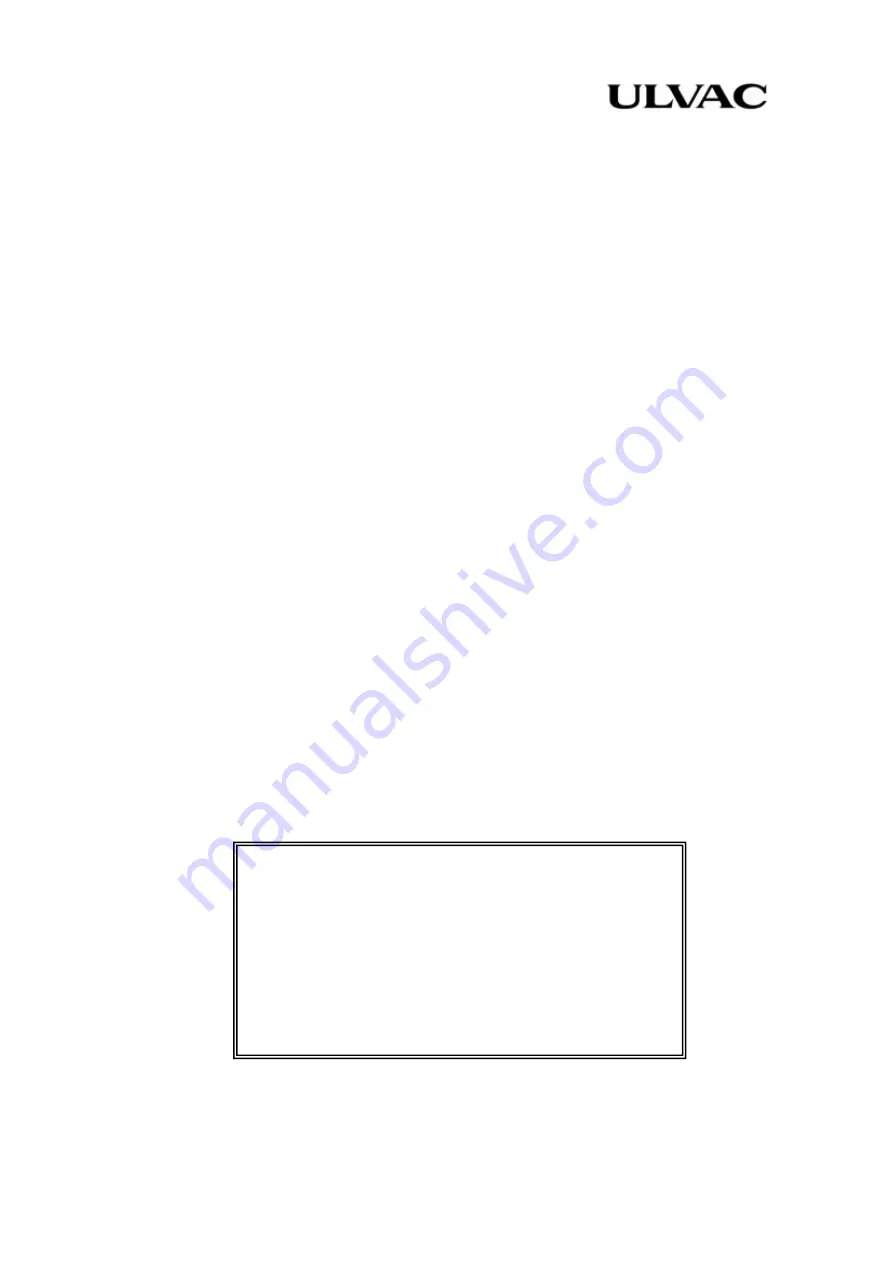
C30V
_
R
series Compressor Unit
for Cryopump and Super Trap
Installation, Operation,
Maintenance, and Troubleshooting
Instructions
C30V
_
R, C30V
_
RT, C30PV
_
RT
C30MV
_
R, C30MV
_
RT
C30MVE
_
R, C30MVE
_
RT
Export Control Policy
Vacuum pumps that pump nitrogen gas at pumping
speed of 15000L/S or more fall under row 2(35) of
appended table 1 of Japan’s Export Trade Control Order,
which is based on international export control regimes.
Customers must follow all related rules and regulations
such as Foreign Exchange and Foreign Trade Act and
take appropriate procedures when exporting or
re-exporting those products.
D/N.MD30XVRE, 2018MH19
ULVAC CRYOGENICS INCORPORATED
Summary of Contents for C30MVER
Page 2: ......
Page 8: ...F 6 ULVAC CRYOGENICS INCORPORATED This page intentionally left blank ...
Page 16: ...S 4 ULVAC CRYOGENICS INCORPORATED This page intentionally left blank ...
Page 18: ...IW 2 ULVAC CRYOGENICS INCORPORATED This page intentionally left blank ...
Page 108: ...CS 2 ULVAC CRYOGENICS INCORPORATED This page intentionally left blank ...
Page 110: ...Revision History R 2 ULVAC CRYOGENICS INCORPORATED This page intentionally left blank ...