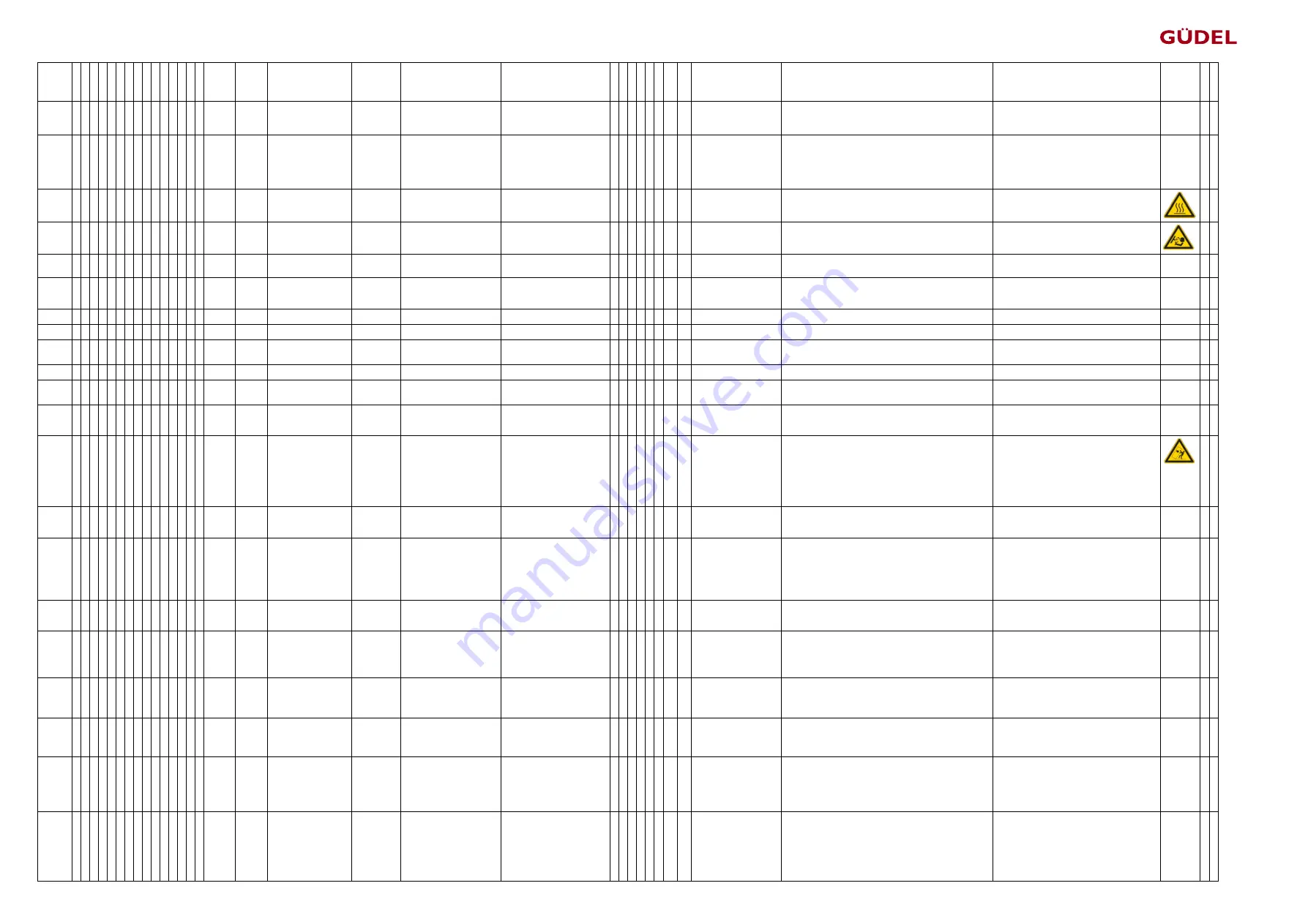
Hazard analysis / Risk analysis
Customer:
Machine type: CP with/without control system
Project no.:
Document no.:
Risk assessment / safety goals / protective measures / residual risks
1)
Solution suggested to the customer (cursive, Times New Roman)
Güdel solution (Arial)
1.14
x
x x x
x x x x x
x
x
Risk of injury (cutting,
crushing) gearbox, racks
Technician,
commissioning
technician,
forwarding agent
Carelessness
Cutting injuries, crush injuries
x
x
1
1/b Cutting and crush injuries occur
Wearing proper protective clothing
Application-specific protective measures
Y
1.15
x
x
x
x
x
x
Rotating parts
All
Contact with rotating parts
Persons are injured
x x
10 3/d Injuries occur
Attach protective cover or warning symbol
Wearing protective clothing
x Y
1.16
x
x
x
Manual workstations
Operators
Automatic movements at the
manual workstation
Someone is surprised by the
automation, body parts are crushed
and injuries result.
