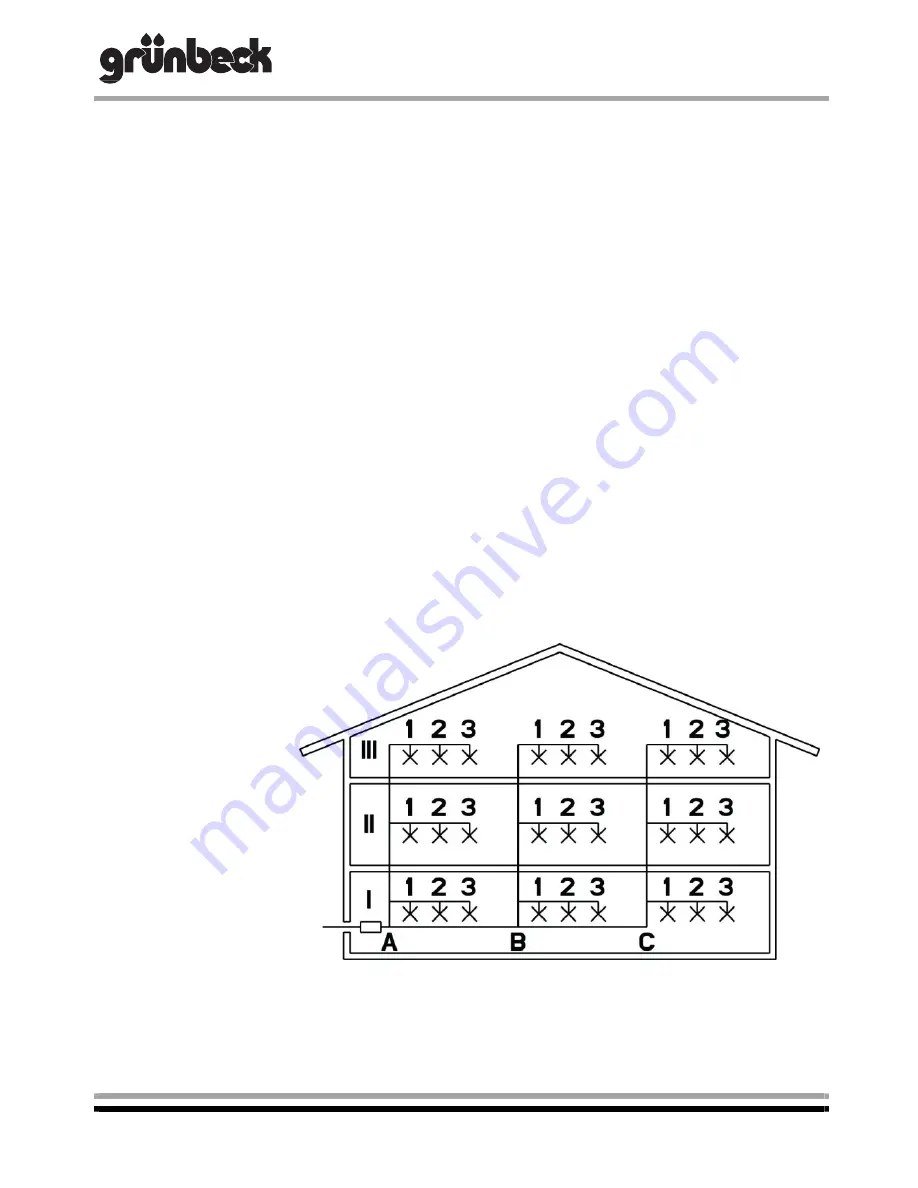
GENO
®
-flushing compressor 1988 K
Order no. 015 151 963-inter Created: KONS-gmei-mrie G:\BA-151963-INTER_GENO-SPUELKOMP-1988_K.DOC
41
6.
In the case of low water pressure, it may be necessary to integrate a
pressure booster when flushing in order to achieve the necessary
minimum flow speed. A sufficient flow speed and the correct inlet
pressure are important for the success of flushing. We recommend a
water inlet pressure of approx. 4-5 bar. Pressure-reducing fittings
(e.g., pressure regulators) which reduce the inlet pressure to below
the recommended pressure should thus be removed.
Under ideal conditions, the compressed air bubble which is fed in is
kept short, water turbulence is ensured and the dirt is discharged. If
the inlet pressure is not sufficient or the flow rate is low, the air
bubble expands too quickly and, consequently, the water and air
are unmixed which reduces the effectiveness of cleaning.
7.
Determine the flushing sections. Depending on the size of the
installation and how the piping is arranged, the installation may
have to be flushed in sections. The maximum flushing section length
must not exceed 100 m. We recommend providing for separation
points when planning and installing and also fitting adjusting pieces
(see accessories).
8.
Determine the flushing order. Flushing must be performed starting
with the nearest withdrawal point and finishing with the point
which is furthest away. Accordingly, the ascending pipes are to be
flushed in the following order, A, B and then C. The floor lines are
flushed starting with I, then II and then III as well as in the floor lines
from 1 to 3 to ensure that contamination is flushed out of the
installation via the shortest route, see Fig. D-16.
Fig. D-16: Flushing order of the installed sections