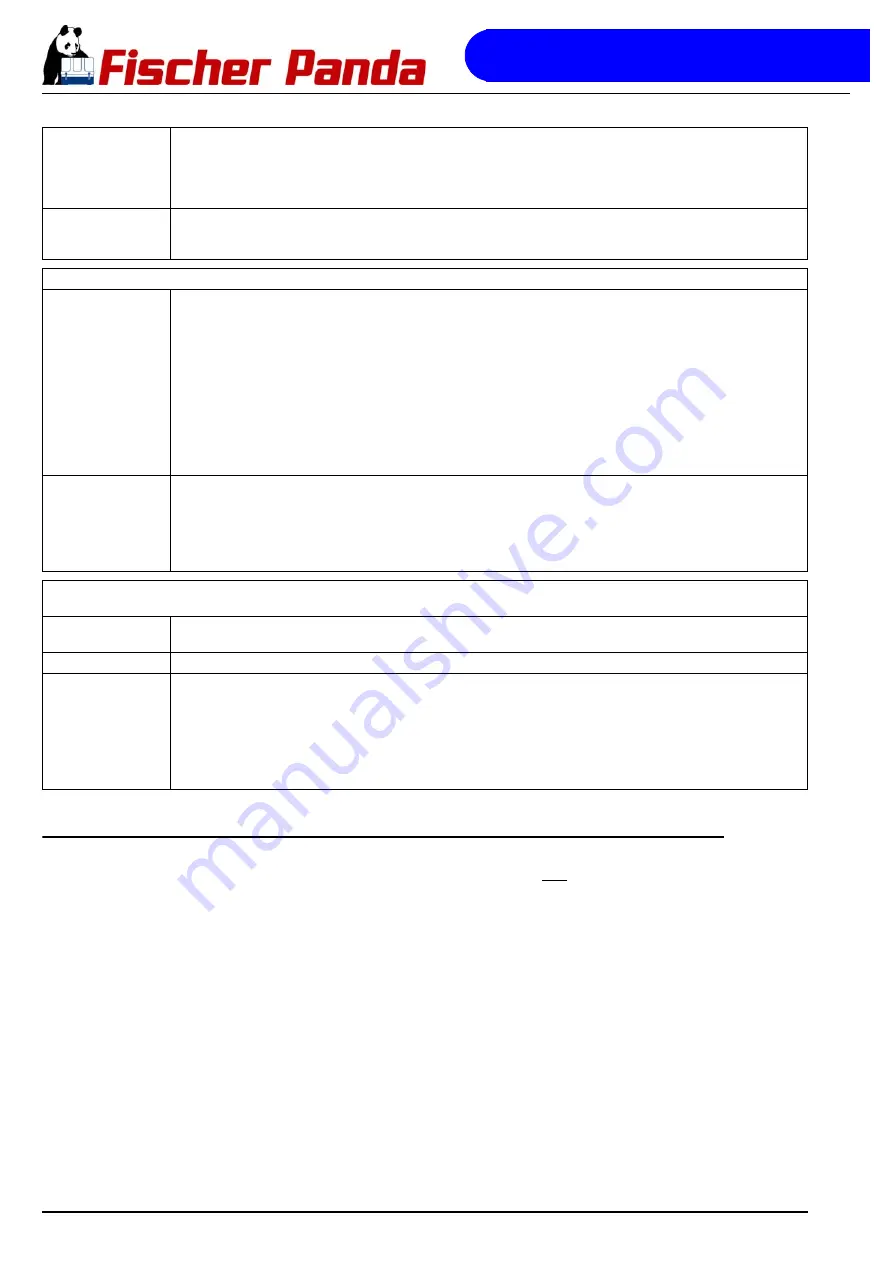
Installation Instructions
Seite/Page 86 Kapitel/Chapter 6: Installation Instructions
30.10.12
6.12.2 Master - Slave - Operation
Two or three fan controllers can be connected with each other that over one temperature sensor for the cooling
water, all fan controllers cam be operated synchronous.
On the connection between master and slave the PWM signal of the masters will transfer. The slave takes over of it
the PWM ratio and the frequency. The slave spends its PWM impulse only then if that of the masters is terminated.
Thus even load of the current supply is reached. The second slave (if available) regards the first slave as its master
(see also drawing).
The slave operation is activated automatically, by the presence of a PWM signal at the slave control inlet. As soon
as such a signal is present, the slave follows the control signal and ignores its own adjusts and its own temperature
measuring input. If the master does not spend a PWM signal, because the coolant temperature is under its starting
temperature, the slave drops back into the master operation and uses its own adjusts and analyses its own
temperature measuring input. So that the slave behaves correctly now, a 100k fixed resistor must be attached at its
temperature measuring input, which corresponds to a coolant temperature below the starting temperature.
