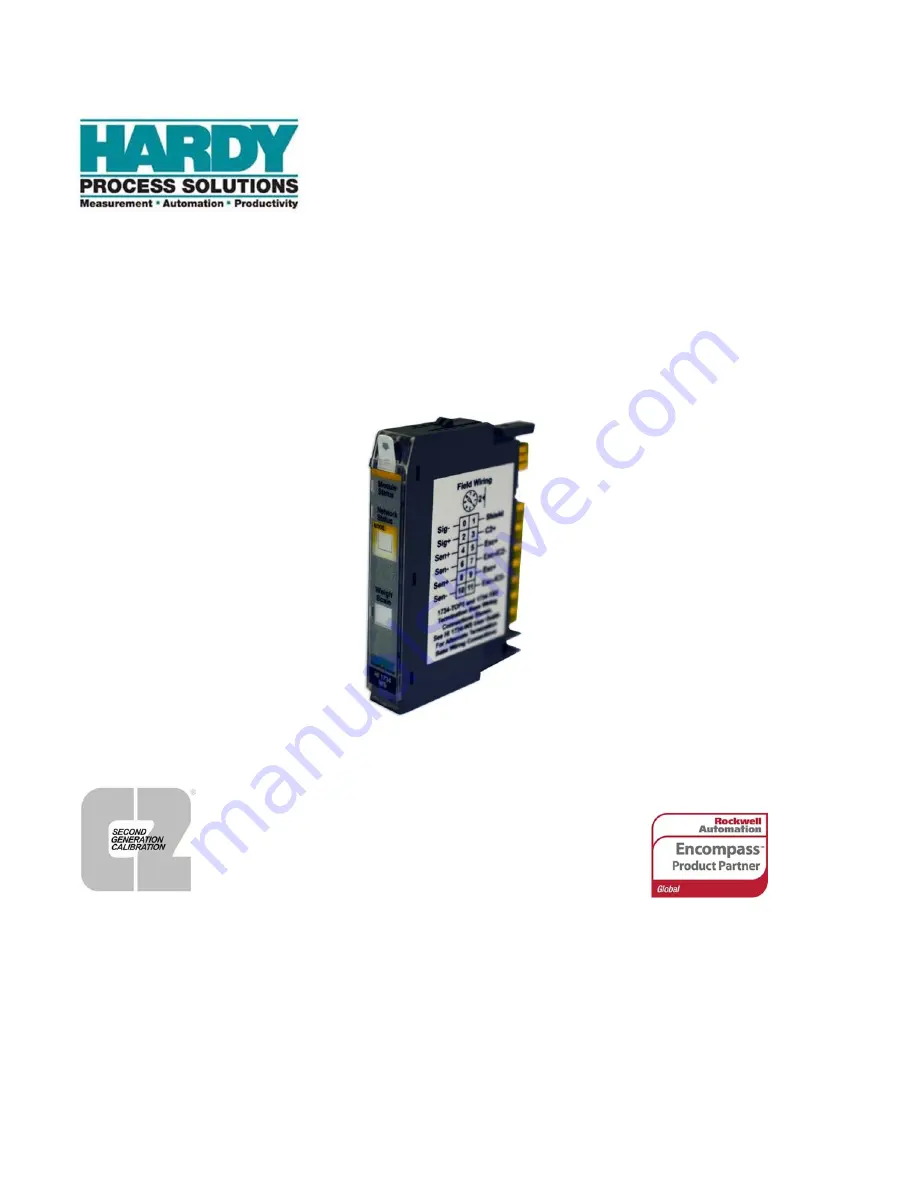
HI 1734-WS
POINT I/O Weigh Scale Module
Installation & Operations Manual
9440 Carroll Park Drive
San Diego, CA 92121
Phone: (858) 278-2900
FAX: (858) 278-6700
Web-Site: http://www.hardysolutions.com
Hardy Process Solutions Document Number: 0596-0354-01 Rev. A
Copyright © 2017 Hardy Process Solutions All Rights Reserved. Printed in the U.S.A.