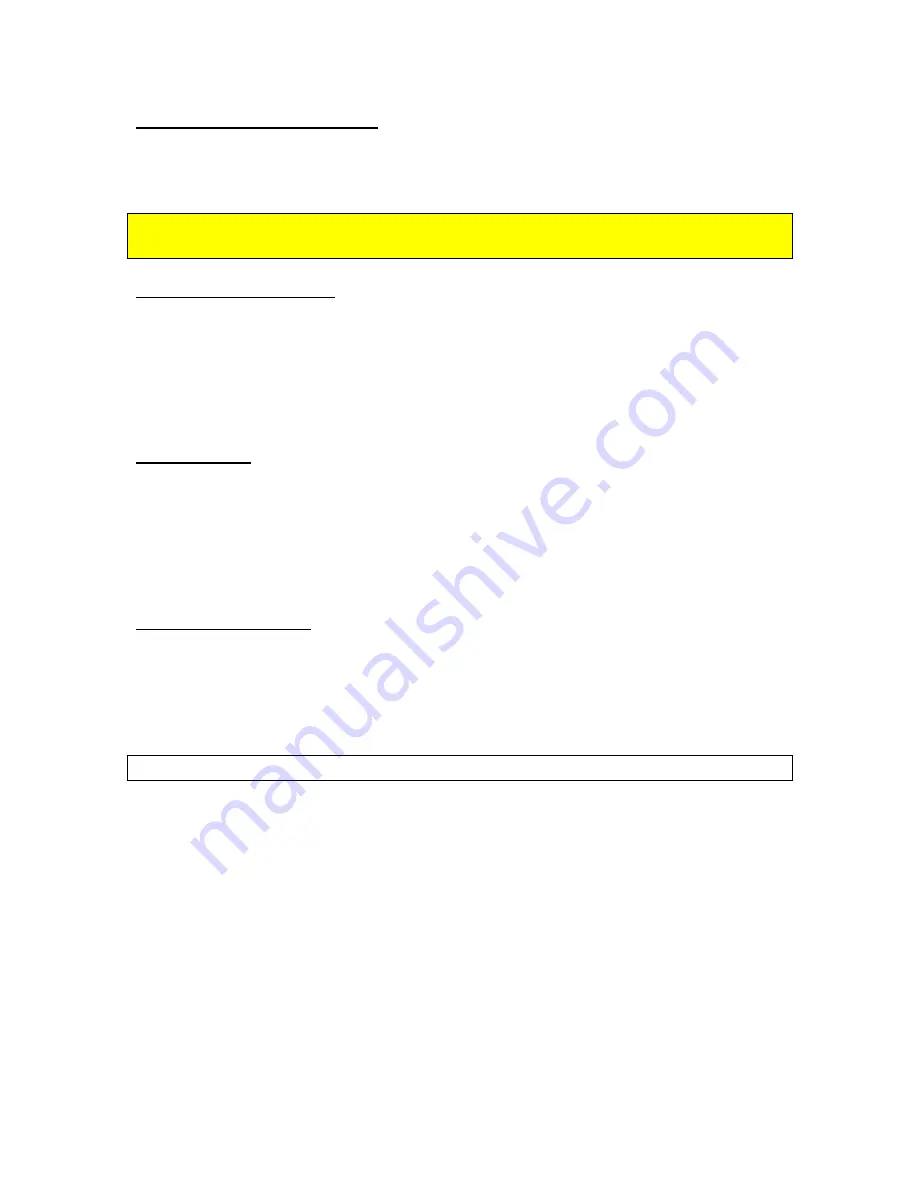
4-4
4.1 Air/Electronic Maintenance
Maintenance of the A/E transducer may be required if there is extreme difficulty in setup
or erratic readings on the Accusetter II.
Power to the column must be turned off prior to installing or removing a signal
conditioning module.
Mag & Zero Needle Valves
If oil is present, it is helpful to clean out each needle valve. With the gage set on a master,
unscrew the mag knob and remove. Allow the air to blow freely. Inspect the “O” ring on
the needle valve body: replace if necessary. Reinsert the mag needle valve and screw
down until the point on the Accusetter II scale comes back to the master point. Repeat
the procedure on the zero knob. By only cleaning one needle at a time, the gage setting is
not lost. Re-check the mastering points before gaging.
Bias Restriction
Remove restrictor bleed screw with a 1/4" allen wrench and the metallic filter, see figure
4.3. Insert #1/4-28 screw into bias restrictor and pull out restrictor assembly. Remove
bottom metallic filter. Wash out in cleaning spirits. The bias restrictor holes may be
cleaned out (very carefully) with a toothpick if necessary. Inspect and replace the two o-
rings if required. Blow dry from central hole in restrictor assembly, and reinsert
components in reverse order.
Needle Valve Assembly
When an extremely dirty air condition is encountered, it may be necessary to remove the
needle valve assembly and clean it. Unscrew the set screw holding the valve assembly.
Pull out the complete valve assembly. Unscrew the needle body, clean and inspect the
“O” ring. Check the “O” ring on the outer valve body and also at the bottom of the bore
in the aluminum restriction block. If they have deteriorated, replace.
Note: See section 2.2, Spare Parts.
Re-assemble the needle to the body. If the threads appear to be loose, carefully spring the
split threads open. This is best done using the wedge effect of the screwdriver tip. Pick
one so that the spread is only slightly larger than the existing slot and do not over bend.
With the valve assembled and all “O” rings in position, reinsert the valve, taking care to
go slowly so as not to nick the top “O ring, as it passes the set screw hole. If pressure is
felt to build up and suddenly release during insertion, the “O” ring may possibly be cut.
Pull out, inspect and replace if necessary. Push assembly down hard to seat the bottom
“O ring, tighten the set screw to retain.
Содержание Accu-Setter II
Страница 2: ...A Accu Setter II User s Manual Edmunds GAGES...
Страница 16: ...2 3 2 3 Overall E9300Unit Figure 2 1 Accusetter II Basic Unit E9300...
Страница 18: ...2 5 Figure 2 2 Front Panel...
Страница 20: ...2 7 Figure 2 3 Rear Panel...
Страница 31: ...3 3 Front Mounting Foot Rear Mounting Bracket Figure 3 1 Base Feet Figure 3 2 Filter Regulator Mounting...
Страница 32: ...3 4 Figure 3 3 Air Connections For Air Gaging Application Only...
Страница 39: ...3 11 An example of various multipliers as related to diameter measurement follows...
Страница 40: ...3 12 The last consideration to complete the formula is the gaging function See examples below...
Страница 43: ...PROGRAMMING SINGLE CHECK MEASUREMENT 3 15...
Страница 44: ...PROGRAMMING SINGLE CHECK MEASUREMENT 3 16...
Страница 50: ...PROGRAMMING MULTIPLE CHECK MEASUREMENT 3 22...
Страница 51: ...PROGRAMMING MULTIPLE CHECK MEASUREMENT 3 23...
Страница 59: ...PROGRAMMING MULTIPLE FIXTURE MEASUREMENT 3 31...
Страница 60: ...PROGRAMMING MULTIPLE FIXTURE MEASUREMENT 3 32...
Страница 90: ...4 5 Figure 4 3 A E Block...
Страница 93: ...4 8 Figure 4 5 Input Output Jumpers...