x
x
20 3/d Operating personnel or third
parties are injured during the
manual insertion or ejection of
the workpieces.
Insertion or ejection axes may only be moved in jog mode or with two-hand
operation. The drive configuration is such that only a slow axis speed is achieved
at maximum speed of the drive motor. The operating elements for insertion and
ejection must be configured so that the operator has a clear view of the movement
and cannot be endangered. Areas where body parts could be crushed are to be
prevented with design measures to the greatest possible extent.
Extra attention is required of the operator at manual
workstations.
Only perform movements if no other person is in the danger area
and none of your own body parts are in the line of danger of the
corresponding axis
x Y
1.17
x
x x
x x x x x x x
x
x
Hot surfaces.
All
During normal operation,
touching hot surfaces.
Person is injured by hot surface.
x
x
8
2/c Persons suffer burns.
Hot surfaces are covered by mechanical protective devices or marked by the
operator.
None
x Y
1.18
x x x x
x x x x x x x x
x
x
Hot oil squirted out due to
high pressure at the gearbox
All
Overload or non-compliance with
the intended use
Burns or eye injuries
x x
10 3/d Oil comes out.
Use of the product within the defined parameters.
Wearing protective clothing, in particular helmet, goggles, and
shoes
x Y
1.19
x
x
x
x
x
No, wrong, or insufficient
oil
Technicians,
Maintenance
personnel
Improper oil change
Failure of the transfer function as well
as increased temperature, resulting in
damage and injuries
x x
10 3/d Consequential damage occurs,
with injuries
Maintenance instructions must be observed
None
x Y
1.20
x x x
x x
x x x x
x
x
Oil running out due to leaks
all
Failure of the gasket
Environmental damage, slipping
hazard as well as consequential
damage due to the insufficient oil (see
1.18)
x x
10 3/d The occurrence of
consequential damage with
injuries and environmental
damage
Maintenance intervals must be maintained
Application-specific protective measures
x Y
1.21
x
x
x
x x
x
x
Wear (tooth breakage)
gearbox
all
Tooth breakage
Transfer function fails, resulting in
consequential damage with injuries
x x
10 3/d Consequential damage occurs,
with injuries
Maintenance intervals must be maintained
Application-specific protective measures
x Y
1.22
x
x
x
x
x
Noise
all
Overload or non-compliance with
the intended parameters
Unpleasant noise level, difficult
communication
x
x
2
1/b Excessive noise level occurs
Use of the product within the defined parameters. Vibrations and resonances must
be prevented.
None
Y
1.23
x
x x x x
x
x
Malfunction of protection
measures
Operators,
Maintenance
personnel
Aging, fatigue fracture, failure due
to vibration or overloading
Someone is surprised by the
unexpected situation and injured as a
result
x x
10 3/d A preventable hazard occurs.
The system is equipped with emergency off devices that trigger an emergency off of
the system. A lock-out (overview of the switch off locations) draws attention to the
switch-off devices.
Do not walk under suspended workpieces or vertical axes. Only
possible in setup mode. Permanent workstations are not
permitted in the direction of movement of the axes.
x Y
1.24
x
x x x x x x x x
x
Slipping
All
Inattention and/or careless
operation
Persons are injured
x
x
4
2/c Injuries occur
For the option of walkable drive axes, use anti-slip plates.
