power is restored the sequence of operation will
resume at
Step 4
. If any error/lockout is present when the power is lost, the control will retain that error/lockout
and display the error/lockout when the power is restored.
5.6.2 Loss of Water Level
The low water switch opens when there is insufficient water level in the boiler. Lockout
LOW WATER LEVEL
is
shown on the display, the burner operation is interrupted, and the boiler locks out. When the correct water level is
re-established, and the control reset button is pressed, the boiler will reset and will start the sequence at
Step 4
.
5.5 s
eQuenCe
of
o
peraTIon
n
oTICe
!
Once the boiler begins the ignition
sequence, the firing sequence will
continue until main flame is reached
regardless of heat request. The
sequence can be interrupted by
turning the power switch off.
If any “Manual Reset” limit device
trips,
DO NOT
reset without
determining and correcting the
cause. Manual Reset Limits
include: Flame safeguard, high or
low gas pressure, high temperature
limit, stack temperature, low water
level.
!
WARNING
5.6 T
roubleshooTIng
5.6.3 low Gas Pressure
The low gas pressure switch opens when there is (or has been) insufficient gas pressure available for proper
operation of the boiler. If an external gas-supply shut-off valve is closed for any reason, a low gas condition will
result. Locking
LOW GAS PRESSURE
is shown on the display, the burner operation is interrupted, and the boiler
locks out. When proper gas pressure is restored, and the control reset button is pressed, the boiler will reset and
will start the sequence at
Step 4
.
5.6.4 high Gas Pressure
The high gas pressure switch opens when there is (or has been) excessive gas pressure for the proper operation
of the boiler Locking
HIGH GAS PRESSURE
is shown on the display, the burner operation is interrupted, and the
boiler locks out. When proper gas pressure is restored, and the control reset button is pressed, the boiler will
reset and will start the sequence at
Step 4
.
5.6.5 high Water temperature
When the boiler water has exceeded both the operating and high-limit temperature the high limit switch
opens, and Locking
HIGH LIMIT
is shown on the display. When the water temperature falls below the high-limit
temperature, the boiler will remain locked out until the water high limit switch is manually reset and the front panel
reset button is pressed. Once reset, the control will restart the sequence of operation at
Step 4
.
5.6.6 low Air
If the display panel indicates Locking
AIR SWITCH NOT OPEN
or Locking
AIR SWITCH NOT CLOSED
this indicates
improper airflow through the boiler. Check the hoses leading to the air switches. Verify proper blower operation.
An air switch error does not necessarily mean that the air switch is defective.
When
AIR SWITCH NOT OPEN
is shown on the display, check that the air switch is open when the fan is off.
Check that there is no air flow through the boiler when the fan is off.
When
AIR SWITCH NOT CLOSED
is shown on the display, check that the air switch is closed when the fan is
running. If the air switch does not close within 5 minutes during purge, the boiler locks out. Check that the burner
is clean ("Cleaning the Burner,"
Section 5.2
) and that there are no obstructions to airflow in the intake or exhaust
ducts.
5.6.7 Flame Failure
In the event of a flame failure, the main fuel valves are de-energized and a manual reset lockout occurs. Locking
IGNITION FAILURE
or Lockout
FLAME FAILURE
is shown on the display. The cause of flame failure must be
diagnosed and repaired before the control is reset.
When
IGNITION FAILURE
is shown on the display, the boiler did not light during a trial for ignition. Check that the
spark, electrode, ignition wire, and gas valve are functioning properly.
When
FLAME FAILURE
is shown on the display, the boiler lost the flame during run. Check that the combustion is
setup properly, the gas pressure is correct, as well as other combustion parameters.
5.6.8 Flame error
Locking
LATE FLAME
Blocking
FALSE FLAME
These errors signify flame error. This may be caused by a failed or leaky gas valve or a flame detector
malfunction. If gas valve leakage is suspected, the unit must be isolated by turning off the main gas supply line.
Qualified and knowledgeable service personnel must be called to evaluate and repair/replace the failed parts.
5.6.9 stack Problem
BLOCKED FLUE
indicates that the high exhaust back pressure switch has tripped. This may be caused by a
blocked stack, a blocked air inlet, or a blocked condensate system. When the blockage is removed, the boiler will
automatically restart.
Figure 5.5