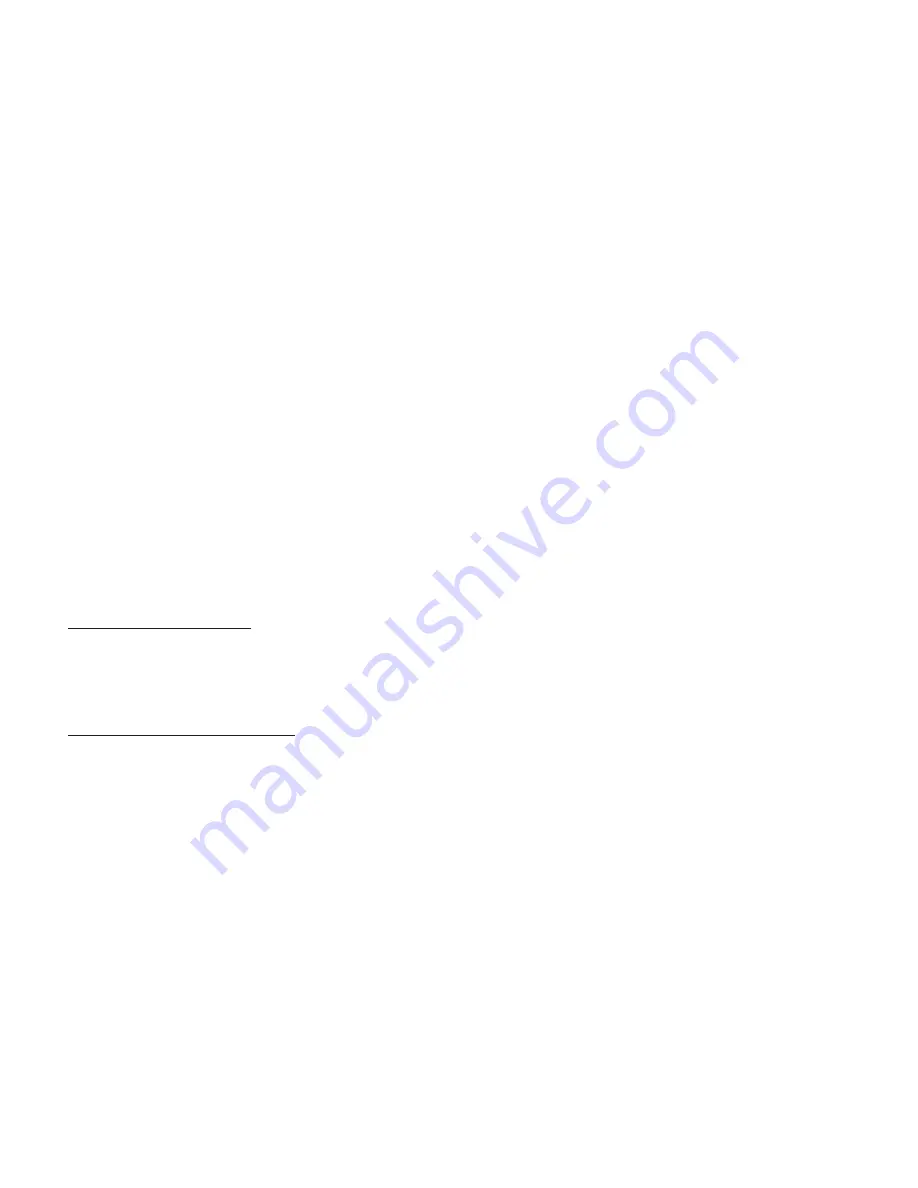
which is packed with each new seal assembly, and tap
seat and ring into place by using a light mallet with a piece
of wood placed squarely against the seat face.
Inspect the shaft sleeve
(5)
to see that it is clean and
smooth. Use emery cloth to polish the sleeve if it is
scored, or replace the shaft sleeve
(5)
if there is excessive
wear. Insert the O-ring spacer
(6a)
up to the shoulder of
the shaft. Insert the O-ring
(6)
up to the spacer sleeve,
and gently replace the shaft sleeve
(5)
.
Wipe the shaft sleeve clean, and give it a thin coating of
light oil. Slide the rotating portion of the seal assembly
onto the shaft sleeve, with carbon washer facing the
ceramic seal in the bracket. Be extremely careful when
sliding the rubber portion of the seal onto the shaft.
Concentration of force on the rubber surface can be
facilitated by using a sleeve which fi ts over the shaft and
butts up squarely against the back of the seal assembly.
Once the seal assembly is on the shaft sleeve, the force
required to push it along the shaft is greatly reduced. Be
sure to anticipate this reduction so that the carbon washer
will not be fractured by being slammed against the seat
face. Before sliding the carbon washer up against the seat
face, make certain that the lapped faces are absolutely
clean. Place the seal spring in position. Discard the seal
retainers on all models except DC4 and replace the
impeller key
(9)
and the impeller
(2)
on the shaft.
Assemble the impeller washer
(8)
and the capscrew
(7)
.
Tighten 3/8
”
capscrews to 35 ft. lbs. and 1/2
”
to 80 ft. lbs.
Reassemble the remaining components.
REPLACEMENT PARTS
Whenever replacement parts are needed for the pump,
contact your nearest pump dealer. Please give the pump
model number and serial number as stamped on the
nameplate.
IMPROPER PERFORMANCE
When investigating possible pump problems, every effort
must fi rst be made to eliminate all external infl uences.
The correct use and accuracy of instruments should
be checked. In addition, note that pump performance
is substantially affected by such fl uid characteristics as
temperature, specifi c gravity and viscosity.
NO DISCHARGE
May be caused by:
Pump not primed
System head too high
Suction lift higher than that for which pump is designed
Impeller plugged or wrong direction of rotation
Air leak in the suction line
Clogged foot valve, suction strainer or suction valve
INSUFFICIENT DISCHARGE
May be caused by:
Air leaks in suction or mechanical seal
System head higher than anticipated
INSUFFICIENT NPSHA
May be caused by:
Suction lift too high. Check with gauges. Check for
clogged suction lines or screen.
Not enough suction head for hot or volatile liquids
Foot valve too small
Impeller partially plugged
Mechanical defects: impeller damaged
INSUFFICIENT PRESSURE
May be caused by:
System head less than anticipated
Air or gas in liquid
Impeller damaged
Impeller diameter too small
Wrong direction or rotation
LOSS OF SUCTION FOLLOWING PERIOD OF
SATISFACTORY OPERATION
May be caused by:
Leaky suction line
Suction lift too high or insuffi cient NPSHA
Air or gas in liquid
Clogging of strainer or foot valve
Mechanical seal damaged
EXCESSIVE POWER CONSUMPTION
May be caused by:
Improper power to motor
System head lower than rating, pumps too much liquid
Specifi c gravity or viscosity of liquid pumped is too high
Impeller rubbing on pump casing (check end play of stub
shaft on 56C frame models)