Otherwise, walking on the drive axis is contrary to intended use.
None
x Y
1.25
x
x x x x x x x x
x
x
Danger of tripping
All
Inattention and/or careless
operation
Persons are injured
x
x
4
2/c Injuries occur
Customer must provide for sufficient protection in accordance with the ambient
conditions.
None
x Y
1.26
x
x
x
x
Faulty assembly
All
Incorrectly assembled system
Someone is surprised by the
unexpected situation and injured as a
result
x x
10 3/d The module is mounted
incorrectly.
The content of the operating manual is known to the technicians.
Before a Güdel device is transported to the operation site, unpacked, assembled,
and commissioned, the operating manual must first be read and understood.
None
x Y
1.27
x
x
x
x
Loss of stability
All
Inattention and/or careless
operation
Machine/System tips over
x x
10 3/d It is possible for the module to
tip or equipment to fall down.
Equipment without base supports:
To connect to customer supports, the specified screw configuration according to
the Güdel layout has to be used with the corresponding screws.
Equipment with base supports:
The supplied screws for assembly have to be used. For the connection of the
uprights to the floor, the anchoring suggestion according to the Güdel layout
needs to be taken into consideration.
Fall protection has to be mounted for area gantries.
The operating manual must be read and understood.
Check the connections that are responsible for the stability of the
device before starting the system.
x Y
1.28
x
x
x
Improper disposal can cause
environmental damage.
All
Disposal regulations are not
observed
Environmental hazard
x x
10 3/d The device and its
consumables are not disposed
of properly at the end of their
service life.
National regulations regarding disposal of the system must be observed.
None
x Y
1.29
x
x
x
Malfunction of the control
system
Setters
Failure of control unit components
Someone is surprised by the
unexpected movement and injured as
a result
x x
10 3/d The risk of potential hazards
becomes too high.
Only drive systems are used that comply with the state of the art and the standards
referenced in the machine directive.
Work in this condition requires a high level of individual
responsibility from the operator/setter.
There is no way to completely ensure that a malfunction of the
control system does not create a hazard by movement the axes.
The operator must therefore try to never be in the possible
direction of travel of the axes and ensure that no third parties
are in the possible danger zones.
x Y
1.30
x
x
x
Malfunction of the control
system
Operators,
Maintenance
personnel
Failure of control unit components
Someone is surprised by the
unexpected movement and injured as
a result
x x
10 3/d The effects of a control system
malfunction endanger the
operator or third parties.
The areas of movement are to be enclosed by mechanical safety fences, light
curtains and light grids so that it is not possible to enter this area from any side.
Movements must transition to static states as quickly as possible.
In normal operation, all protective hoods must be closed,
removable protective hoods must be screwed securely.
Required conduct: Inspect the protective hoods before starting
normal operation.
x Y
1.31
x
x
x x x x x
x
x
Electrical hazard
Operators,
Maintenance
personnel,
Technicians
Touching the machine
Defective insulation
Improper el. installation
Unsuitable components
Someone suffers an electric shock and
is injured or killed as a result.
x x
10 3/d Operating personnel or third
parties are injured by direct or
indirect electrical contact.
Only contact-protected components are to be used.
Before working on electrical installations, always disconnect the system (plug/main
switch) and double check.
Work on electrical installations, switch cabinets and devices may only be
performed by authorized technicians.
Control cabinet fuses
Work on electrical installations requires expertise and extra
care.
x Y
1.32
x
x
x
Disruption of the energy
supply
Operators,
Maintenance
personnel
Power failure, lightning, interrupted
compressed air supply
Someone is surprised by the
unexpected movement and injured as
a result
x x
10 3/d The effects of a power failure
endanger the operator or third
parties.
The movement of the drives is mechanically limited in case the supply voltage fails
(mechanical limit stops and holding brakes).
The movement of the drives is braked if the supply voltage fails. The operator and
third parties are outside the danger area.
After a crash, defective elements of the mechanical limit stops
cannot necessarily be recognized immediately. The entire
bumper unit must always be replaced.
x Y
1.33
x
x
x
x
Disruption of the energy
supply
Setters
Power failure, lightning, interrupted
compressed air supply
Someone is surprised by the
unexpected situation and injured as a
result
x x
10 3/d The effects of a power failure
endanger the operator or third
parties.
