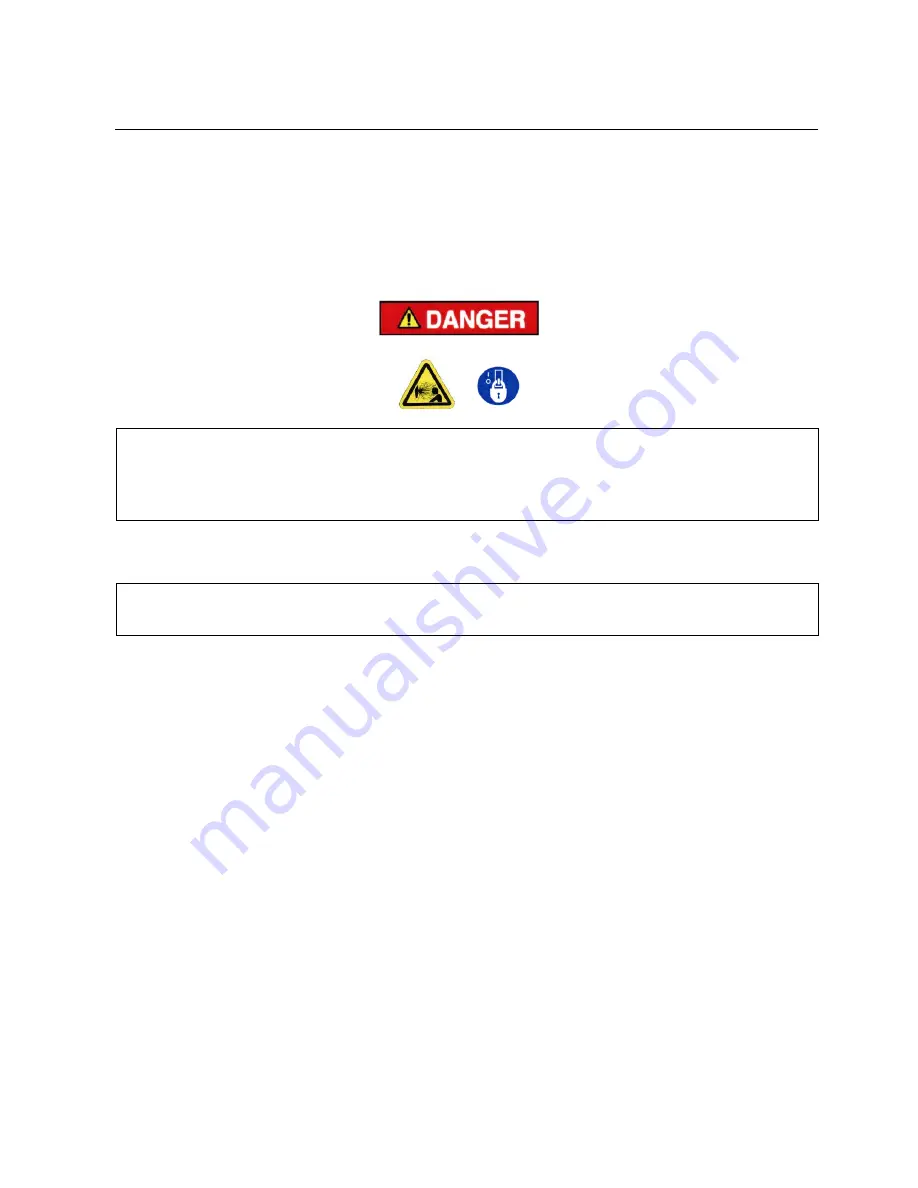
13-17-618 Page 65
9-1
SECTION 9
MINIMUM PRESSURE/CHECK VALVE
MINIMUM PRESSURE/CHECK VALVE
-
This device maintains minimum pressure within the air/oil
reservoir, thus insuring [cooling/lubricating] oil injection flow into the compressors. It also serves as a
check valve to prevent back flow of compressed air flow from the customer’s piping or pipe network back
into the compressor package when the compressor is not active. The valve does not require
maintenance or adjustment. If the valve fails to function, check the valve stem O-ring for sealing, valve
orifices for restriction, or valve and valve seat for burrs and dirt.
Repair kits are available from your local
authorized Gardner Denver distributor.
Before servicing the minimum pressure valve, always stop the unit, release air
pressure, lockout and tagout the power supply to the compressor package.
Failure to release pressure or properly disconnect the power may result in
personal injury or death.
Working spring within valve body is under tension. Failure to relieve spring
tension gradually may cause serious injury upon cap removal.
Minimum Pressure/Check Valve Inspection:
1. Be sure the unit is completely off and that the oil reservoir is depressurized.
2. Disconnect, lockout and tagout power supply to the compressor package.
3. Carefully and gradually unscrew the valve cap from the body
– this will also release tension from
working spring within valve body. After cap removal, all internal parts can be retrieved
– note their
relative positions during disassembly to help the re-assembly process. See Figure 9-1, page 66
4. Inspect and/or replace parts.
5. Re-assemble by following steps 4 to 3 in reverse order.
Содержание VST55-90B
Страница 33: ...13 17 618 Page 32 4 5 Figure 4 2 PIPING AND INSTRUMENTATION ILLUSTRATION 300ETK797 C Ref Drawing ...
Страница 67: ...13 17 618 Page 66 9 2 Figure 9 1 MINIMUM DISCHARGE PRESSURE CHECK VALVE ...
Страница 81: ...NOTES ...
Страница 82: ...NOTES ...
Страница 83: ...NOTES ...