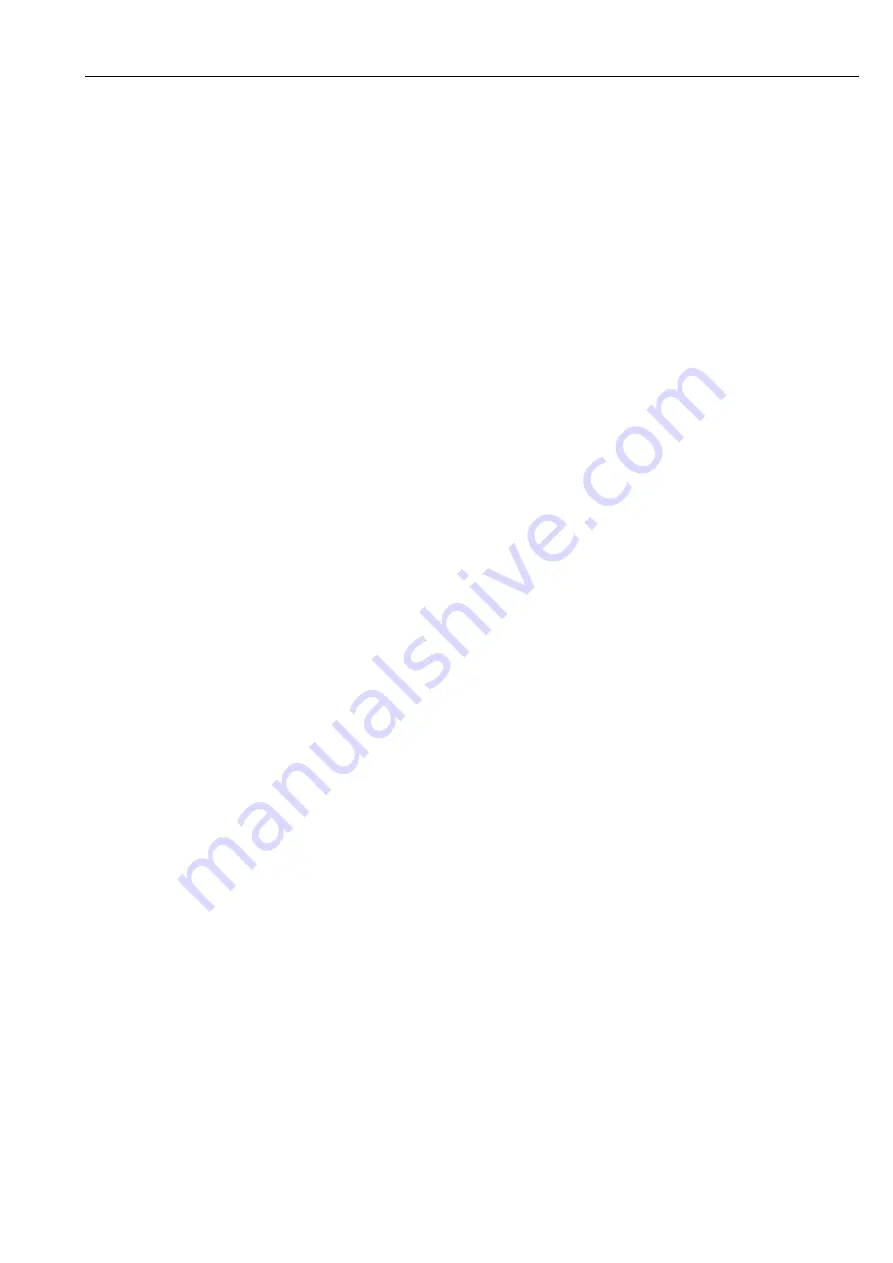
Proline t-mass 65 PROFIBUS DP/PA
Maintenance
Hauser
89
8.4
Replacing seals
Under normal circumstances, fluid wetted seals of the sensor do not require replacement.
Replacement is necessary only in special circumstances, for example if aggressive or corro-
sive fluids are incompatible with the seal material.
Only Hauser seals may be used.
Sensor-specific information:
• t-mass F:
The sensor contains o-rings seals and a bushing. In case of failure, the device must be
returned to an Hauser sales center for inspection and repair (
• t-mass I:
The transducer is welded to the insertion tube and has no exchangeable seals. The com-
pression fitting contains wetted seals (ferrules) and a bonded seal is used on the G 1 A
thread version.
"
Caution!
Do not reuse gaskets after removing sensors.
Use only original parts from Hauser. The compression fitting and gasket seals are
deliverable as spare parts. The seal ring can be replaced easily on site
8.5
In-situ calibration
The t-mass flowmeters are designed to support in-situ calibration using a reference meter
signal, thus saving time and cost by reducing the need for factory re-calibration.
Pre-requirements for in-situ calibration with adjustment:
1.
Stable gas composition (operation with one gas group only; without gas analyzer input)
2.
Stable pressure and temperature (without pressure compensation input)
3.
Mass flow reference
a. mass flow reference meter, mounted in the measurement or bypass pipe, providing
a mA signal to t-mass or
b. manual entry of known mass flow reference values. For example, the display value
from the reference meter or a derived value from a pump curve)
4.
Ability to control the flow range over a minimum of 5 control points
This function is activated using the service access code.
For specific applications, contact your Hauser sales center.
8.6
Recalibration
For thermal meters, the interval between calibrations is dependent on the application since
calibration drift is predominantly caused by contamination of the sensor surface.
If the gas is not clean (i.e. contains particulates), then gentle cleaning of the sensor elements
can be effective at regular intervals. The cleaning interval will depend upon the nature and
extent of the contamination.
Determination of recalibration intervals:
• If the measurement is critical, then a calibration audit should be undertaken by performing
recalibration checks once per year for a period of 2 years. Increase that period to twice per
year if the application gas is not clean and dry.
Depending on the results of the audit, the next recalibration check interval can be
increased or decreased accordingly.
• For non-critical applications and or where the gas is clean and dry, a recalibration interval
of every 2 to 3 years is recommended.
Содержание Proline t-mass 65 PROFIBUS DA
Страница 127: ...www addresses endress com ...