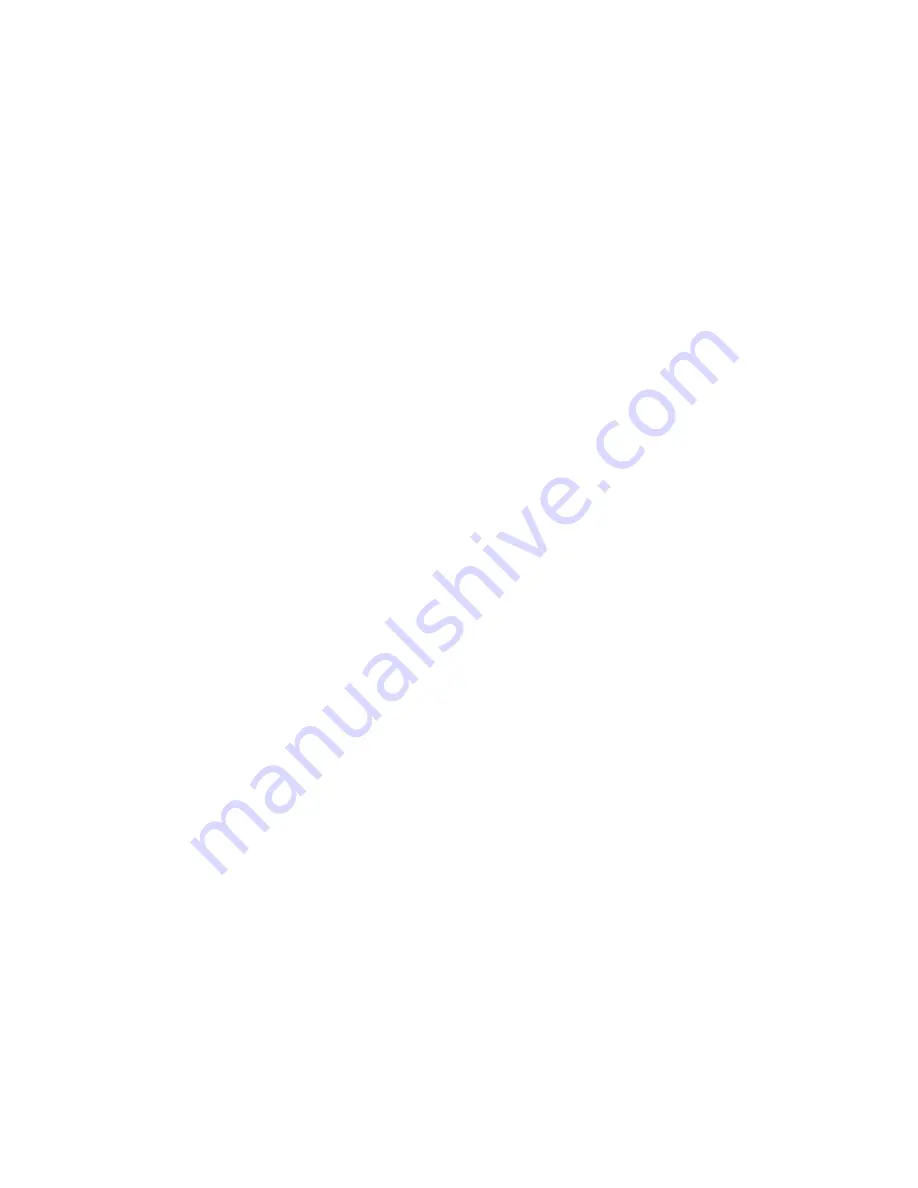
unit is level. Tighten the mounting bolts supporting the
motor on the pump bracket evenly and securely. When
connecting the suction and discharge connections, do not
impose additional strain at the pump connections;
lubricate all thread with suitable pipe dope or sealant.
PIPING
Never allow pump to carry weight of piping. Both suction
and discharge piping should be supported independently
at a point near the pump. Piping must be installed
carefully so that it will not be necessary to force it into
place when connecting to the pump.
In unusually long discharge lines, and in lines which are
subject to wide temperature ranges, slip joints or other
fl exible connectors should be used to compensate for
elongation of the pipe due to pressure or temperature.
