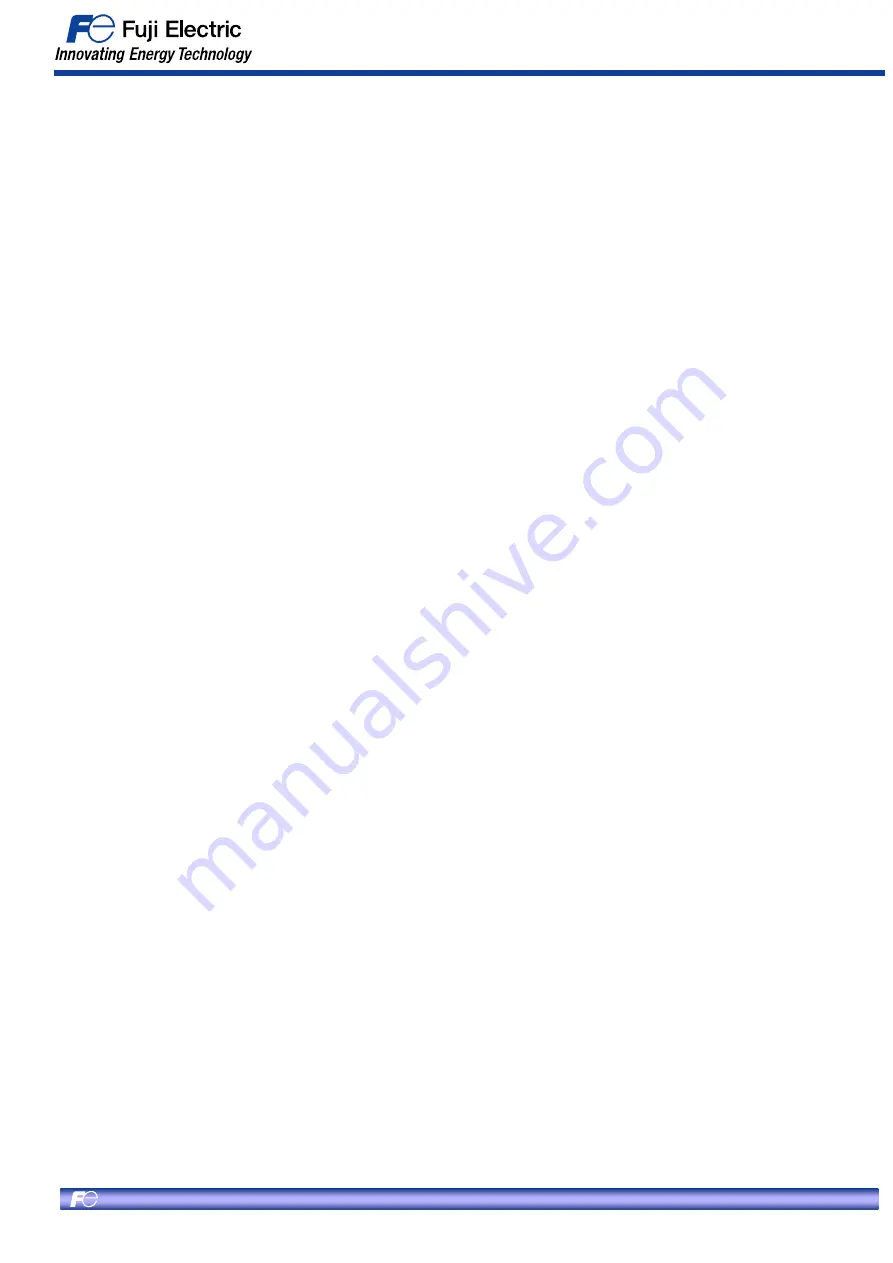
5-4
Fuji Electric Co., Ltd.
MT6M12343 Rev.1.0
Dec.-2016
Chapter 5
Recommended wiring and layout
1.
Input signal for IGBT driving is High-Active. The input circuit of the IC has a built-in pull-down
resistor. To prevent malfunction, the wiring of each input should be as short as possible. When
using RC filter, please make sure that the input signal level meets the turn-on and turn-off threshold
voltage.
2.
The IPM has built-in HVICs and thus it is possible to be connected to a microprocessor (MPU)
directly without any photocoupler or pulse transformer.
3.
VFO output is open drain type. It should be pulled up to the positive side of a 5V power supply by a
resistor of about 10k
W
.
4.
To prevent erroneous protection, the wiring of (A), (B), (C) should be as short as possible.
5.
The time constant R2-C2 of the protection circuit should be selected approximately 1.5
s.
Over current (OC) shut down time might vary due to the wiring pattern. Tight tolerance, temp-
compensated type is recommended for R2, C2.
6.
It is recommended to set the threshold voltage of the comparator reference input to be same level
as the IPM OC trip reference voltage V
IS(ref)
.
7.
Please use high speed type comparator and logic IC to detect OC condition quickly.
8.
If negative voltage is applied to R1 during switching operation, connecting a Schottky barrier diode
D1 is recommended.
9.
All capacitors should be connected as close to the terminals of the IPM as possible. (C1, C4:
ceramic capacitors with excellent temperature, frequency and DC bias characteristics are
recommended; C3, C5: electrolytic capacitors with excellent temperature and frequency
characteristics are recommended.)
10.
To prevent destruction caused by surge voltage, the wiring between the snubber capacitor C6 and P
terminal, Ns node should be as short as possible. Generally, snubber capacity of 0.1
F~0.22
F is
recommended.
11.
Two COM terminals (9 & 16 pin) are connected internally. Please connect either of the terminal to
the signal GND and leave the other terminal open.
12.
It is recommended to connect a Zener diode (22V) between each pair of control power supply
terminals to prevent destruction caused by surge voltage.
13.
If signal GND is connected to power GND by board pattern, there is possibilty of malfunction due to
fluctuations at the power GND. It is recommended to connect signal GND and power GND at a
single point.
<Note>