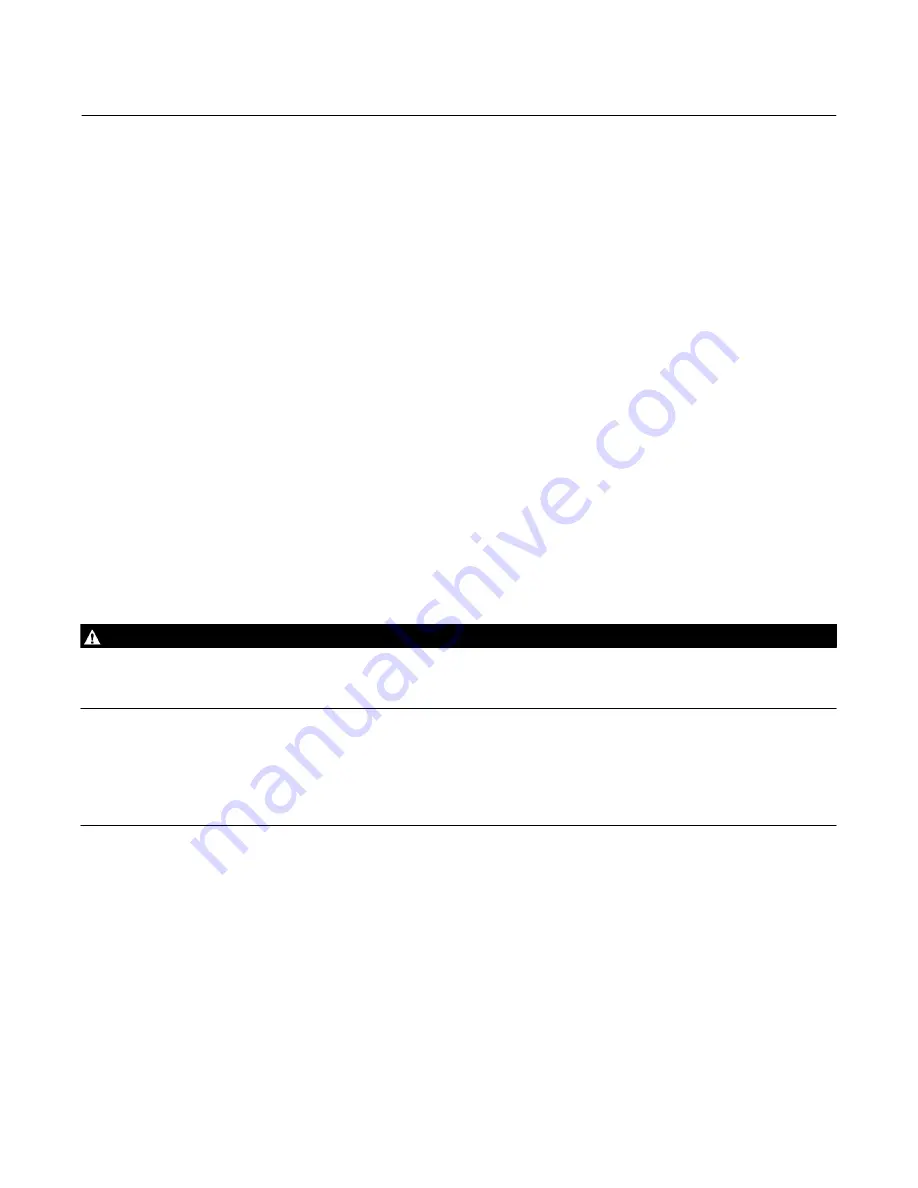
Instruction Manual
D200156X012
4194HA, HB, HC Controllers
July 2018
72
Link B
the set point indicator assembly.
2. Loosen the screw in the replacement link and adjust the length to match the link being replaced. Tighten the screw.
4. After replacing parts, refer to the various maintenance calibration procedures (process zero‐and‐span adjustment,
flapper alignment).
Pressure Control Block for Remote Set Point
1. Remove remote set point pressure.
2. Loosen the nut on that portion of the tubing connecting the capsular element to the pressure control block
(key 57).
3. Remove the two cap screws (key 58) holding the pressure control block to the frame (key 3) and lift out the
pressure control block.
4. Install the O‐ring (key 7) on the replacement pressure control block.
5. Install the replacement pressure control block to the frame with two screws (key 58).
6. Tighten the nut loosened in step 2.
7. Apply the maximum value of remote set point pressure and check for leaks.
Remote Set Point Maintenance Calibration
WARNING
To avoid personal injury or property damage resulting from the sudden release of pressure, do not exceed the operating
limits given in this manual.
Note
Perform all maintenance calibration procedures upon completion of maintenance. If only zero‐and‐span or linearity adjustments
are required, use only those procedures. Key numbers are referenced in figures 6‐1 and 6‐2. Adjustments are shown in figure 3‐1.
After maintenance calibration, perform the flapper alignment procedures if directed to do so. Otherwise, go to the appropriate
prestartup instructions in the Controller Operation section.
Remote Set Point Precalibration Procedures
1. Set the proportional band adjustment between DIRECT and REVERSE.
2. Remove the tie bar (key 106).
3. Apply 50 percent of full span remote set point pressure.
4. The drive flexure (key 79) should be straight. If not, proceed as follows:
a. Loosen the screw on the adjustment arm on pivot assembly A (key 114) and the screws holding the drive flexure.
b. Set the length of the adjustment arm so the drive flexure is parallel to the centerline of the capsules.
c. Tighten the screw on the adjustment arm.