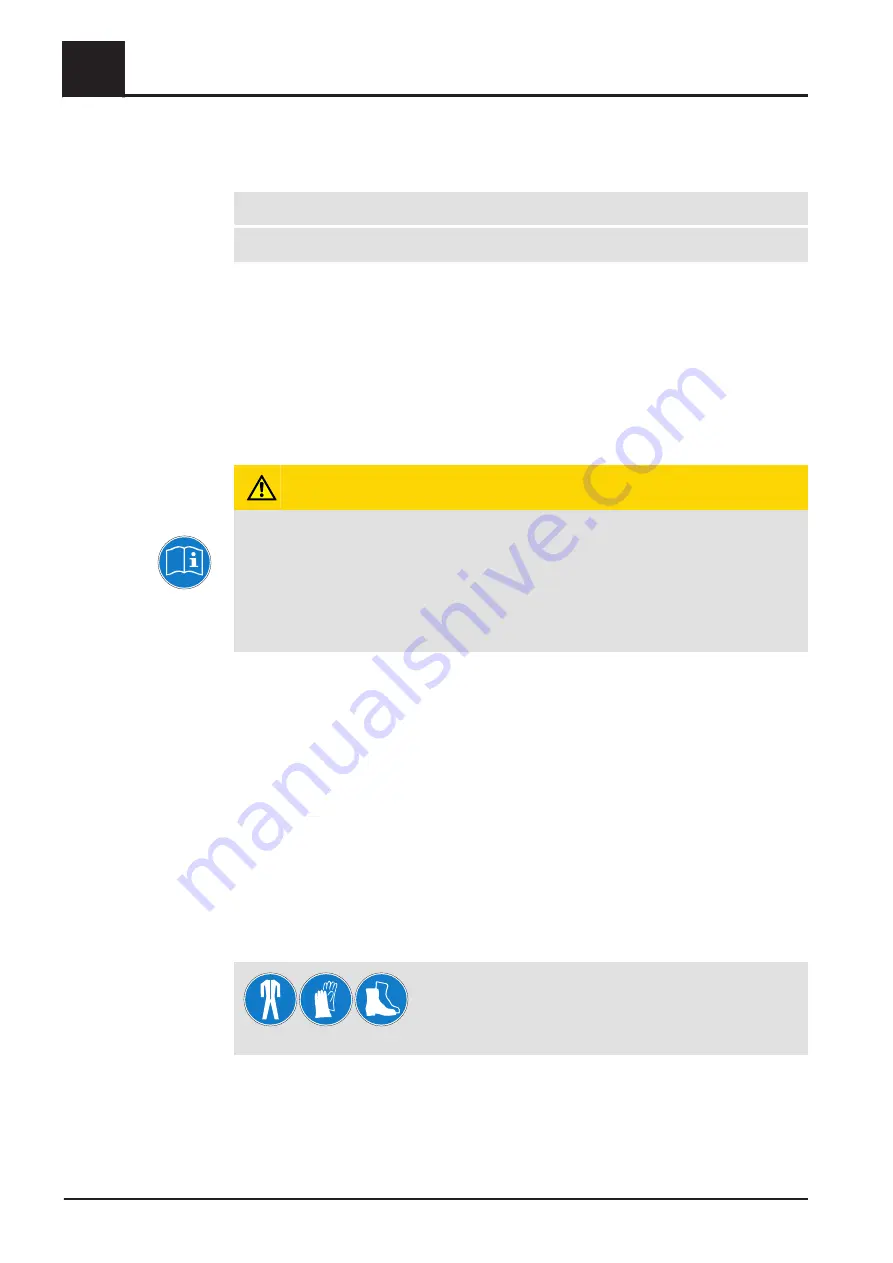
Wood pellets
Wood pellets made from natural wood with a diameter of 6 mm
EU:
Fuel acc. to EN ISO 17225 - Part 2: Wood pellets class A1 / D06
and/or:
EN
plus
/ DIN
plus
certification scheme
General note:
Before refilling the store, check for pellet dust and clean if necessary.
2.3 Qualification of staff
2.3.1 Qualification of assembly staff
CAUTION
Assembly and installation by unqualified persons:
Risk of personal injury and damage to property
During assembly and installation:
❒ Observe the instructions and information in the manuals
❒ Only allow appropriately qualified personnel to work on the system
Assembly, installation, initial startup and servicing must always be carried out by
qualified personnel:
- Heating technician / building technician
- Electrical installation technician
- Froling customer services
The assembly staff must have read and understood the instructions in the
documentation.
2.3.2 Personal protective equipment for assembly staff
You must ensure that staff have the protective equipment specified by accident
prevention regulations.
▪ For transportation, setup and assembly:
- suitable work wear
- protective gloves
- sturdy shoes (min. protection class S1P)
Note on standards
2
Safety
Permitted uses
8
Froling GesmbH | A-4710 Grieskirchen, Industriestraße 12 | www.froeling.com