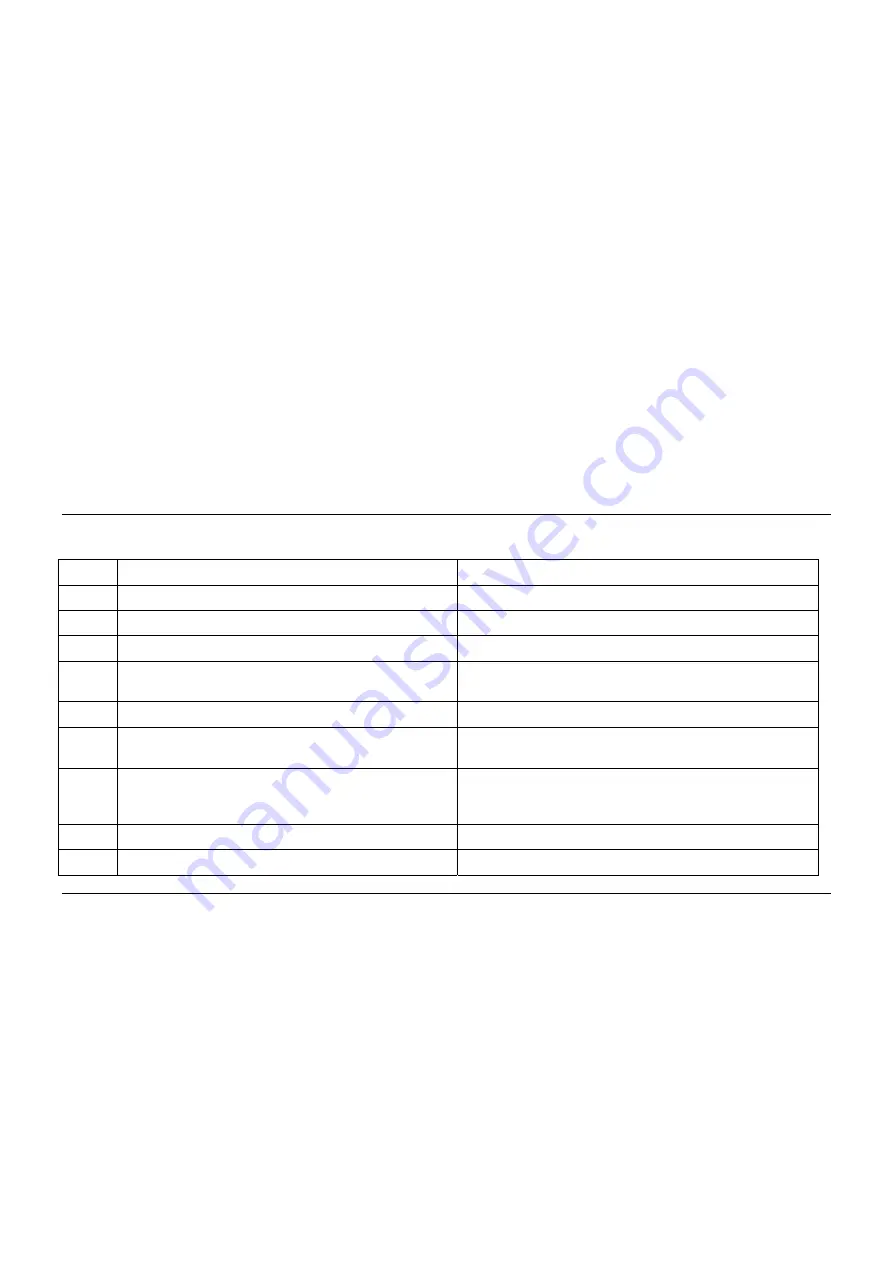
8
produced by this procedure tends to stick to the gas
nozzleholder and nozzle, clean them frequently to avoid
problems (dual arc) that can destroy the nozzle in the
space of a few seconds.
Considering the high level of radiation (infrared and ultra-
violet) emitted during this procedure, we recommend that
the operator and anyone else in the vicinity of the work-
place follow adequate, careful protective measures.
Shut off the machine when you have finished working.
4 CUTTING ERRORS
4.1 INSUFFICIENT PENETRATION
This problem may be caused by:
•
High speed:
Always make sure that the arc fully penetrates the
work-piece, and is never angled forward by more than
10° - 15°. This will avoid incorrect consumption of the
nozzle and burns on the gas nozzle holder.
•
Workpiece too thick (see cutting speed/thickness
diagram).
•
Mass clip not in good electrical contact with the
workpiece.
•
Worn nozzle and electrode.
•
Nozzle hole too large for the current value set on the
knob
Z
.
•
Cutting current too low.
NOTE: When the arc does not penetrate, scraps of molten
metal may damage the nozzle hole.
4.2 THE CUTTING ARC GOES OUT
This problem may be caused by:
•
Worn nozzle, electrode or diffuser.
•
Air pressure too high.
•
Supply voltage too low.
•
Advancement speed too low.
•
Cutting current too high for the thickness of the
workpiece.
4.3 SLANTED CUT
If the cut is slanted, shut off the machine and replace the
nozzle.
Prevent the nozzle from coming into electrical contact
with the workpiece (including via scraps of molten
metal).
This will cause rapid at times instantaneous destruction of
the nozzle hole, leading to very poor quality cutting.
4.4 EXCESSIVE WEAR ON CONSUMER PARTS
This problem may be caused by:
•
gas pressure too low compared to the recommended
value.
•
gas supply circuit damaged.
5 ERROR CODES
In the event of a malfunction, the letter
E
may appear on the display
H
, followed by a number with the following meaning:
CODE ERROR
SOLUTION
1 Hardware
lockup
Contact the technical service department.
2 Hardware
lockup.
Contact the technical service department.
12
Transfer reed sensor closed during start-up.
Replace the reed.
13
Hazardous voltage on the torch
Shut the machine off and turn it back on. If the error
recurs, contact the technical service department
51
Torch not recognized.
Check the type of torch. Use only original torches
52
Start button pressed during start-up
Open, the start command, shut the machine off and turn it
back on
53
Start button pressed while resetting the pressure
switch, which shows insufficient pressure, or thermal
reset
Open start command, shut the machine off and turn it back
on
54
Short-circuit between electrode and nozzle
Shut off the machine, check the electrode and the nozzle
55
Electrode finished
Shut off the machine, replace the electrode and the nozzle
6 HELPFUL HINTS
• If the system air contains a considerable amount of
moisture and oil, it is best to use a drying filter to avoid
excessive oxidation and wear of the consumer parts,
damaging the torch and reducing the cutting speed and
quality.
• The impurities in the air may make it difficult to light the
pilot arc. If this occurs, clean the end portion of the
electrode and the interior of the nozzle using very fine-
grained sandpaper.
7 ACCESSORIES
7.1 COOLING UNIT
When using the torch P150W or P150W HF, which requires
water cooling, you must apply the cooling unit.
7.2 INTERFACE CODE 540050
This circuit allows the following functions on the 14-pin
connector
AE
:
A - Start.
B - Arc transferred signal.
C - Signal in proportion to the cutting voltage.
D - Cutting current adjustment.
Содержание PLASMA 167
Страница 2: ...2 2 1 3 4 5 6...