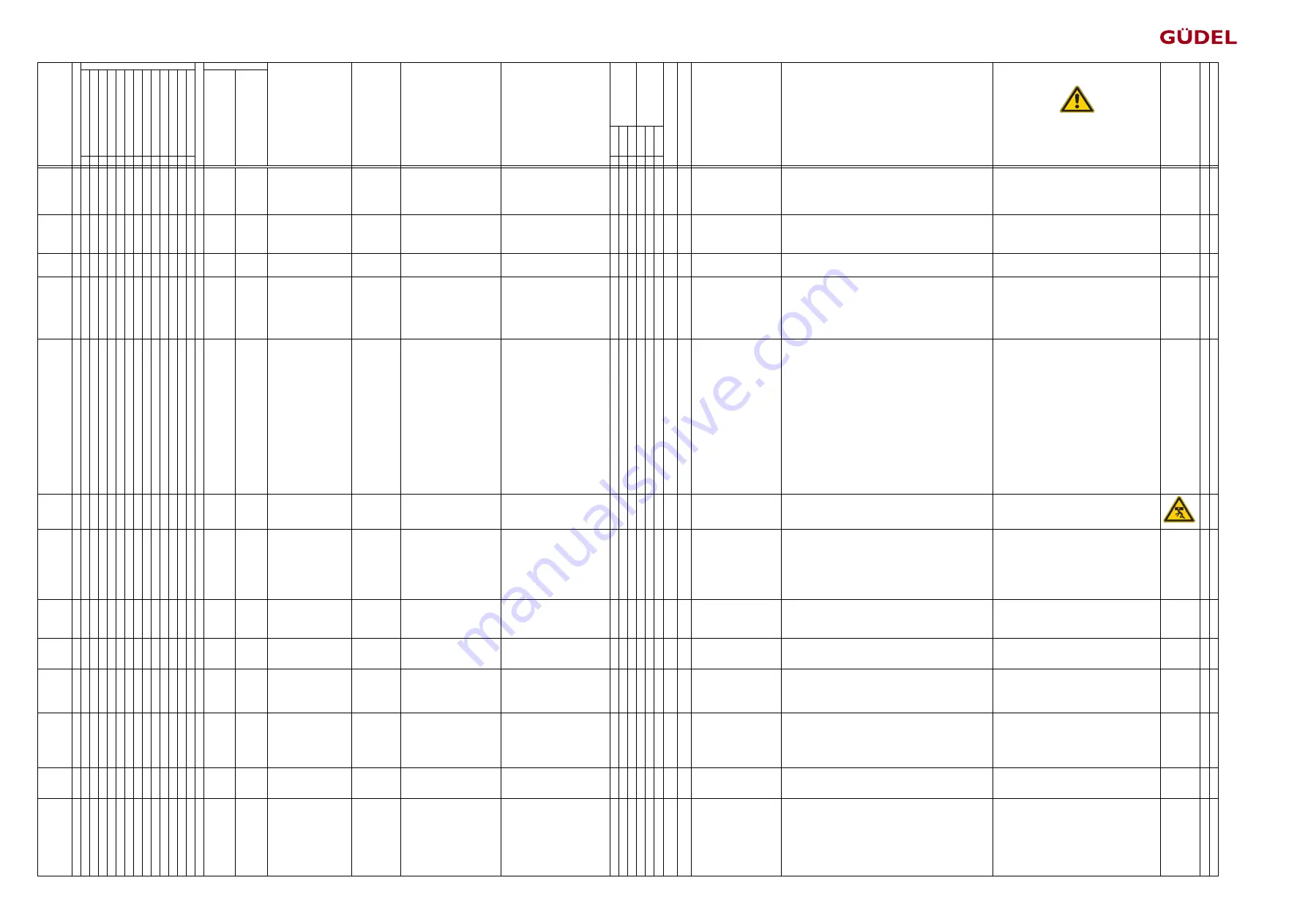
Mi
nor
Moder
ate
Sev
er
e
Rar
e
O
ften
F
requent
A
B
C
D
E
F
G
H
I
J
K
L
M
1
4
10
1
2
3
The following should be prevented:
1.1
x x x x x x x x x x x x x x
x
x
Processing of hazardous
materials. Fire and danger of
explosion.
