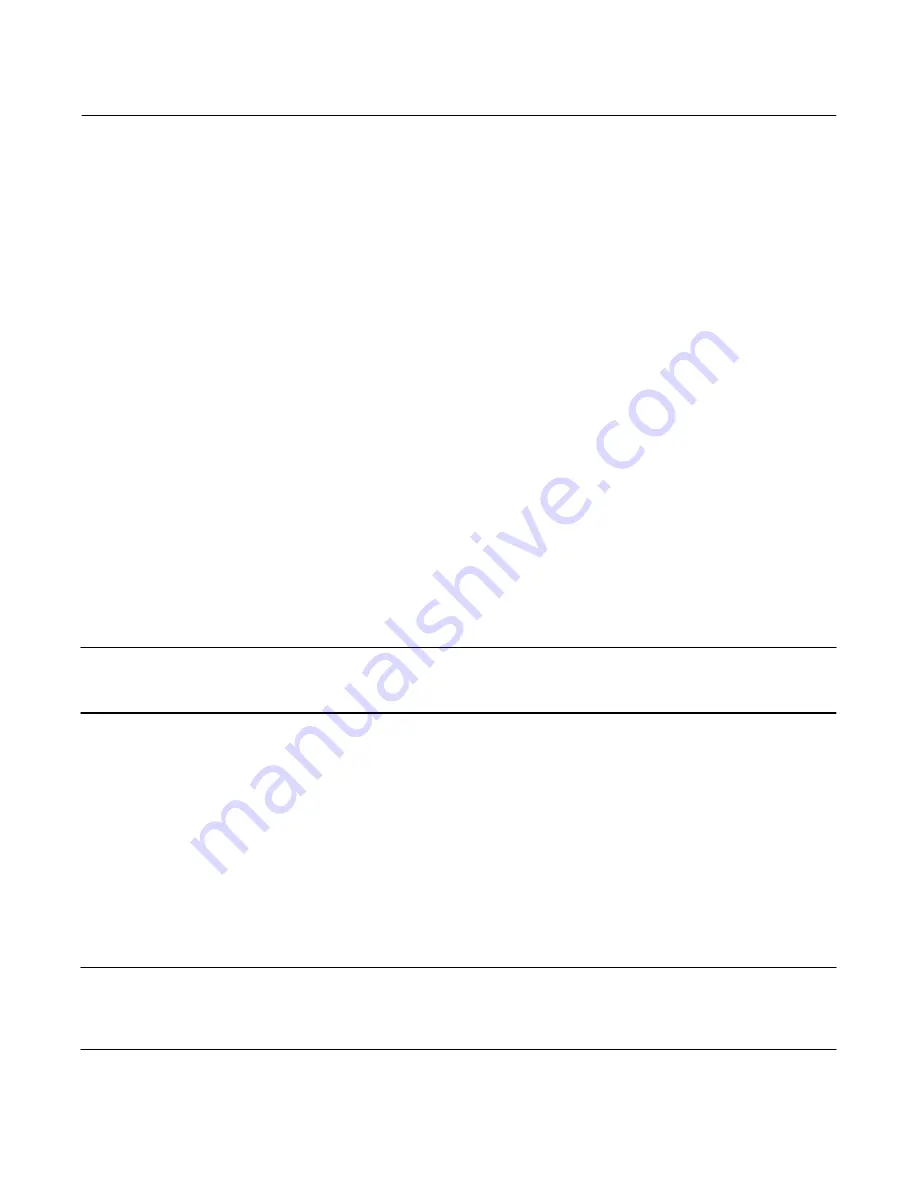
Instruction Manual
D200156X012
4194HA, HB, HC Controllers
July 2018
19
1. Remove two screws (key 6) and lift off the proportional band indicator cover (key 36).
2. Set the proportional band between DIRECT and REVERSE.
3. Adjust the set point pressure to the low limit of the set point input range. Note the position of the set point
indicator. Loosen the set point zero adjustment locking screw and adjust the zero adjustment screw (figure 3‐1)
until the set point indicator aligns with the lowest scale limit.
When the set point indicator is properly aligned with the low scale limit, tighten the zero adjustment locking screw.
4. Adjust the set point pressure to the upper limit of the input span. Note whether the indication is above or below the
upper limit of the process scale.
5. Adjust the span screw as follows: Clockwise to increase span for a low indication; counterclockwise to decrease span
for a high indication. Adjust the span screw to correct one‐half the error.
6. Repeat steps 3 through 5 until the error is eliminated.
7. Adjust the remote set point pressure to 50 percent of the remote set point range.
8. Make sure the remote set point indicator is within
±
1 percent of the mid‐scale mark and, if so, proceed to step 10. If
the set point indicator is not within
±
1 percent but is within
±
2 percent of the mid‐scale mark then proceed with
step 9. If the set point indicator is
not
within
±
2 percent, proceed to the remote set point calibration in Section 5.
9. Loosen the zero adjustment locking screw and adjust the zero screw to correct for one‐half the error. Tighten the
locking screw.
10. Adjust the remote set point pressure to the lower and upper range limits and make sure the set point indicator is
within
±
1 percent.
11. Install the proportional band indicator cover and tighten the two screws.
12. If necessary, proceed to the process indicator zero‐and‐span calibration procedure in this section. Otherwise,
proceed to the flapper alignment procedure in this section.
Flapper Alignment
Note
Perform the process indicator zero‐and‐span calibration procedure and, if necessary, the remote set point calibration procedure
before the flapper alignment.
Flapper leveling screw numbers and adjustments are shown in figure 3‐1.
Provide a means of applying supply pressure to the controller. Also, provide an accurate means of measuring output
pressure.
Apply process differential pressure to the differential pressure unit. Refer to figures 2‐1 and 2‐2 for the differential
pressure unit connections.
1. For a controller with manual set point, move the set point indicator to 50 percent of the scale range. For a controller
with remote set point (suffix letter M), adjust the remote set point pressure until the set point indicator is at 50
percent of the scale range.
2. Apply differential pressure equal to 50 percent of the input range.
Note
If a pressure source is not available to pressure the input element (differential pressure unit) to 50 percent of range, an alternate
method is to disconnect link 1 at the drive arm and tape the process indicator at 50 percent of the input range. Note the hole from
which link 1 was removed for proper replacement.