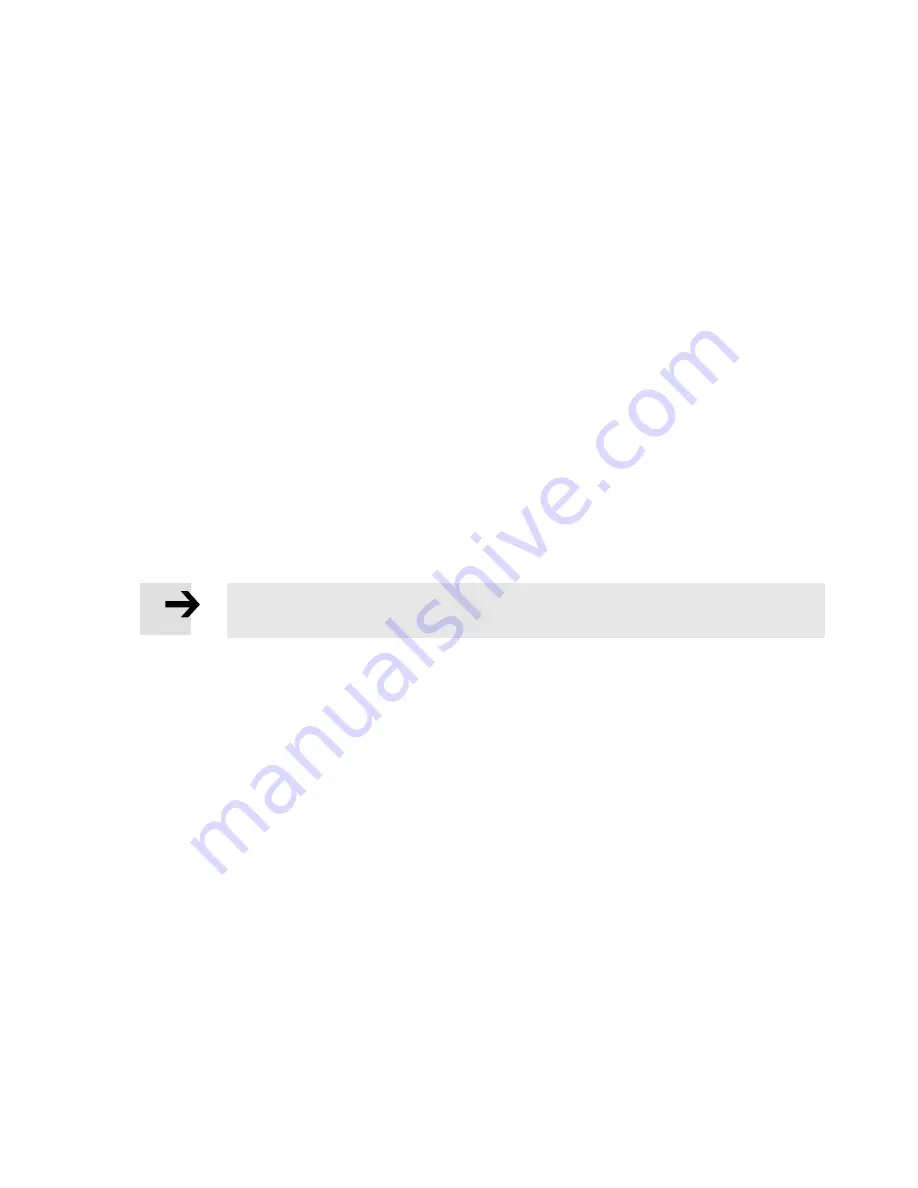
6
Functions
Festo – GDCP-CMMP-M3-FW-EN – 1203NH
57
The encoder difference of 60° represents a start value that is operational in most cases. But it must be
adjusted, depending on the application.
6.6.8
2nd measuring system at input [X2A]
The input [X2A] can only be used for motors with encoder. After switch-on (24 V voltage off or reset),
homing must be executed first.
The interface [X2A] supports all commonly available incremental resolvers, single-pole or multipolar.
6.6.9
Commissioning
After parameterisation, the system is commissioned.
Before the first enable, the counting direction of the motor and of the external encoder must be
checked.
To do this, shift the moving mass by hand and observe the change in the FCT (online area – operate).
The actual position is recorded by the external encoder, and the speed is calculated from the encoder in
the motor. Both values change as a result of shifting by hand. The direction of the system can be selec-
ted freely and is usually simply selected corresponding to the application. After selection of a suitable
zero point, shift the axis by hand in a positive direction. If the actual position becomes smaller rather
than larger, the direction of the 2nd measuring system must be changed. If the speed is negative, the
direction of rotation of the motor must be reversed.
After each change, download, save and restart must be done.
For motors with integrated brake, the brake can be manually opened with the button Release brake.
Note
For vertical axes, the moving masses must be secured against falling.
After that, the customary commissioning is continued.
Usually, the controller data must be adjusted manually to achieve a good positioning. For longer
toothed belt axes, reinforcement of the position controller must not be too large, since the system
would otherwise swing up.
Содержание CMMP-AS-***-M3 Series
Страница 131: ......