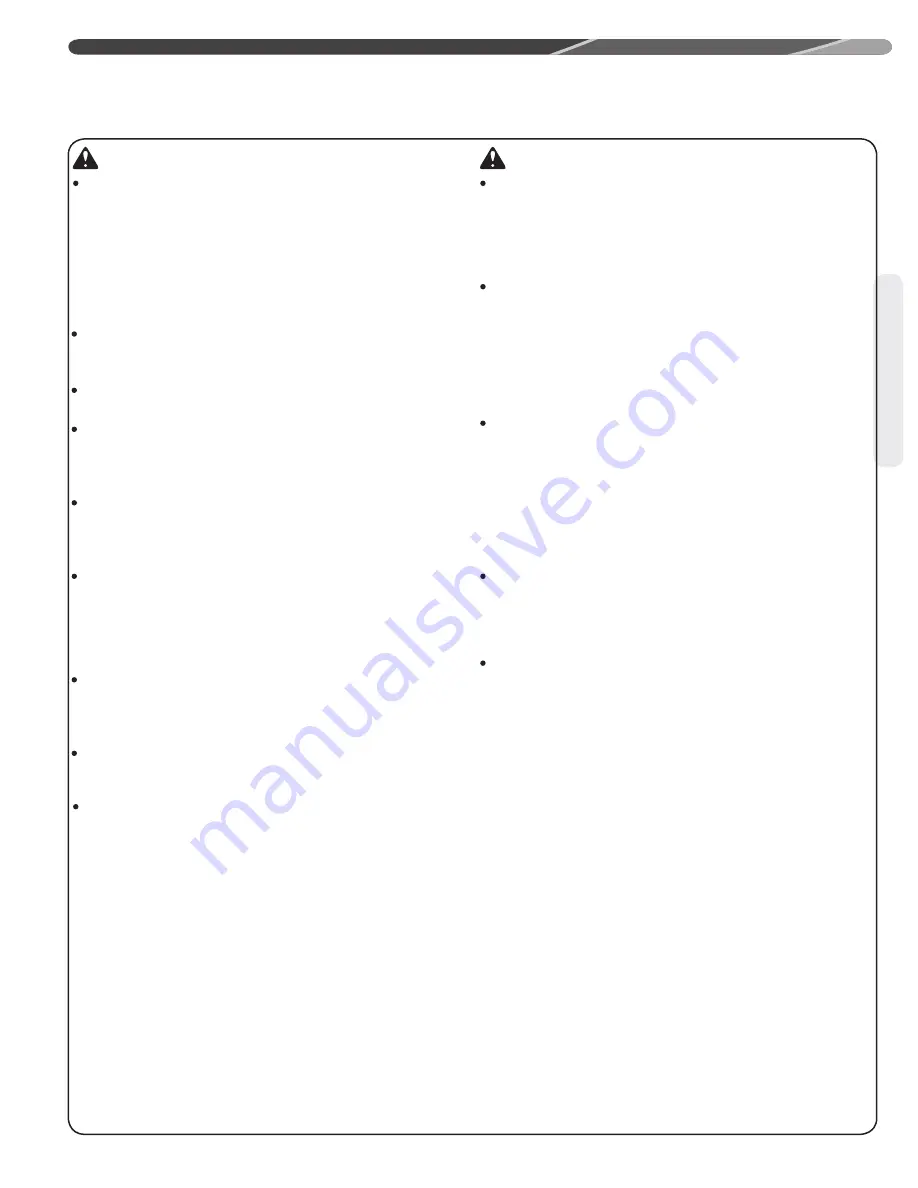
3
Safety
1.0 IMPORTANT SAFETY INFORMATION
WARNINGS:
These instructions are intended as an aid to
qualified, licensed service personnel for proper
installation, adjustment, and operation of this
unit. Read these instructions thoroughly before
attempting installation or operation.
Failure to
follow these instructions may result in improper
installation, adjustment, service, or maintenance
possibly resulting in fire, electrical shock,
property damage, personal injury, or death.
The unit must be permanently grounded. Failure
to do so can cause electrical shock resulting in
severe personal injury or death.
Turn off electric power at the fuse box or service
panel before making any electrical connections.
Complete the ground connection before making
line voltage connections. Failure to do so can
result in electrical shock, severe personal injury,
or death.
Disconnect all power to unit before starting
maintenance. Failure to do so can cause
electrical shock resulting in severe personal
injury or death.
Never assume the unit is properly wired and/or
grounded. Always test the unit cabinet with a
noncontact voltage detector available at most
electrical supply houses or home centers before
removing access panels or coming into contact
with the unit cabinet.
DO NOT use oxygen to purge lines or pressurize
system for leak test. Oxygen reacts violently with
oil, which can cause an explosion resulting in
severe personal injury or death.
The top of the scroll compressor shell is hot.
Touching the compressor top may result in serious
personal injury
.
The manufacturer’s warranty does not cover
any damage or defect to the unit caused by the
attachment or use of any components, accessories,
or devices (other than those authorized by the
manufacturer) into, onto, or in conjunction with
the heat pump.
You should be aware that the
use of unauthorized components, accessories,
or devices may adversely affect the operation
of the heat pump and may also endanger life
and property.
The manufacturer disclaims any
responsibility for such loss or injury resulting
from the use of such unauthorized components,
accessories, or devices.
CAUTIONS:
R-410A systems operate at approximately 60%
higher pressures (1.6 times) than R-22 systems. Do
not use R-22 service equipment or components on
R-410A equipment. Use appropriate care when using
this refrigerant. Failure to exercise care may result in
equipment damage or personal injury.
Only match this outdoor unit with a matched indoor
coil or air handler approved for use with this outdoor
unit per the unit manufacturer’s specification sheet.
The use of unmatched coils or air handler will likely
result in a charge imbalance between the cooling
and heating modes which can cause unsatisfactory
operation including a high-pressure switch lockout
condition.
Only use indoor coils approved for use on R-410A
systems. An R-22 coil will have a TXV or fixed
expansion device that is not designed to operate
properly in an R-410A system and will result in
serious operational issues. The R-22 coil could also
contain a significant amount of mineral oil which
is incompatible with the POE oil used in R-410A
systems and could result in reliability issues with the
compressor and expansion devices.
When the indoor coil or air handler is installed over a
finished ceiling and/or living area, it is required that an
auxiliary overflow pan be constructed and installed
under the entire indoor unit. Failure to do so can
result in property damage.
UNIT MAY START SUDDENLY AND WITHOUT
WARNING. The 7 segment LED on the Outdoor
Control will flash c or C when a call for unit operation
is present, but the unit is in temporary lockout.
The variable speed outdoor control will attempt to
start unit after the anti-short cycle time expires or
when a high or low pressure control automatically
resets.
•
This product is not approved for installation at 2000
meters [6561 feet] above sea level or higher. Installation
at higher altitudes may result in control and unit
failures due to electrical arc tracking between electrical
components on the invertor drive control board. Possibly
resulting in fire, electrical shock, property damage,
personal injury, or death.