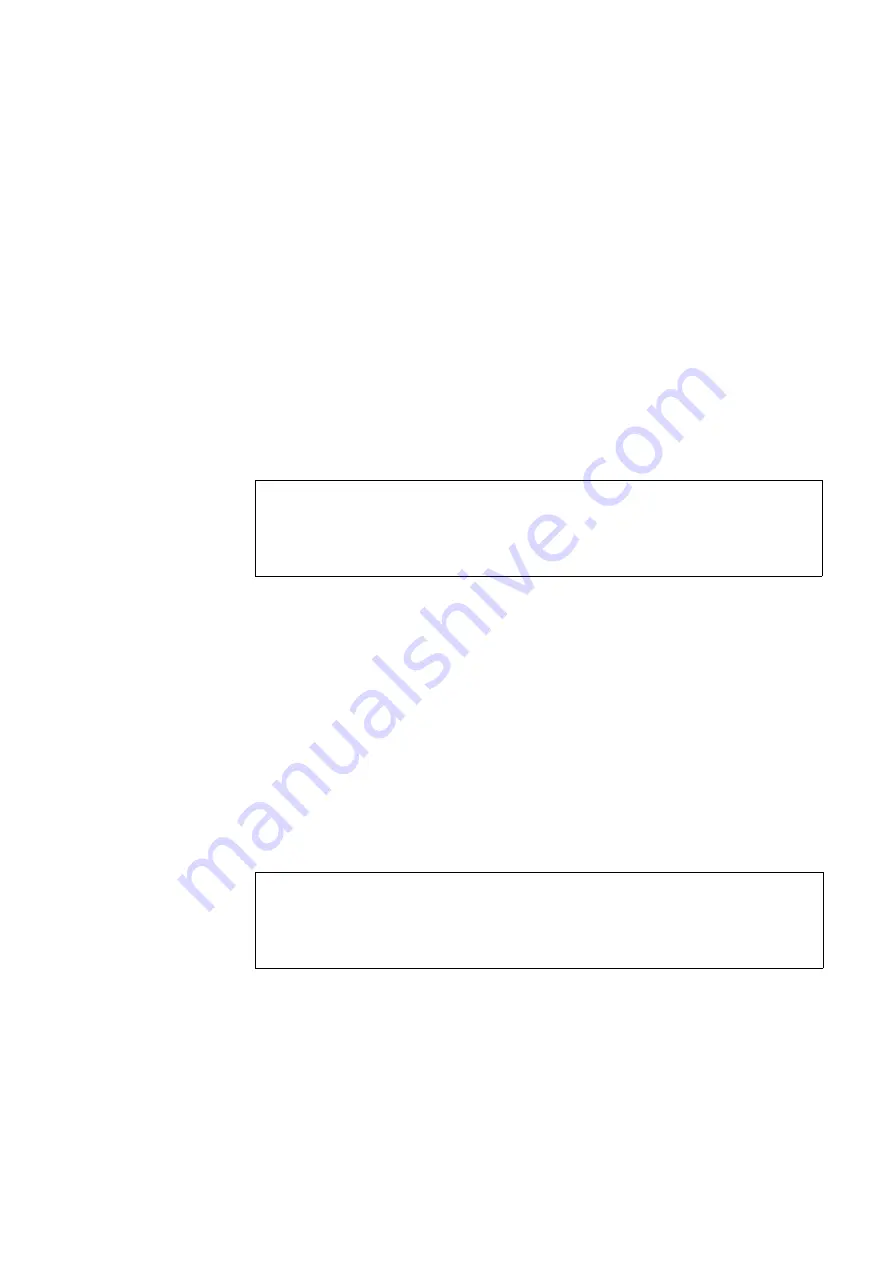
2 Engineering
2.10 Switching to the output side
50
DC1…20… and DC1…OE1 Variable Frequency Drives
02/20 MN040059EN
www.eaton.com
2.10 Switching to the output side
Typical applications for switching at the DC1 variable frequency drive’s
output include:
•
Cases in which a bypass circuit is implemented.
•
Cases in which it must be possible to switch on various motors as
necessary.
•
Cases in which several motors are connected in parallel and need to be
switched individually.
•
Cases in which the motor must be de-energized quickly in the event of
an emergency switching off (safety shutdown).
When an individual motor is switched off, the inverter needs to be disabled
first (the FWD/REV enable signal must be switched off) before the contacts
(contactor, switch-disconnector) on the variable frequency drive’s output side
are opened.
In cases in which the output is switched to a running motor, parameter P-33
must have a value of 1 (flying restart circuit enabled). When this condition is
met, the DC1 variable frequency drive will be automatically synchronized
with the running motor with the enable signal (FWD/REV).
2.10.1 Contactors
The contactors on the output side of DC1 variable frequency drives need to
be sized based on utilization category AC-3 (IEC/EN 60947-4-1) for the
assigned rated motor current and the corresponding rated operating voltage.
When a motor is being switched off, the DC1 variable frequency drive’s
output (inverter) must be disabled (the FWD/REV enable signal must be
switched off) before the contacts are opened.
NOTICE
Switching off during operation in vector mode (P-60 = 0 / 2 / 3 / 4)
is not permissible and may result in damage to the switching
device and the variable frequency drive.
NOTICE
Switching off during operation in vector mode (P-60 = 0 / 2 / 3 / 4)
is not permissible and may result in damage to the contactor and
the variable frequency drive.
→
Vacuum contactors should not be used at a variable frequency
drive’s output, as they are not suitable for switching at low
frequencies.