The movement of the drives is limited by mechanical limit stops in case the supply
voltage fails. The drives have already been switched off in case of a power failure
(safety shutdown situation). The movement of the drives is braked in case of supply
voltage failure by the motor brake or holding brake in the drive train.
After a crash, defective elements of the mechanical limit stops
cannot necessarily be recognized immediately. The entire
bumper unit must always be replaced.
x Y
1.34
x
x
x x x
x x
x
Falling or flung out parts
Operators,
Maintenance
personnel,
Setters,
Commissioning
technicians
Forced fracture of components or
mounting elements if the X-carrier -
with Y-axis not retracted - runs
against a different carriage or
against an obstacle (crash) in the
end position damper.
Persons are injured or killed by falling
or flung about parts.
x x
10 3/d In case of a crash, falling or
ejected parts can injure or kill
persons.
Mechanical guards are available against parts that could fall or fly away.
The protective equipment is inspected by means of calculation and trial.
The gantry can no longer be operated safety following a crash.
The gantry must be taken out of operation and contact be made
with Güdel before putting it back into operation.
After a crash, defective elements cannot be detected easily. In
any case, a general inspection in the sense of a fine check must
be carried out.
x Y
1.35
x
x
x x x
x x
x
Falling or flung out parts
Operators,
Maintenance
personnel,
Setters,
Commissioning
technicians
Forced fracture of components or
fastening elements due to overload
at e-stop or crash with extended Y-
and/or Z-axis.
Persons are injured or killed by falling
or flung about parts.
x x
10 3/d In case of a crash or an e-stop,
falling or ejected parts can
injure or kill persons.
The axes are protected against separation from the rest of the system by a fall
protection device.
Mechanical guards are available against parts that could fall or fly away.
The protective equipment is inspected by means of calculation and trial.
To protect against mechanical overload, the drive torques for all operating modes
must be limited in accordance with the operating manual
=> Reference to torque limitation of the module configurator
The gantry can no longer be operated safety following an
overload. The gantry must be taken out of operation and contact
be made with Güdel before putting it back into operation.
After an overload, defective elements cannot be detected easily.
In any case, a general inspection in the sense of a fine check
must be carried out.
x Y
Author: Alain Thurner
Created: 11.12.2009
Process owner: Michael Marti
Approved: 11.06.2019 / Version 01
Page 2 of 3
Risikobeurteilung_Module CP_2019_06_11_EN.xlsx
Содержание CP 3-5 V2
Страница 4: ...Revision history OPERATING MANUAL CP 3 5 V2 9007202252815371_v1 0_EN US 4...
Страница 15: ...Options Third party documentation Table of contents OPERATING MANUAL CP 3 5 V2 9007202252815371_v1 0_EN US 15...
Страница 16: ...Table of contents OPERATING MANUAL CP 3 5 V2 9007202252815371_v1 0_EN US 16...
Страница 34: ...Safety OPERATING MANUAL CP 3 5 V2 9007202252815371_v1 0_EN US 34...
Страница 42: ...Design function OPERATING MANUAL CP 3 5 V2 9007202252815371_v1 0_EN US 42...
Страница 52: ...Transport OPERATING MANUAL CP 3 5 V2 9007202252815371_v1 0_EN US 52...
Страница 130: ...Operation OPERATING MANUAL CP 3 5 V2 9007202252815371_v1 0_EN US 130...
Страница 216: ...Maintenance OPERATING MANUAL CP 3 5 V2 9007202252815371_v1 0_EN US 216...
Страница 217: ...9 4 Maintenance schedules Maintenance OPERATING MANUAL CP 3 5 V2 9007202252815371_v1 0_EN US 217...
Страница 218: ...Maintenance OPERATING MANUAL CP 3 5 V2 9007202252815371_v1 0_EN US 218...
Страница 220: ...Maintenance OPERATING MANUAL CP 3 5 V2 9007202252815371_v1 0_EN US 220...
