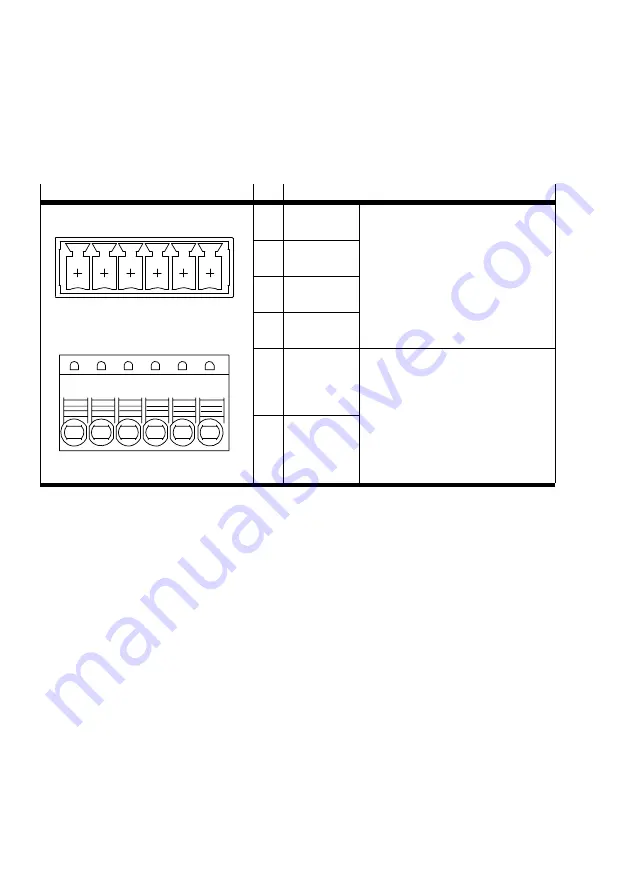
4
Installation
76
Festo – GDCP-CMMO-ST-EA-SY-EN – 2017-05c – English
4.3.5
[X6] Motor
The ready-to-use cables from Festo (
è
www.festo.com/catalogue) offer sufficiently large cable cross
sections as well as screening of the motor/encoder cable with earth contact on both sides for connec
ted components.
Connection
Pin
Function
X6
1
6
1
6
1
String A
Connection of the two motor strings
2
String A/
3
String B
4
String B/
5
BR+
Connection of the holding brake
– +24 V
– Max. 1.4 A
– 33 W
– Short-circuit-proof and
overload-proof
BR– = GND,
BR+ is switched (24 V load)
6
BR–
Tab. 4.8
Motor connection [X6]
Содержание CMMO-ST-C5-1-DION
Страница 172: ...B Control via Ethernet CVE 172 Festo GDCP CMMO ST EA SY EN 2017 05c English ...
Страница 173: ......