The plug-able plug-in for the master-slave-connection and the 100k fixed resistor belong not to the normal scope of
supply and must be ordered separately.
Poti Window:
Adjusting the temperature window: With the potentiometer „Window“ the size of the window between starting temperature
and temperature for full number of revolutions (upper limit temperature) can be adjusted. The temperature window can
be adjusted from 5°C to 20°C. Is the starting temperature adjusted to 70°C and the temperature window to 10°C thus the
fan start-up with 70°C and reaches the maximum speed with 80°C (upper limit temperature). Ex factory a temperature
window of 12,5°C is adjusted (potentiometer position: In the middle).
Poti Freq:
Adjusting of the PWM frequency. Desired to many customers a potentiometer was added for changing the PWM
frequency. A selection of the frequency between approx. 1,7 and 3,5kHz is possible, which can serve for the avoidance
of unwanted oscillation/resonances. Ex factory a PWM frequency of 2 kHz is adjusted.
Function of the temperature sensors (NTC-resistance, extern und intern):
extern:
Over this temperature sensor the coolant temperature is collected. The starting temperature (fan start-up) and the upper
limit temperature can be adjusted by means of potentiometer present at the plate. The PWM ratio starts with the
exceeding of the starting temperature with approx. 40% (for 2 seconds), so that the fan starts reliably. According to
expiration of the 2 seconds the PWM ratio is determined by coolant temperature and potentiometer adjust. Since the
coolant temperature will not continue to rise in the 2 seconds, the PWM ratio will jump back to the minimum value of 30%.
At, from here, far rising coolant temperature, the PWM ratio will then rise linear with the temperature. If the upper limit
temperature is nearly reached, the PWM ratio rose to 85%. By 85% to 100% PWM ratio with reaching the upper limit
temperature switching over is made by one step, in order to avoid very short turn-off times. Likewise switch-back is made
with falling coolant temperature of 100% to 85% PWM ratio. If the coolant temperature falls under the starting
temperature, the minimum PWM ratio is not fallen below of 30%, but remains constant. If the coolant temperature sinks
approx. 3°C under the starting temperature, then the fan is switched off completely. All data exclusively apply on use of
the temperature sensor type S891-100k of the manufacturer Epcos.
intern:
Over this temperature sensor the temperature of the output stage is collected. If the temperature of the output stage rises
over 85°C, the PWM ratio, independently of the coolant temperature, is set to 100%, in order to avoid the switching losses
and cool the output stage down again. If the temperature of the output stage continues to rise nevertheless and beyond
90°C, the fan controller switches itself off.
NOTE: The cooling of the generator is not ensured anymore.
If the output
stage temperature sinks again under 85°C, the fan controller restarts itself. Such output stage temperatures cannot occur
however with intended use of the equipment.
Light emitting diodes: The 3 light emitting diodes (LED's) indicate the operating condition of the fan controller and have the following
meaning:
LED (green):
Shines with normal operation. After the self check and successful recognizing of the sensors the fan controller jumps into
the normal operating condition, in which the fan regulates, if the temperature lies in the appropriate range.
LED (yellow):
Shines if the fan controller is in slave-mode.
LED (red):
Shines with the occurrence of the following errors:
Incorrect external temperature sensor. If the temperature sensor for the cooling water is defective or the feeder line to it
interrupted (cable break), then the fan is accessed with 100% PWM.
Incorrect internal temperature sensor. If the temperature sensor for the output stage is defective or the feeder line to it
interrupted (cable break), then this is indicated over the LED. The fan controller continues working normally.
Overheating of the output stage. If the output stage of the fan controller becomes too hot, then this switches itself off.
Please read in addition the description of the function of the internal temperature sensor.
Содержание 5000i PVK-U
Страница 36: ...Seite Page 36 Panda_5000i_PVMV N_Book_eng R02 30 10 12 Leere Seite Intentionally blank Basics...
Страница 48: ...The Panda Generator Seite Page 48 Kaptitel Chapter 4 The Panda Generator 30 10 12...
Страница 126: ...Generator Tables Seite Page 126 Kaptitel Chapter 8 Generator Tables 30 10 12...
Страница 146: ...Installation Page 146 Chapter 11 Installation 30 10 12 11 3 Dimensions Fig 11 3 0 1 Housing of the Panda iControl2 panel...
Страница 150: ...Page 150 Chapter 11 Installation 30 10 12 Intentionally left blank Installation...
Страница 152: ...Page 152 Chapter 12 Maintenance 30 10 12 Intentionally left blank Maintenance...
Страница 158: ...Page 158 Chapter 14 Annex 30 10 12 Intentionally left blank Annex...