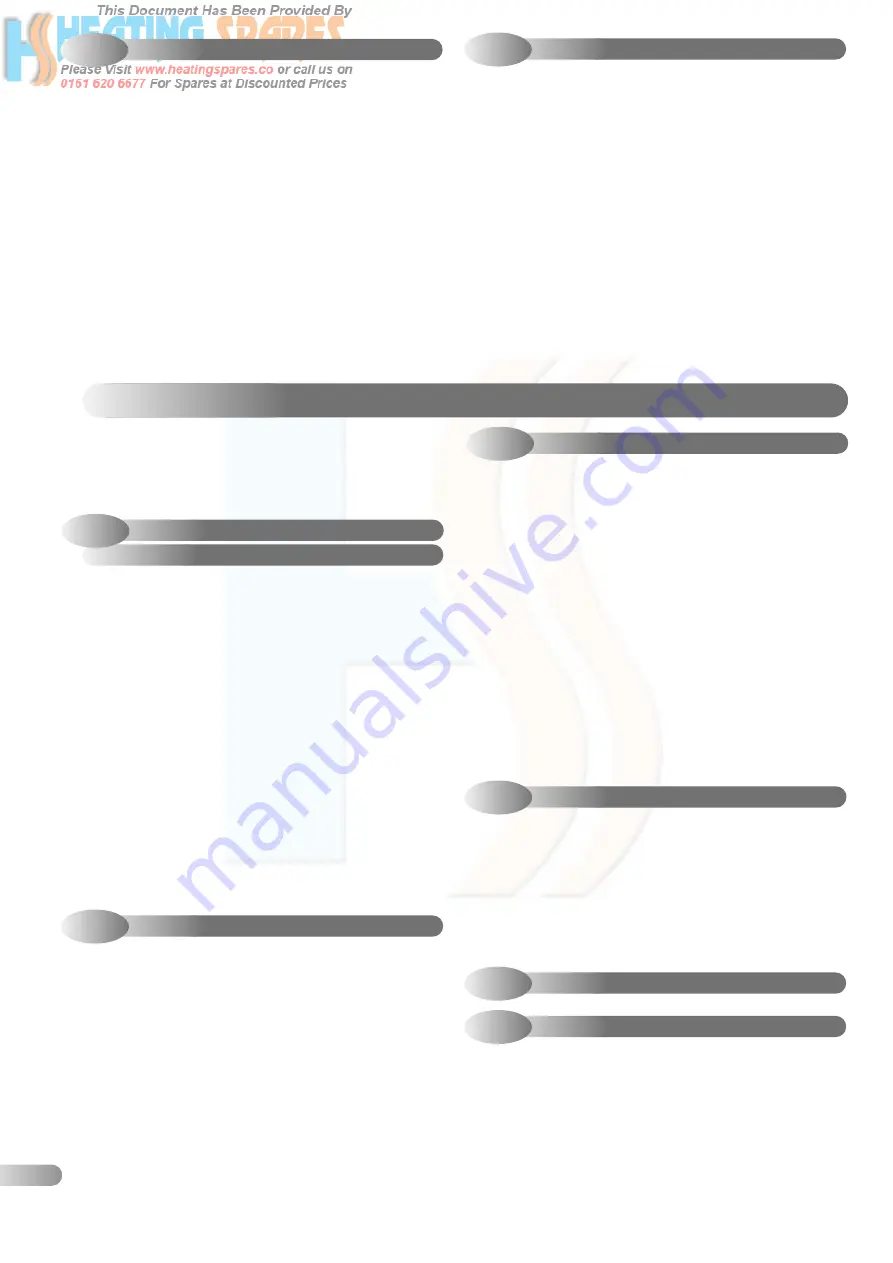
Supplied By www.heating spares.co Tel. 0161 620 6677
PARTS REPLACEMENT
9
9.2
FAN ASSEMBLY
9.3
BURNER
9.4
IGNITION & DETECTION ELECTRODES
9.5
MULTIFUNCTIONAL GAS CONTROL
9.5.1
GAS CONTROL REPLACEMENT
The design of the appliance is such that the combustion chamber
insulation should not require replacement unless mechanically
damaged. It is recommended that to prevent dust, the insulation is
dampened prior to removal.
a)
Remove the r
etaining screw and lift off the casing front panel.
Refer to Fig.28
b)
Remove the sealed chamber fr
ont panel (4 screws).
c)
Remove the combustion chamber fr
ont panel (9 screws).