Thermal factors
All
Non-compliance with the intended
use
Someone is injured or killed
x x
10 3/d Someone is injured or killed
Intended use: Güdel devices are only used to bring objects to a specific position,
hold them there or move them simultaneously with other machine movements.
No hazardous (e.g. poisonous or explosive) objects must be moved. Güdel devices
must not be operated in potentially explosive areas. The ambient temperature
during operation must be between 5° and 40 °C.
If the intended use is modified, this can result in hazards that are
not covered by the safety concept.
x Y
1.2
x
x x x
x x x x
x
x
Suspended load
Technician,
forwarding
agent,
commissioning
technician
Faulty lashing of slings, improper
use, defective or insufficient hoists
Injuring or killing of persons due to
components falling down
x x
10 3/d Persons are injured or killed by
falling parts.
Use appropriate lifting equipment. Wear protective clothing. Keep a safe distance.
Observe the operating manual. Never step below suspended loads
None
x Y
1.3
x
x x x
x x x x
x
x
Heavy load
Technician,
forwarding agent
Lifting without auxiliary agents,
falling
Physical injuries
x x
10 3/d Persons are injured
Use suitable lifting units. Use trained personnel as well as protective clothing
None
x Y
1.4
x
x
x
Movement of the axes
Setters
Unexpected start
Someone is surprised by the
unexpected situation and injured as a
result
x x
10 3/d When the permission button is
pressed, the operator is
exposed to a hazard due to an
automatic movement triggered
by a third party.
Axes can only be moved individually by a two-hand operating device in jog mode.
In the event of several carriages on a single gantry, the individual carriages have
to be selected using a key switch. The permission button is a "shock button".
For the permission button to be activated, only one safety door may be open and
the others must be closed and confirmed. Safety-relevant parts of the control are
inspected at appropriate time intervals by the machine control system.
In confirmation mode, the operator must pay great attention and
have a high level of individual responsibility. Only perform
movements if no other person is in the danger area and none of
your own body parts are in the line of danger of the
corresponding axis.
x Y
1.5
x
x
x
x
Movement of the axes,
suspended loads
(vertical axes and
workpieces)
Operators,
Maintenance
personnel,
Commissioning
technicians
Gripper problems
Defective motor brake
General problems in the drive train
Someone is surprised by vertical
movement and injured as a result.
x
x
20 3/d That neither operating
personnel nor third parties can
reach or walk into the
hazardous locations where
automatic movements are
performed. The areas of
movement must be secured
accordingly.
The areas of movement are enclosed by light grids, light curtains as well as
mechanical safety fences so that it is impossible to enter this area from any
direction.
There are door elements or light barriers that allow access to the danger area or
to a portion of the danger area.
The height of the safety fences is described in EN ISO 13857.
Safety shutdown situation:
The vacuum system remains active in a de-energized condition.
Door elements: When opening the danger area, a safety shutdown is performed for
at least those drives that pose a hazard in this area.
The door elements are also locked electromechanically.
Light barriers: These are monitored so that when contact is broken, at least those
drives that pose a hazard in this area are shutdown. The distance between the
source of the danger and the light barriers is described in EN ISO 13855.
In normal operation, all protective hoods must be closed.
Removable protective hoods must be screwed securely.
Required behavior:
Inspect the protective hoods before starting normal operation.
Safety shutdown situation: Never step into the area below
suspended workpieces and vertical axes.
x Y
1.6
x x
x
Movement of the axes,
suspended loads
(vertical axes and
workpieces)
Technician,
forwarding agent
Removal of transport securing
device without supporting
suspended loads and axes.
Someone is surprised by the
unexpected movement and injured as
a result
x x
10 3/d Suspended loads fall.
Before removing the transport securing device, support the suspended loads or
axis.
If motors or gearboxes are removed, vertical axes must always be secured or
supported.
None
x Y
1.7
x x x x
x
x
Movement of the axes.
Parts are flung out
Operators,
Maintenance
personnel,
Cleaning
personnel
Unexpected start
Someone is surprised by the
unexpected situation and injured as a
result
x x
10 3/d A person is injured by the
unexpected start-up of moving
parts.
