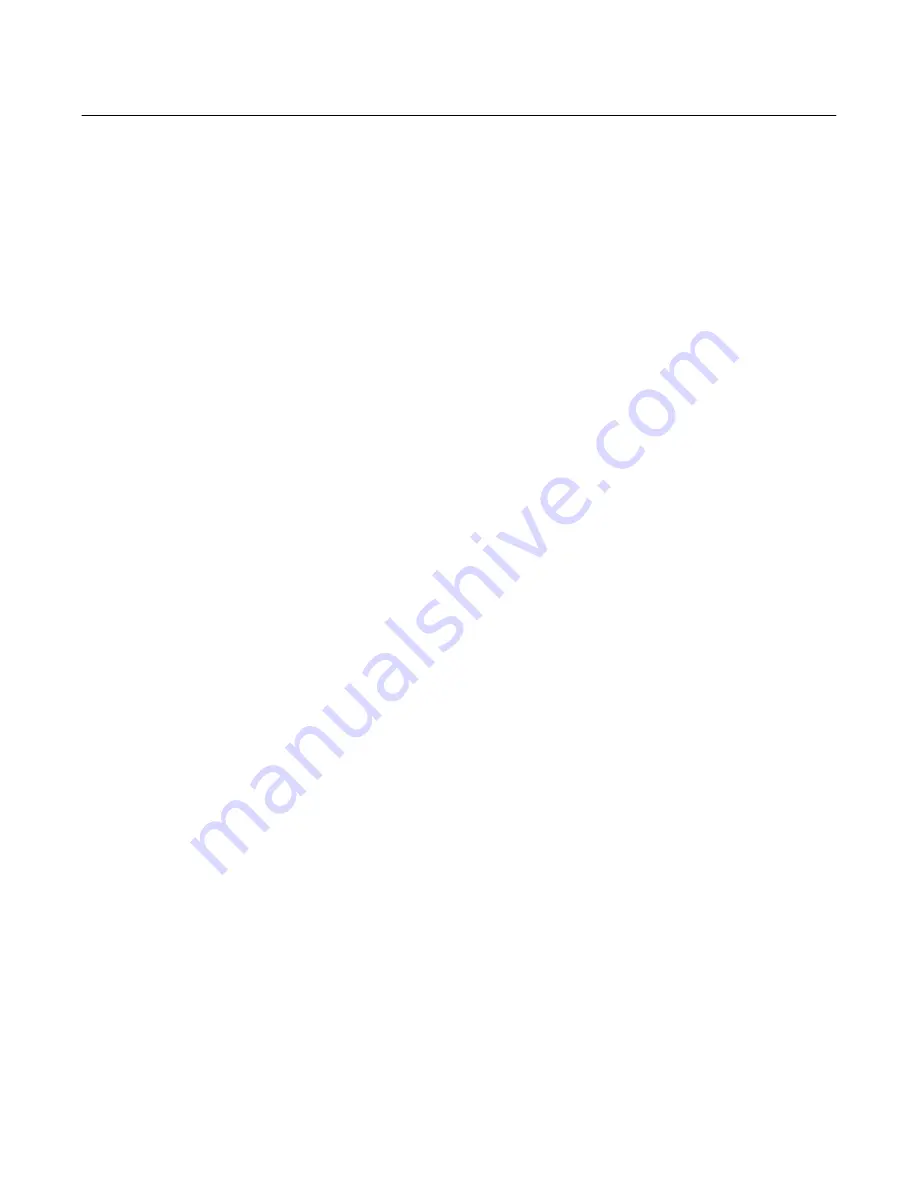
Instruction Manual
D200156X012
4194HA, HB, HC Controllers
July 2018
21
The process differential pressure input element is connected to the process indicator and to the flapper by connecting
links. As the process differential pressure increases (in a direct‐acting controller), the flapper moves toward the nozzle,
restricting flow through the nozzle and increasing nozzle pressure. When this occurs, relay action increases the output
pressure (delivery) of the controller. Output pressure is fed back to the proportional bellows. The action of the
proportional bellows counteracts the flapper movement that resulted from the process differential pressure change
and backs the flapper away from the nozzle until equilibrium is reached.
The set point adjustment changes the distance between the nozzle and flapper as does a change in process differential
pressure except that when the set point is changed, the nozzle moves with respect to the flapper.
The proportional band adjustment knob positions the nozzle on the flapper. Increasing (widening) the proportional
band moves the nozzle to a position on the flapper where less input and more feedback motion occurs, which
decreases the gain of the controller. Decreasing (narrowing) the proportional band moves the nozzle toward a
position where more input and less feedback motion occurs, which increases the gain. The controller action is
changed from DIRECT to REVERSE by turning the proportional band adjustment knob to position the nozzle on the
flapper quadrant to a point where the direction of the flapper motion versus input motion is reversed (see flapper
detail in figure 5‐11). With the controller in the reverse‐acting mode, an increase in process differential pressure
causes a decrease in output pressure.
Remote Set Point Option (suffix letter M)
The capability to adjust the controller set point from a remote location is available with all 4194H controllers. This
option is designated by the suffix letter M in the type number.
A control pressure is applied to the capsular element within the remote set point assembly. The expansion and
contraction of the capsule moves the set point adjustment via a connecting linkage. Increasing the control pressure to
the capsule increases the set point setting and decreasing the control pressure reduces the set point setting.
Auto/Manual Station Option (suffix letter E)
Controllers with the auto/manual option (designated by the suffix letter E in the type number) have piping on the
output side of the relay as shown in figure 4‐5. Supply pressure to the relay is also applied to the manual loader. The
manual loader, functioning as a regulator, applies pressure to one side of the plastic tube and to the auto/manual
switch. Output pressure from the relay registers on the other side of the plastic tube as well as in the auto/manual
switch.
When the auto/manual switch is in the MANUAL position, the output of the manual loader is channeled through the
auto/manual switch and becomes the output of the controller. When the auto/manual switch is in the AUTO position,
the output of the relay is channeled through the switch to become the output of the controller.
Before the auto/manual switch is operated, the output of the relay must equal the output of the manual loader to
avoid bumping the process. Adjusting the set point varies the pressure on the left‐hand side of the plastic tube.
Adjusting the manual loader knob varies the pressure on the right‐hand side. When the pressures are equal, the metal
ball is centered in the tube. Pressure imbalance forces the ball to one end of the tube where it forms a seal, blocking air
flow through the tube.