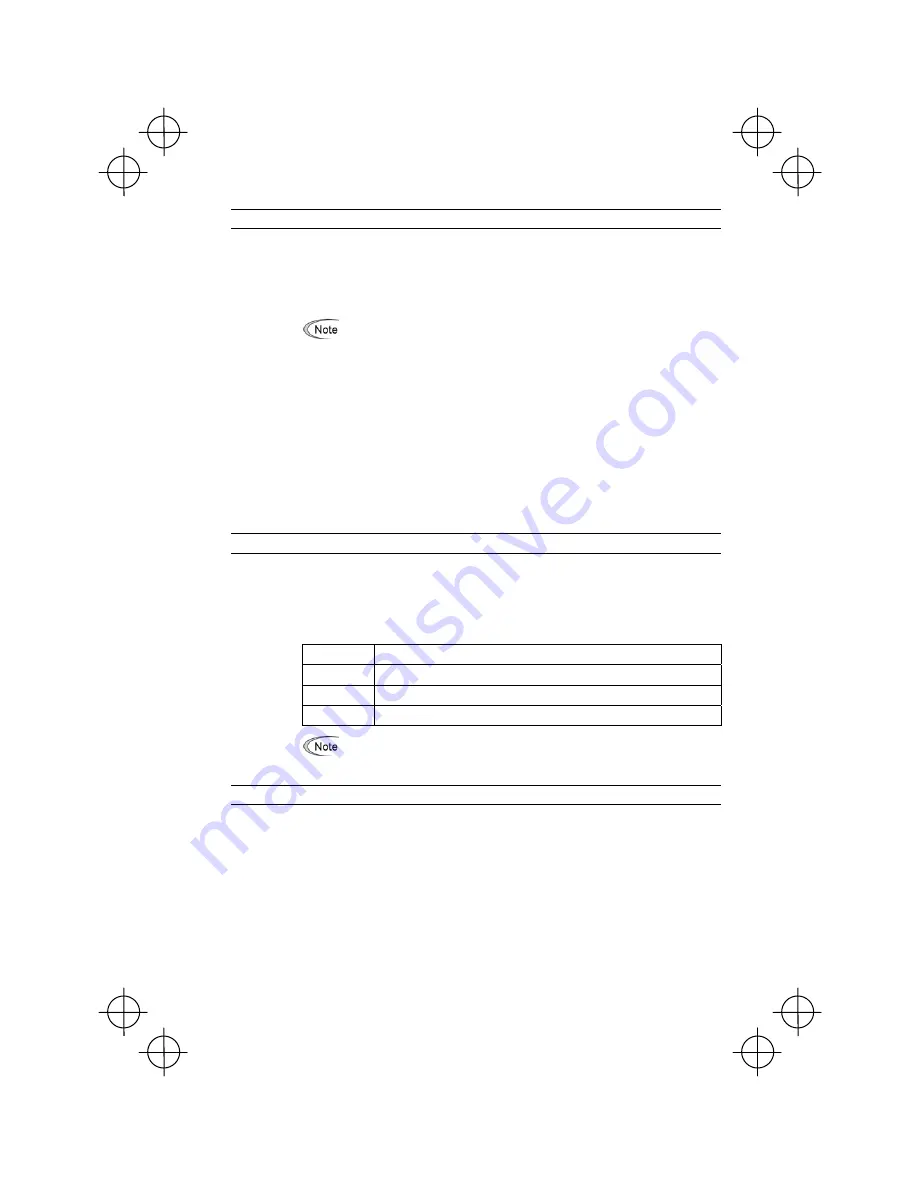
5-71
H69
Automatic Deceleration
H69 specifies whether automatic deceleration control is to be enabled or disabled. During
deceleration of the motor, if regenerative energy exceeds the level that can be handled by the
inverter, overvoltage trip may happen. With automatic deceleration enabled, when the DC link
bus voltage exceeds the level (internally fixed) for starting automatic deceleration, the output
frequency is controlled to prevent the DC link bus voltage from rising further; thus regenerative
energy is suppressed.
If automatic deceleration is enabled, deceleration may take a longer time. This is
designed to limit the torque during deceleration, and is therefore of no use where there
is a braking load.
Disable the automatic deceleration when a braking unit is connected. The automatic
deceleration control may be activated at the same time when a braking unit starts
operation, which may make the acceleration time fluctuate. In case the set deceleration
time is so short, the DC link bus voltage of the inverter rises quickly, and consequently,
the automatic deceleration may not follow the voltage rise. In such a case, prolong the
deceleration time.
Even if the time period of 3 times of the deceleration time 1 (F08) has elapsed after the
inverter entered automatic deceleration, there may be a case that the motor does not
stop or the frequency dose not decrease. In this case, cancel the automatic
deceleration forcibly for safety and decelerate the motor according to the set
deceleration time. Prolong the deceleration time also.
H70
Overload Prevention Control
H70 specifies the rate of decreasing the output frequency to prevent an overload condition.
Under this control, an overload trip is prevented by decreasing the output frequency of the
inverter before the inverter trips because of the overheating of the cooling fan or the overloading
of the inverter (with an alarm indication of
0h1
or
0lu
). This control is useful for facilities such
as pumps where a decrease in the output frequency leads to a decrease in the load and it is
necessary to keep the motor running even when the output frequency goes low.
Data for H70
Function
0.00
Decelerate the motor by deceleration time 1 specified by F08
0.01 to 100.0
Decelerate the motor by deceleration rate 0.01 to 100.0 (Hz/s)
999
Disable overload prevention control
In applications where a decrease in the output frequency does not lead to a decrease in
the load, this function is of no use and should not be enabled.
H91
PID control feedback line disconnection detection protection
After H91 is set from 0.1 to 60.0 and all of the condition as below are satisfied for set time, “CoF”
alarm comes ON. When H91 is set to 0.0s, “CoF” alarm does not come ON by disconnection
detection.
-The input current on the terminal C1 is less than 2mA.
-The terminal C1 is used for the feedback input value of PID control (E62=5).
-Under the PID control.
Содержание FRENIC-ECO
Страница 111: ...5 3 F codes Fundamental Functions The shaded function codes are applicable to the quick setup...
Страница 114: ...5 6 F code continued...
Страница 115: ...5 7 E codes Extension Terminal Functions...
Страница 116: ...5 8 E code continued...
Страница 119: ...5 11 E code continued...
Страница 121: ...5 13 P codes Motor Parameters The shaded function codes are applicable to the quick setup...
Страница 122: ...5 14 H codes High Performance Functions...
Страница 123: ...5 15 H code continued...
Страница 126: ...5 18 J code continued...
Страница 127: ...5 19 J code continued...
Страница 128: ...5 20 y codes Link Functions...
Страница 129: ...5 21 y code continued...
Страница 141: ...5 33 Example of Operating Characteristics...
Страница 217: ...8 6 8 3 Common Specifications...
Страница 218: ...8 7...
Страница 223: ...8 12 8 5 External Dimensions 8 5 1 Standard models Unit inch mm 10 2 260...
Страница 227: ...8 16 8 5 3 Multi function Keypad Unit inch mm...
Страница 246: ...Fuji Electric FA Components Systems Co Ltd Fuji Electric Corp of America 2007 11 K07 K07 10CM...