The start-up of the system without the permission button being pressed or available
must be prevented.
With the permission device pressed, moving system parts can be moved in a
controlled manner, even if the system is unsecured.
When the permission button is pressed, it must not be possible for the operator to
be endangered by an automatic movement triggered by a third party.
The lockable main switch of the system breaks all main and control circuits.
Never step into the area below suspended workpieces and
vertical axes.
In confirmation mode, the operator must pay great attention and
have a high level of individual responsibility.
If motors or gearboxes are removed, vertical axes must always
be secured or supported.
x Y
1.8
x
x
x
Parts flung out
Setter,
third parties
Gripper problems, defective motor
brake, torn belt (telescopic axis),
pressure drop (load balancing),
general problems in the drive train
Someone is surprised by parts flying
away and being injured as a result.
x x
10 3/d Parts are flung out.
The axes can only be moved with reduced speed.
Rotating parts must be shut down securely.
Work in this mode requires great attention and a high level of
individual responsibility from the operator. Only perform
movements if no other person is in the danger area and none of
your own body parts are in the line of danger of the
corresponding axis.
x Y
1.9
x
x
x
Parts flung out
Operators,
third parties
Parts clamped improperly
Breakage of rotating tools
Someone is surprised by parts flying
away and being injured as a result.
x x
10 3/d Operating personnel or third
parties are injured by parts that
become loose and fly away.
Mechanical protective equipment must be placed in the possible flight path of
parts that could fly away.
Safety devices are inspected by means of calculation and trial.
In normal operation, all protective hoods must be closed,
removable protective hoods must be screwed securely.
Required conduct: Inspect the protective hoods before starting
normal operation.
x Y
1.10
x
x x x x
x
x
Parts flung out
Operators, third
parties
Carrier hits mech. bumper unit.
Moving parts are torn out of their
holder and hurled away due to the
delay which occurs.
Someone is surprised by parts flying
away and being injured as a result.
x x
10 3/d Operating personnel or third
parties are injured by parts that
become loose and fly away.
Attachments to moved masses (vertical and horizontal axes) must be fastened in
such a manner to prevent them from being separated or sheared off due to the
delay. The max. delay must be calculated. The calculation of the fastening and
loading of the attachments must also be taken into account in the construction.
Workplaces and operating devices in the direction of travel
should be avoided as far as possible.
x Y
1.11
x
x
Suspended loads
(vertical axes, telescope
axes, counter balance
cylinders, and workpieces)
Setters
Gripper problems, defective motor
brake, torn belt (telescopic axis),
pressure drop (load balancing),
general problems in the drive train
Someone is surprised by the
unexpected situation and injured as a
result
x x
10 3/d It must be ensured that when
the permission button is not
pressed, no persons can be
endangered by falling vertical
axes, telescope axes, or
workpieces.
Grippers have to remain in the de-energized state in the clamp position.
To minimize risk, vertical axes can be redundantly equipped with an additional
brake.
Telescopic axes and counter balance cylinder: Special attention is required here.
The axis (for a telescopic axis, the 2nd level) is to be secured with locking pins.
Operation in setup mode only when the restricted area is closed off.
Do not walk under suspended workpieces or vertical axes. Take
special care with telescope axes. Inspect belts visually for cracks
and tears before every setup procedure.
x Y
1.12
x
x
Suspended loads
(vertical axes, telescope
axes, counter balance
cylinders, and workpieces)
Setters
Inattention and/or careless
operation by operator
Someone is surprised by the
unexpected situation and injured as a
result
x x
10 3/d Workpieces are dropped
accidentally
Grippers can only be operated in the storage position.
Do not walk under suspended workpieces or vertical axes. Take
special care with telescope axes. Inspect belts visually for cracks
and tears before every setup procedure.
x Y
1.13
x x x
x
Suspended loads
(vertical axes, telescope
axes, counter balance
cylinders, and workpieces)
Maintenance
personnel,
cleaning
personnel
Unexpected start-up
Defective motor brake
Torn belt (telescope axis)
Pressure drop (load balance)
General problems in the drive train
Disassembly of the vertical axis
motor
Someone is surprised by the
unexpected situation and injured as a
result
x x
10 3/d Persons injured by vertical
axes falling down.
