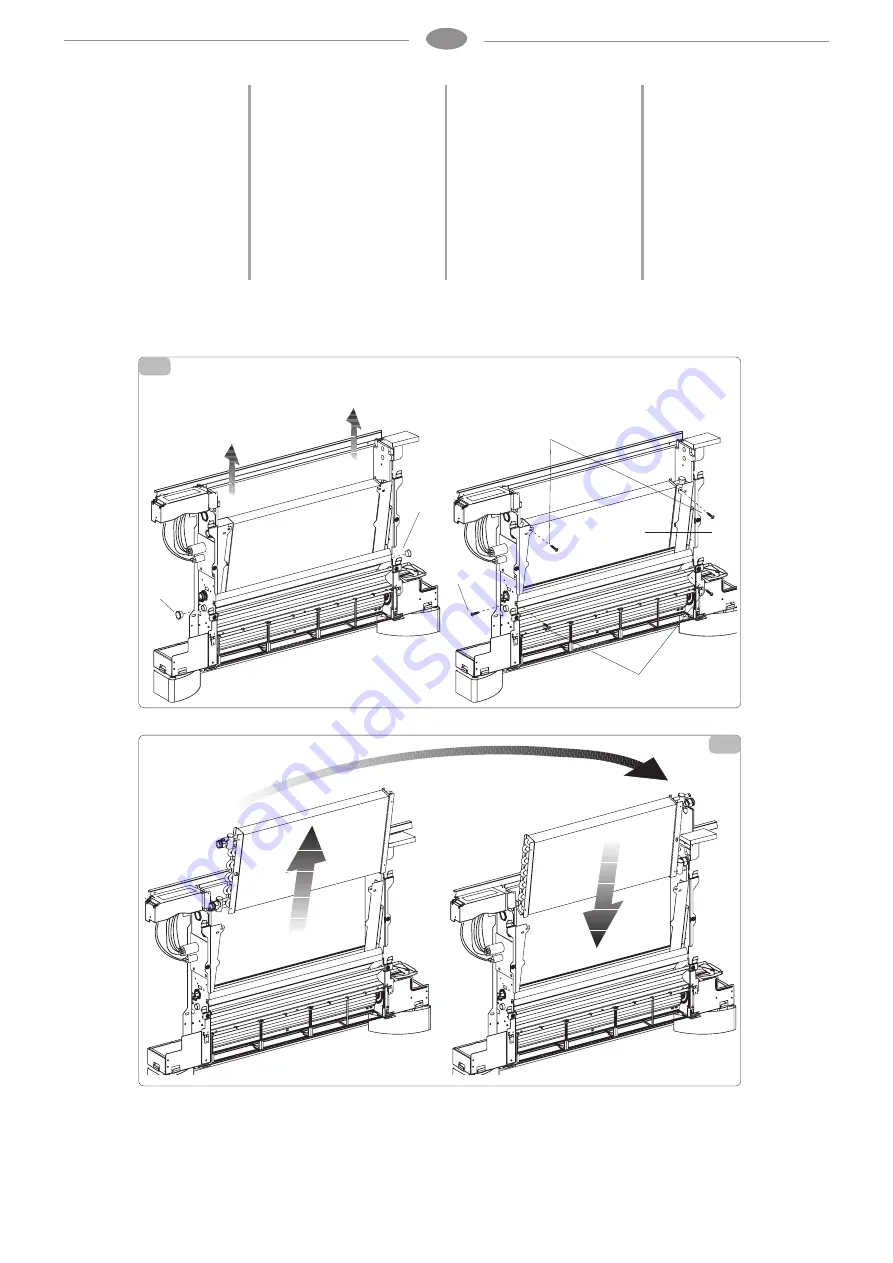
GB
16
Disassembling the heat
exchangers
- Unscrew the four screws that
secure the heat exchanger (fig.
21 ref. C);
- remove the coil water probe, if
present.
- remove the heat exchanger (fig.
21 ref. F);
- remove the drip guard extension
from the central pan (fig. 21 ref.
D);
- on the opposite side, remove
the plug on the condensate
evacuation hole (fig. 21 ref. E);
22
21
C
E
D
C
F
G
- unscrew the fixing screw
of the central condensate drain
pan (fig. 21 ref. G), set the pan
on the opposite side so that the
connection nozzle for the drip
guard extension comes out of
the structure, therefore block
the pan with the previously
removed screw;
- reinsert the drip guard extension
and the cap on the opposite
side;
- open the pre-cut hexagonal holes
on the right side insulation and
close the hexagonal holes on
the left edge with insulating
material;
- rotate the exchanger, bringing
the connections to the opposite
side, and reinsert it on the
machine (fig. 22);
- tighten all the heat exchanger
fixing screws.
Once all the described steps have
been completed, reassemble
all the previously disassembled
components, following the
disassembly steps in inverse
order.
Содержание ETI 2100
Страница 1: ...INSTALLATION AND USE MANUAL GB SILENCE THIN ETM ETI Fan Coil with Smart Touch controls ...
Страница 20: ...20 20 GB 31 A B A B 32 B C C B 33 A B 33 ...
Страница 34: ...58 GB 240 260 280 2100 ...
Страница 35: ...59 GB 240 260 280 2100 ...