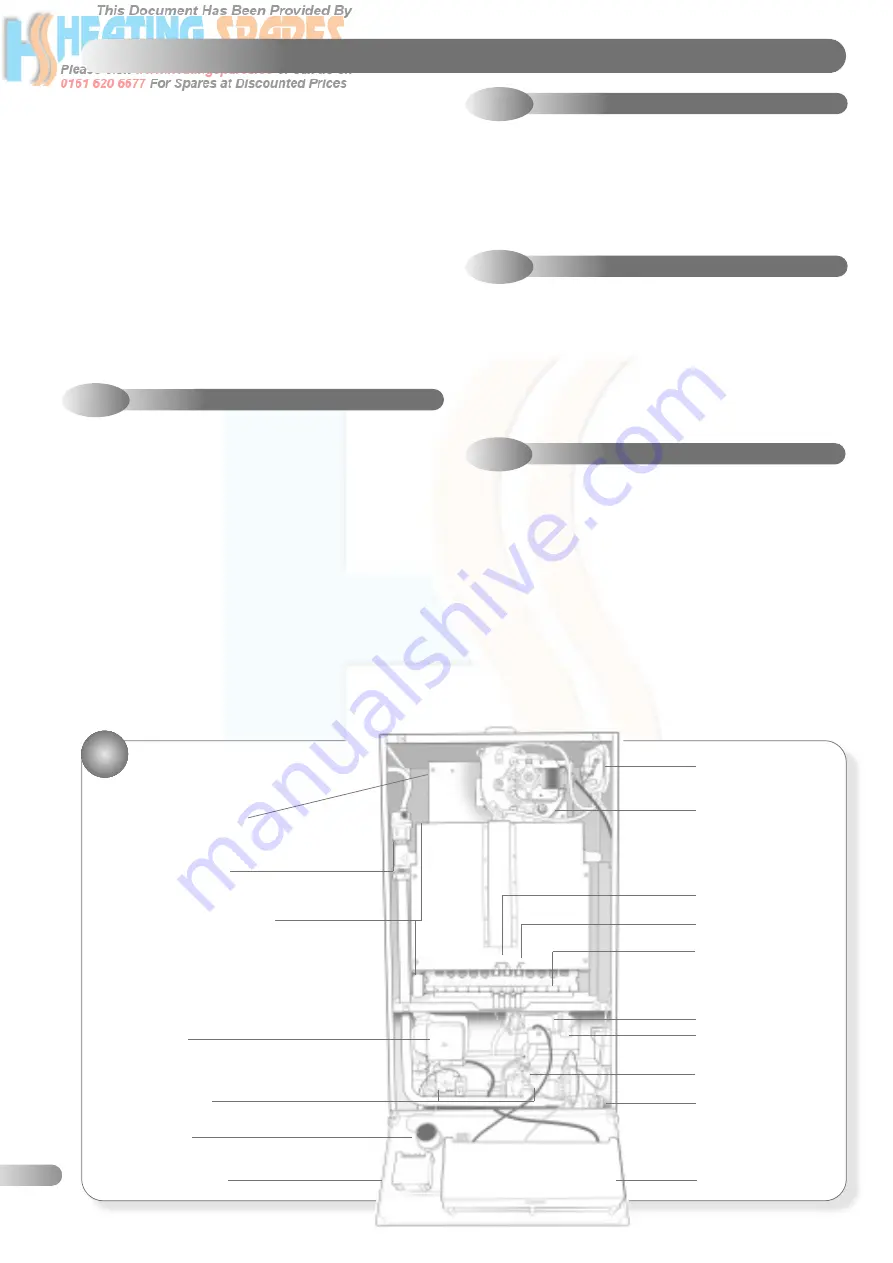
Supplied By www.heating spares.co Tel. 0161 620 6677
ROUTINE SERVICING
6
29
LOCA
TION OF
SERVICEABLE
COMPONENTS
6.1
MAIN BURNER ASSEMBLY
6.2
BURNER INJECTOR
6.3
IGNITION AND DETECTION ELECTRODES
6.4
FAN ASSEMBLY
T
o ensure continued efficient operation of the appliance, it is
recommended that it is checked and serviced as necessary at regular
intervals. The frequency of servicing will depend upon the particular
installation conditions and usage, but in general once a year should
be adequate. It is the law that any service work must be carried out
by a competent person, such as British Gas or other CORGI
registered personnel.