Flexible connectors are also helpful as a means of
preventing transmission of noise and vibration.
SUCTION PIPING
The pump should be installed as close to the source of
liquid as possible. Where high suction lifts (15 feet or
more), hot liquids, or intricate suction piping are involved,
a careful check must be made to be sure that the pump’s
required net positive suction head (NPSH) will be met.
The suction line should be as short, large and simple as
practical. It should be placed so that it rises gradually
toward the pump and so that the pump suction is at the
highest point in the suction line. Use as few fi ttings as
possible and utilize smooth, long-radius fi ttings where
space permits.
Avoid attaching an elbow directly to the pump suction; use
a length of straight pipe or an eccentric reducer to provide
proper entry of liquids into pump. Do not use throttling
valves or orifi ces in suction line. They may cause
cavitation which can seriously damage the pump.
If a footvalve is required to keep the pump primed, the
cross-sectional area of its passageways should be 1½ to
2 times the area of the suction pipe. A strainer, if required
should have 3 to 4 times the area of the suction pipe;
otherwise, excessive friction loss will be caused.
It is especially important that suction piping on pumps
which operate at high suction lift be absolutely free from
leaks. If air is drawn into the suction line through any
leaks, the pump capacity will be reduced, and serious
diffi culties in maintaining prime may result.
When the suction line draws liquid from an open sump, its
lower end should be submerged suffi ciently so that air is
not drawn into the line by vortex action. A fl ared suction
bell placed on the end of vertical suction line will help to
compensate for lack of submergence.
DISCHARGE PIPING
Care should be exercised in sizing and laying out pipe so
unnecessary friction losses are avoided. As in suction
piping, the number of fi ttings should be minimized and
abrupt changes in direction and size of piping should be
avoided.
A gate valve should be installed in the discharge line. It will
be of assistance when priming the pump and will permit
service to be performed on the pump without having to
drain the discharge line and any connected vessels.
It is advisable to install a check valve in the discharge line
between the pump and the gate valve. In a system
operating at high discharge heads and with a foot valve on
the suction line, the check valve protects the pump from
pressure surges which occur when the pump is stopped.
In pressure systems without a foot valve, the check valve
prevents reverse rotation of the pump and loss of pressure
in the discharge line if the pump stops.
MOTORS AND CONTROLS
Small close-coupled centrifugal pumps use fractional (56C
frame) motors ranging from 1/3 HP through 3 HP at 3600
RPM. The larger close-coupled pumps use integral (JM
frame) motors ranging from 3 through 50 HP at 3600 RPM.
The single phase fractional (56C frame) motors are
protected by an internal, automatic reset, thermal overload
switch and no external protection is required. All Three-
Phase Motors (56C and JM frame) must be provided with
a manual starter that incorporates overload protection. For
overload protection, as well as automatic operation (in
conjunction with a fl oat or pressure switch), a magnetic
starter must be used.
Electric wiring to the motor should be sized in accordance
with applicable codes or handbooks. Undersize wires will
cause a voltage drop which may result in damage to the
motor. Be certain that the current characteristics of the
electrical supply are in agreement with those required by
the motor. Instructions for connecting the motor leads of a
dual-voltage motor appear in the cover of the motor
conduit box or on the motor nameplate.
PROTECTIVE CONTROLS
If there is any possibility that a pumping system will allow
the pump to run dry (loss of prime, empty tank, etc.) the
pump must be protected by an automatic control.
START UP
Centrifugal pumps must be primed (fi lled with liquid)
before they will start pumping. For pumping systems
which have a footvalve on the end of the suction line, the
easiest way to prime the pump is to fi ll suction line, pump
and enough of the discharge system to establish a liquid
level one or two feet above the top of the pump case. Any
air trapped in the pump case should be allowed to escape
by opening the top vent plug until a steady stream of liquid
fl ows from the opening. Turn the pump shaft by hand so
that any air trapped within the impeller is allowed to
escape. Wait several minutes for air to escape from any
nearly horizontal runs of suction pipe. Close the vent pipe
plug valve and prepare to start pump.
The correct direction of rotation is assured when the
pump is furnished complete with single-phase motor. It is
very important, however, to check for correct rotation
when three-phase motors are furnished, or when drivers
of any type are supplied by others. Check rotation of