Страница 222: ...Maintenance OPERATING MANUAL CP 3 5 V2 9007202252815371_v1 0_EN US 222...
Страница 224: ...Maintenance OPERATING MANUAL CP 3 5 V2 9007202252815371_v1 0_EN US 224...
Страница 228: ...Maintenance OPERATING MANUAL CP 3 5 V2 9007202252815371_v1 0_EN US 228...
Страница 230: ...Maintenance OPERATING MANUAL CP 3 5 V2 9007202252815371_v1 0_EN US 230...
Страница 232: ...Maintenance OPERATING MANUAL CP 3 5 V2 9007202252815371_v1 0_EN US 232...
Страница 234: ...Maintenance OPERATING MANUAL CP 3 5 V2 9007202252815371_v1 0_EN US 234...
Страница 236: ...Maintenance OPERATING MANUAL CP 3 5 V2 9007202252815371_v1 0_EN US 236...
Страница 264: ...Repairs OPERATING MANUAL CP 3 5 V2 9007202252815371_v1 0_EN US 264...
Страница 266: ...Repairs OPERATING MANUAL CP 3 5 V2 9007202252815371_v1 0_EN US 266...
Страница 272: ...Decommissioning storage OPERATING MANUAL CP 3 5 V2 9007202252815371_v1 0_EN US 272...
Страница 277: ...13 Spare parts supply Spare parts supply OPERATING MANUAL CP 3 5 V2 9007202252815371_v1 0_EN US 277...
Страница 278: ...Spare parts supply OPERATING MANUAL CP 3 5 V2 9007202252815371_v1 0_EN US 278...
Страница 284: ...Spare parts supply OPERATING MANUAL CP 3 5 V2 9007202252815371_v1 0_EN US 284...
Страница 302: ...List of illustrations OPERATING MANUAL CP 3 5 V2 9007202252815371_v1 0_EN US 302...
Страница 306: ...List of tables OPERATING MANUAL CP 3 5 V2 9007202252815371_v1 0_EN US 306...
Страница 316: ...Appendix OPERATING MANUAL CP 3 5 V2 9007202252815371_v1 0_EN US...
Страница 317: ...Hazard analysis Risk analysis Appendix OPERATING MANUAL CP 3 5 V2 9007202252815371_v1 0_EN US...
Страница 318: ...Appendix OPERATING MANUAL CP 3 5 V2 9007202252815371_v1 0_EN US...
Страница 322: ...Addition to declaration of incorporation Appendix OPERATING MANUAL CP 3 5 V2 9007202252815371_v1 0_EN US...
Страница 323: ...Appendix OPERATING MANUAL CP 3 5 V2 9007202252815371_v1 0_EN US...
Страница 326: ...Technical data Appendix OPERATING MANUAL CP 3 5 V2 9007202252815371_v1 0_EN US...
Страница 327: ...Appendix OPERATING MANUAL CP 3 5 V2 9007202252815371_v1 0_EN US...
Страница 328: ...Layout Appendix OPERATING MANUAL CP 3 5 V2 9007202252815371_v1 0_EN US...
Страница 329: ...Appendix OPERATING MANUAL CP 3 5 V2 9007202252815371_v1 0_EN US...
Страница 330: ...Spare parts lists Appendix OPERATING MANUAL CP 3 5 V2 9007202252815371_v1 0_EN US...
Страница 331: ...Appendix OPERATING MANUAL CP 3 5 V2 9007202252815371_v1 0_EN US...
Страница 332: ...Options Appendix OPERATING MANUAL CP 3 5 V2 9007202252815371_v1 0_EN US...
Страница 333: ...Appendix OPERATING MANUAL CP 3 5 V2 9007202252815371_v1 0_EN US...
Страница 334: ...Third party documentation Appendix OPERATING MANUAL CP 3 5 V2 9007202252815371_v1 0_EN US...
Страница 335: ...Appendix OPERATING MANUAL CP 3 5 V2 9007202252815371_v1 0_EN US...
Страница 350: ...G DEL AG Industrie Nord CH 4900 Langenthal Switzerland Phone 41 62 916 91 91 info ch gudel com www gudel com...