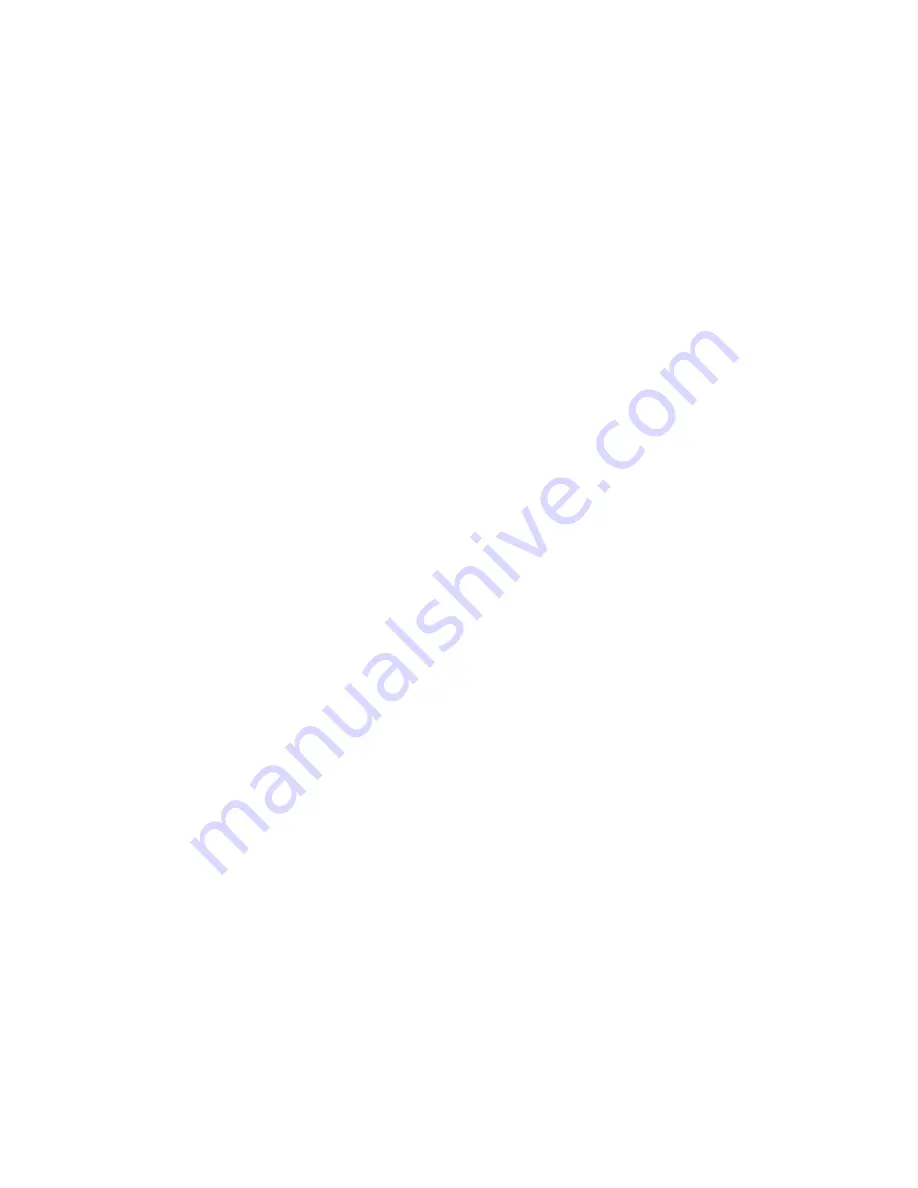
35 / 47
Hakki Pilke 50 Pro
Translation
Version 1-2018
5.4.2.
Replacing and tensioning the out-feed conveyor belt
The instructions for tensioning and aligning the out-feed conveyor are presented in Section 4.4.
Replace the out-feed conveyor belt as follows:
1.
Pull out the pin locking the conveyor in place and lower the conveyor to the ground.
2.
Shut the machine down and disconnect it from its power sources.
3.
Move the belt joint to the start of the conveyor.
4.
Fold the conveyor, but do not place the belt support in the transport position. This will allow the
belt to hang loose.
5.
Disconnect the joint by opening the bolts.
6.
Remove the old belt.
7.
First, insert the new belt under the folded conveyor (bottom opening) from the end of the
conveyor with the plates facing downwards. Feed the belt in until you can pull it out from the
other end of the conveyor. Pull out a length of approx. 60 cm.
8.
Push the other end of the belt into the upper section of the folded conveyor (top opening) from
the end of the conveyor. Feed it in until you can connect the joint.
9.
Pull the excess belt to the start of the conveyor.
10.
Lower the conveyor back to the operating position and tension the belt.
The belt is at the correct tension when its middle section is raised approx. 15 cm when the conveyor is
in the operating position. An excessively tight belt may be damaged more easily, and it places
unnecessary strain on the conveyor bearings.
5.4.3.
Replacing the out-feed conveyor plates
The out-feed conveyor plates can be replaced by disconnecting the bolt joints (3 x M8) fastening the
plates and replacing the plates with new ones. It is recommended that you move the belt into a position
that puts the plate to be replaced above the conveyor. Shut the machine down and disconnect it from the
power source for the duration of the procedure.
5.5.
Lubrication
All of the firewood processor's lubrication points, which require Vaseline, have been labelled. There are
24 lubrication points, presented in the figures below. Note! Take care when applying grease to dustproof
bearings!
1.
Hinged nipples of the guard (2 pcs) in Figures 35 and 36. (every 200 hours)
2.
Grease nipple for the wood measuring device cylinder in Figure 35. (every 50 hours)
3.
Bearing nipples of the out-feed conveyor’s lower roller (2 pcs) in Figure 37. (every 200 hours)
4.
Grease nipple for the output conveyor's turning device in Figure 37. (every 200 hours)
5.
Grease nipples of the out-feed conveyor’s swivel cylinder (2 pcs) in Figure 38. (every 200
hours)
6.
Grease nipples of the out-feed conveyor’s lifting cylinder (4 pcs) in Figures 38–40 (every 200
hours).
7.
Grease nipple of the hydraulic in-feed roller bearing in Figure 41. (every 200 hours)
8.
Grease nipple for the wood measuring device cylinder in Figure 42. (every 50 hours)
9.
Grease nipples of the cutting cylinder (2 pcs) in Figure 46. (every 50 hours)
10.
Grease nipples in the splitting groove support (Figure 42) and splitting blade winch (Figure 39).
(according to use)
11.
Grease nipple of the in-feed conveyor roller in Figure 43. (every 200 hours)
12.
Grease nipples of the log press (4 pcs) in Figure 42. (every 50 hours)