The boiler incorporates a flue sampling point on the top panel in
front of the flue outlet. If the service engineer has suitable equipment
to analyse the flue gas, the plastic cap may be removed and a 6mm
inside diameter sample tube fitted. Check CO
2
/CO values and
compare with figure stated in section 2.4. Do not forget to replace
the plastic cap after use. Before commencing any service operation,
ISOLATE the mains electrical supply, and TURN OFF the gas supply
at the main service cock.
Service the appliance by following the full procedure detailed below:
Refer to Figs. 29 and 30
a)
Remove the casing fr
ont panel. Refer to Fig. 31.
b)
Remove the sealed chamber fr
ont panel (4 screws).
c)
Remove the combustion chamber fr
ont panel (9 screws). Take
care not to damage the insulation.
Do not attempt to light the burner with Front Panel removed.
d)
Remove the two securing scr
ews and lower the controls fascia
panel.
e)
Disconnect the thr
ee leads from the spark and detection
electrodes and disengage the grommets from the combustion
chamber bottom panel.
f)
Remove the 4 scr
ews securing the burner to the gas manifold
and slide the burner out of the combustion chamber.
g)
Inspect, and if necessar
y clean the main burner ports using a soft
brush or vacuum cleaner. Do not use a wire brush or any
abrasive material.
Check that the injectors fitted in the gas manifold are free from dirt and
debris. If necessary, clean the injector orifices carefully using a soft
brush or vacuum cleaner. Do not use a wire brush or any abrasive
material.
It is not necessar
y to remove the injectors.
If ther
e are signs of
injector(s) being blocked please call the Halstead Service Department.
a)
Inspect the ignition and detection electr
odes in situ. If necessary,
clean using a soft brush. If either the electrode or the ceramic
insulation show signs of damage or wear, replace the
electrode(s).
b)
Check that the alignments of the ignition and detection
electrodes are correct. Refer to Fig. 34. Adjust by carefully
bending the tip of the electrode rod whilst supporting the base of
the rod. Do not put any pressure on the ceramic insulation.
a)
Remove combustion chamber fr
ont panel. Refer to 6.1.
b)
Car
efully disconnect the two electrical leads from the fan.
c)
Disconnect the air pr
essure switch sensing pipes from the fan,
noting their positions
d)
Remove the fan assembly by unscr
ewing the three screws,
lowering the assembly and lifting it forwards.
e)
Inspect the fan assembly (especially the impeller and the venturi)
for dirt, damage, or signs of wear. If necessary clean the
impeller and/or venturi using a soft brush or vacuum cleaner.
Spin the impeller and check that it rotates freely, without noise,
and without imbalance. If there is any sign of deterioration or
damage, replace the fan.
•
COMBUSTION CHAMBER
FRONT PANEL FIXING
SCREWS (9)
•
•
•
•
•
•
AUTO AIR
VENT
FAN ASSEMBLY BASE
PLATE SCREWS
PUMP
GROUP SET
CONTROL
BOX
AIR PRESSURE
SWITCH & PIPES
GAS CONTROL VALVE
GAS COCK
PRESSURE RELIEF
VALVE
FAN ASSEMBLY
PRESSURE
GAUGE
•
OVERHEA
T THERMOSTAT
•
•
•
•
•
CONTROL P
ANEL
DETECTION ELECTRODE
BURNER
IGNITION ELECTRODES
•
• •
•
20
•
•