Workpieces have to be deposited beforehand in automatic or setup mode.
The system must be brought into a safe state (emergency off)
Vertical axes have to be secured with the supplied locking pins for the vertical axes
or with the transport securing device.
Appropriate safety devices (cables, auxiliary supports etc.) must be used to secure
telescope axes against falling down.
Avoid walking under suspended workpieces or vertical axes.
Take special care with telescope axes. Inspect belts for cracks
and tears before every maintenance procedure.
Workpieces must be deposited beforehand in automatic or setup
mode.
Vertical axes must be secured with the supplied locking pins for
the
vertical axes or with the transport securing device.
Appropriate safety devices (cables, auxiliary supports etc.) must
be used to secure telescope axes against falling down.
x Y
Hazard analysis / Risk analysis
Customer:
Machine type: CP with/without control system
Project no.:
Document no.:
Affec
ted per
so
n(
s)
Cor
re
sp
ondi
ng oper
ati
ng
mode
Triggering factor
Event
(worst case)
(without protective measures)
Setup / Changeov
er
Cl
eani
ng
T
roubl
es
hooti
ng / Repai
r
Mai
ntenanc
e
D
isa
sse
m
bl
y
Di
sp
os
al
Source of danger
F
loor
-mounted dr
iv
e ax
es
Rai
sed dr
iv
e ax
es
Application area
E
xtent of the
damage
Categor
y / PLr
(
S
IL)
mi
ni
mal
Risk assessment / safety goals / protective measures / residual risks
1)
Solution suggested to the customer (cursive, Times New Roman)
Güdel solution (Arial)
Sa
fe
ty
r
eq
uir
em
en
t f
ulf
ille
d [
Y
/N
]
Recommendation to avoid residual risks
O
per
ati
ng manual
Protective measures
(existing protective measures)
Danger
symbol
Safety goal
(negation of the event)
Pr
ob
ab
ilit
y o
f
occu
rre
nc
e
R
isk a
sse
ssm
en
t (<
=
3;
4
-8
; 9
-2
0;
>
20
Inter
nal
as
sembl
y
Nor
mal
oper
ati
on
Haz
ar
d no.
Inter
nal
c
ommi
ss
ioni
ng
Inter
nal
di
sa
ss
embl
y
Commi
ss
ioni
ng at the
T
rai
ni
ng at the c
us
tomer
T
rans
por
t
A
sse
m
bl
y a
t t
he
cu
st
om
er
Special operating modes
Author: Alain Thurner
Created: 11.12.2009
Process owner: Michael Marti
Approved: 11.06.2019 / Version 01
Page 1 of 3
Risikobeurteilung_Module CP_2019_06_11_EN.xlsx
Содержание CP 3-5 V2
Страница 4: ...Revision history OPERATING MANUAL CP 3 5 V2 9007202252815371_v1 0_EN US 4...
Страница 15: ...Options Third party documentation Table of contents OPERATING MANUAL CP 3 5 V2 9007202252815371_v1 0_EN US 15...
Страница 16: ...Table of contents OPERATING MANUAL CP 3 5 V2 9007202252815371_v1 0_EN US 16...
Страница 34: ...Safety OPERATING MANUAL CP 3 5 V2 9007202252815371_v1 0_EN US 34...
Страница 42: ...Design function OPERATING MANUAL CP 3 5 V2 9007202252815371_v1 0_EN US 42...
Страница 52: ...Transport OPERATING MANUAL CP 3 5 V2 9007202252815371_v1 0_EN US 52...
Страница 130: ...Operation OPERATING MANUAL CP 3 5 V2 9007202252815371_v1 0_EN US 130...
Страница 216: ...Maintenance OPERATING MANUAL CP 3 5 V2 9007202252815371_v1 0_EN US 216...
Страница 217: ...9 4 Maintenance schedules Maintenance OPERATING MANUAL CP 3 5 V2 9007202252815371_v1 0_EN US 217...
Страница 218: ...Maintenance OPERATING MANUAL CP 3 5 V2 9007202252815371_v1 0_EN US 218...
Страница 220: ...Maintenance OPERATING MANUAL CP 3 5 V2 9007202252815371_v1 0_EN US 220...