The front insulation may now be replaced, but to replace the side and
rear insulation, the heat exchanger must be removed. Refer to section X
d)
Fit the new insulation and r
e-assemble in reverse order.
e)
Ensur
e that all joints and seals are correctly re-fitted and re-
commission the system (if necessary) using the procedure in
section 5.1.
It is r
ecommended that a protective mask is worn when
changing or handling the insulation material.
a)
Remove the casing fr
ont panel. Refer to Fig. 31
b
)
Remove the sealed chamber front panel (4 screws).
c)
Remove the combustion chamber fr
ont panel (9 screws). Take
care not to damage the insulation.
d)
Lower the contr
ols front cover panel and remove the two
securing screws and lower the controls fascia panel.
e)
Disconnect the thr
ee leads from the spark and detection
electrodes and disengage the grommets from the combustion
chamber bottom panel.
f)
Remove the four scr
ews securing the burner to the gas
manifold and slide the burner out of the combustion chamber.
g)
T
ransfer the ignition and detection electrodes to the new
burner and check their alignment. Refer to Fig.34.
h)
Fit the new bur
ner and reassemble in reverse order. Ensure
that all joints and seals are correctly re-fitted.
Refer to Fig. 29
a)
Ensur
e supply voltage is isolated. Remove the burner. Refer to
section 9.3.
b)
Fit the new ignition and /or detection electr
ode(s) and check
that both electrodes are aligned as detailed in Fig.34.
c)
Re-assemble in r
everse order. Ensure that all joints and seals
are correctly re-fitted.
Refer to Fig. 29
a)
Ensur
e supply voltage is isolated.
b)
Remove the casing fr
ont panel, sealed chamber panel and
combustion chamber panel. Refer to section 9.3
c)
Car
efully disconnect the two electrical leads from the fan.
d)
Disconnect the air pr
essure switch sensing pipes from the fan,
noting their position.
e)
Remove the fan assembly (3 scr
ews) and withdraw the
assembly by lowering and lifting it forwards.
f)
Fit the new fan assembly and r
e-assemble in reverse order.
Ensure that all joints and seals are correctly re-fitted. (Polarity is
immaterial on the fan connections.)
Before commencing any service operation, ISOLATE the mains electrical
supply and TURN OFF the gas supply at the main service cock.
It is the law that any service work must be carried out by a registered
person.
9.1
COMBUSTION CHAMBER
INSULATION
24
8.4
DHW FAULT FINDING
8.5
CENTRAL HEATING FAULT FINDING
When the hot water tap is tur
ned on, the controls should carry out
a set of start up checks followed by an ignition sequence. Refer to
section 5.2
If the control has powered up correctly but does not respond to a
DHW demand.
Check operation of fan and air pressure switch. Check if Red LED
on DHW flow switch is on or off. If off, check DHW hall effect
sensor and condition of sanitary flow detector in hydraulic group
set. If on, check wires to flow switch, check DHW thermistor and
wires. If fan, air pressure switch, DHW flow switch, thermistor
and wires are OK replace PCB.
Guidance notes (Refer to section 7.1):
If DHW temperature heavily fluctuates during a long draw off and
occasionally goes to an overheat Lock-out condition, check the
secondary plate heat exchanger for debris and replace.
Upon a demand for Central Heating, (closure of the time switch and
room thermostat, if fitted) , the controls should carry out a set of start up
checks, followed by an ignition sequence. Refer to Section 5.2.
If the control has powered up correctly but does not respond to a CH
demand. Check voltage between pin 2 plug X1A (orange wire) and
pin 2 X13 (blue wire). If 0V ac, check room thermostat and clock. If
230 V ac, check operation of fan and air pressure switch. Check
operation of gas valve. If room thermostat clock, fan, air pressure
switch and gas valve are OK replace PCB.
Guidance notes (Refer to section 7.1):
1) Whenever a CH demand is removed, either by the timer, the room
thermostat or the boiler internal temperature control, an anti cycle mode
is initiated which prevents the boiler from firing in CH mode for 3
minutes. Ensure that the control is not in this mode by removing power
from the control and restoring it after a delay of 10 seconds.
Refer to Figs. 32 and 35
a)
Ensur
e supply voltage is isolated.
b)
Lower the contr
ols front cover panel and remove the casing
front panel. Refer to section 9.3
c)
Remove the two r
etaining screws and lower the controls
fascia panel.
d)
Release the scr
ew and unplug the electrical lead from the
gas control.