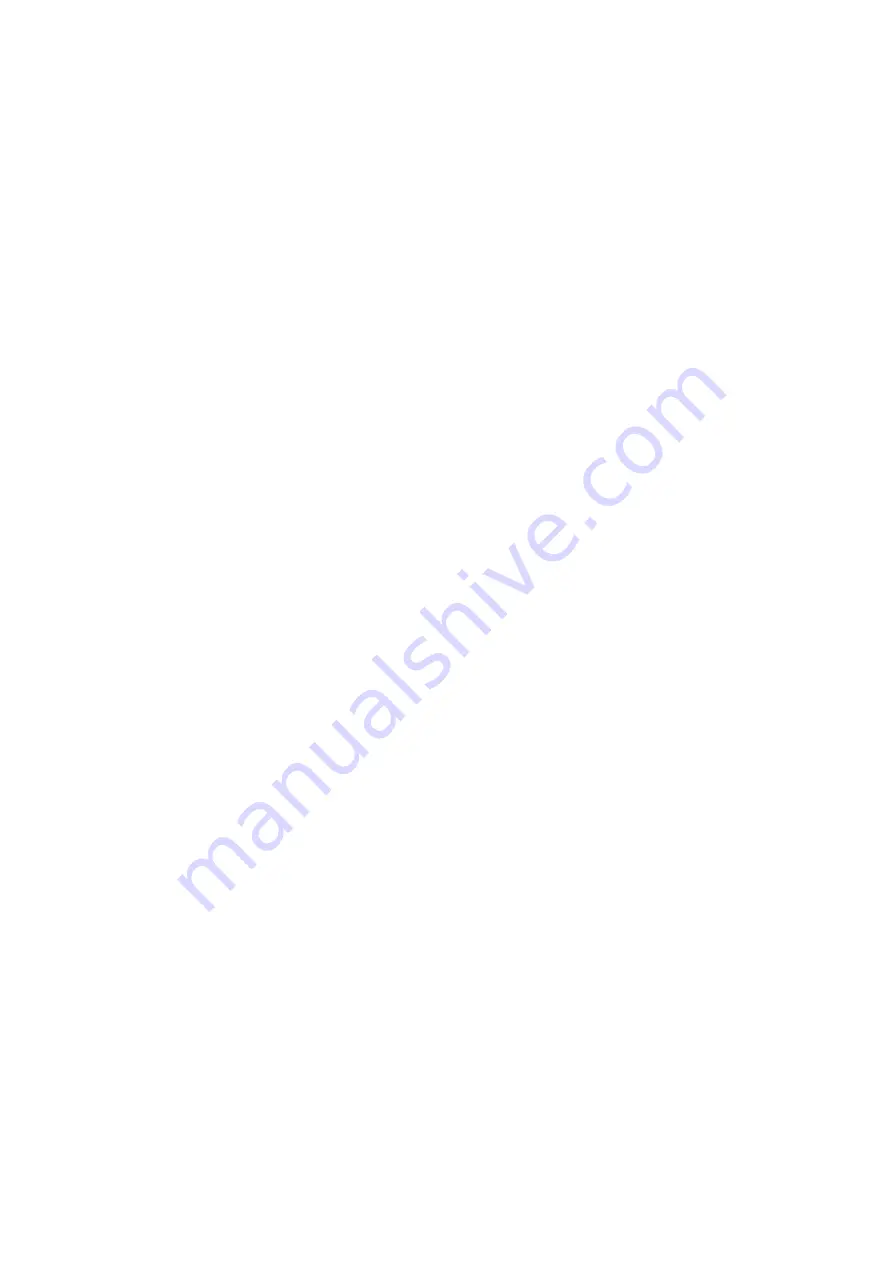
Figure M—8: Locking piece with fittings (left) ¦¦ tightened with a nut spinner (right)
Figure M—9: Bottom isolators with partially unscrewed fittings
....................................................... 73
Figure M—10: Isolator with fittings (left) ¦¦ tightened with spanner (right)
......................................... 73
Figure M—11: Clockwise: Isolators with fittings ¦¦ back fittings tightened with spanner ¦¦ front
fittings tightened with nut spinner
............................................................................... 74
Figure M—14: Rear view of LCD display board with cable attached
................................................. 75
Figure M—15: Fitting PGA locks
Figure M—16: Reconnect LCD display board cable
............................................................................ 77
Figure M—18: Loosen isolator front nut with nut spinner
................................................................. 78
Figure M—19: Loosen isolator rear outer nut with spanner
.............................................................. 78
Figure M—20: Bottom isolator with fittings removed
......................................................................... 78
Figure M—21: Unscrew the failsafe bolt
............................................................................................. 79
Figure M—22: Loosen the isolator M6 nut using a nut spinner
......................................................... 79
Figure M—23: Inverted top locking piece
............................................................................................ 80
Figure M—24: Bottom locking piece
Figure M—25: Surplus nuts & washers stored securely on bracket bolts
......................................... 80
Figure M—27: Rear view of LCD display board with cable attached
................................................. 82
Figure M—28: Slide out PGA lock
Figure M—31: PGA locks secured using Allen key
.............................................................................. 83
Figure M—32: Reconnect LCD board cable
........................................................................................ 84
List of Tables
Table 4—1: Technical specification
Table 11—1: Product communications channels
............................................................................... 34
Table L—1: MINI DM-Cradle retrofit kit — KITT00071
......................................................................... 57
Table L—2: Bracket tools and fittings
Table L—3: Top isolators tools and fittings
......................................................................................... 60
Table L—4: Bottom isolators tools and fittings
................................................................................... 62
Table L—5: Failsafe tools and fittings