Страница 222: ...Maintenance OPERATING MANUAL CP 3 5 V2 9007202252815371_v1 0_EN US 222...
Страница 224: ...Maintenance OPERATING MANUAL CP 3 5 V2 9007202252815371_v1 0_EN US 224...
Страница 228: ...Maintenance OPERATING MANUAL CP 3 5 V2 9007202252815371_v1 0_EN US 228...
Страница 230: ...Maintenance OPERATING MANUAL CP 3 5 V2 9007202252815371_v1 0_EN US 230...
Страница 232: ...Maintenance OPERATING MANUAL CP 3 5 V2 9007202252815371_v1 0_EN US 232...
Страница 234: ...Maintenance OPERATING MANUAL CP 3 5 V2 9007202252815371_v1 0_EN US 234...
Страница 236: ...Maintenance OPERATING MANUAL CP 3 5 V2 9007202252815371_v1 0_EN US 236...
Страница 264: ...Repairs OPERATING MANUAL CP 3 5 V2 9007202252815371_v1 0_EN US 264...
Страница 266: ...Repairs OPERATING MANUAL CP 3 5 V2 9007202252815371_v1 0_EN US 266...
Страница 272: ...Decommissioning storage OPERATING MANUAL CP 3 5 V2 9007202252815371_v1 0_EN US 272...
Страница 277: ...13 Spare parts supply Spare parts supply OPERATING MANUAL CP 3 5 V2 9007202252815371_v1 0_EN US 277...
Страница 278: ...Spare parts supply OPERATING MANUAL CP 3 5 V2 9007202252815371_v1 0_EN US 278...
Страница 284: ...Spare parts supply OPERATING MANUAL CP 3 5 V2 9007202252815371_v1 0_EN US 284...
Страница 302: ...List of illustrations OPERATING MANUAL CP 3 5 V2 9007202252815371_v1 0_EN US 302...
Страница 306: ...List of tables OPERATING MANUAL CP 3 5 V2 9007202252815371_v1 0_EN US 306...
Страница 316: ...Appendix OPERATING MANUAL CP 3 5 V2 9007202252815371_v1 0_EN US...
Страница 317: ...Hazard analysis Risk analysis Appendix OPERATING MANUAL CP 3 5 V2 9007202252815371_v1 0_EN US...
Страница 318: ...Appendix OPERATING MANUAL CP 3 5 V2 9007202252815371_v1 0_EN US...
Страница 322: ...Addition to declaration of incorporation Appendix OPERATING MANUAL CP 3 5 V2 9007202252815371_v1 0_EN US...
Страница 323: ...Appendix OPERATING MANUAL CP 3 5 V2 9007202252815371_v1 0_EN US...
Страница 326: ...Technical data Appendix OPERATING MANUAL CP 3 5 V2 9007202252815371_v1 0_EN US...
Страница 327: ...Appendix OPERATING MANUAL CP 3 5 V2 9007202252815371_v1 0_EN US...
Страница 328: ...Layout Appendix OPERATING MANUAL CP 3 5 V2 9007202252815371_v1 0_EN US...
Страница 329: ...Appendix OPERATING MANUAL CP 3 5 V2 9007202252815371_v1 0_EN US...
Страница 330: ...Spare parts lists Appendix OPERATING MANUAL CP 3 5 V2 9007202252815371_v1 0_EN US...
Страница 331: ...Appendix OPERATING MANUAL CP 3 5 V2 9007202252815371_v1 0_EN US...
Страница 332: ...Options Appendix OPERATING MANUAL CP 3 5 V2 9007202252815371_v1 0_EN US...
Страница 333: ...Appendix OPERATING MANUAL CP 3 5 V2 9007202252815371_v1 0_EN US...
Страница 334: ...Third party documentation Appendix OPERATING MANUAL CP 3 5 V2 9007202252815371_v1 0_EN US...
Страница 335: ...Appendix OPERATING MANUAL CP 3 5 V2 9007202252815371_v1 0_EN US...
Страница 350: ...G DEL AG Industrie Nord CH 4900 Langenthal Switzerland Phone 41 62 916 91 91 info ch gudel com www gudel com...