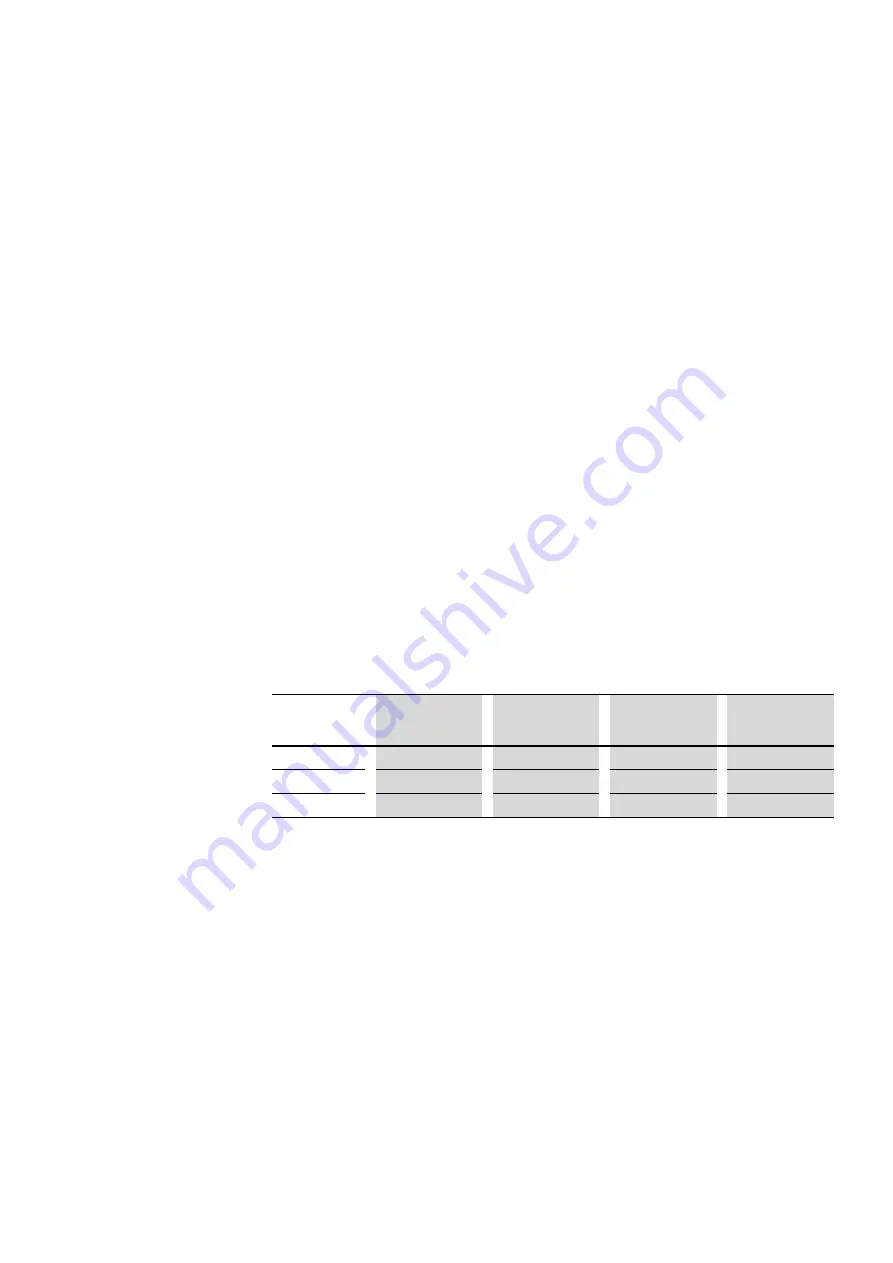
2 Engineering
2.7 Braking resistances
DC1…20… and DC1…OE1 Variable Frequency Drives
02/20 MN040059EN
www.eaton.com
45
2.7 Braking resistances
In certain operating states, the motor may run as a generator in certain
applications (regenerative braking operation).
Examples include:
•
Lowering in hoisting gear and conveyor applications,
•
Controlled speed reduction in the case of large load inertias
(flywheels),
•
A fast speed reduction in dynamic travel drives.
When the motor operates as a generator, its braking energy will be fed into
the variable frequency drive’s DC link via the inverter. DC link voltage U
DC
will be increased as a result. If the voltage value is too high, the DA1 variable
frequency drive will disable its inverter, after which the motor will coast
uncontrolled.
If there is a braking chopper and a connected braking resistance R
B
, the
braking energy fed back into the variable frequency drive can be dissipated in
order to limit the DC link voltage.
DC1-…B-A… variable frequency drives (frame sizes FS2, FS3, and FS4)
feature an integrated braking chopper. The brake resistors are connected to
the internal braking transistor with terminals DC+ and BR so that they will be
connected in parallel to the DC link. In addition to this, the braking chopper
must be enabled using parameter P-34 (= 1 or = 2).
The braking chopper will be switched on automatically if the braking energy
being fed back causes the DC link voltage to increase to the switch-on
voltage’s magnitude.
For example, in the case of DC1-34… variable frequency drives, the braking
chopper will be switched on at a DC link voltage of approximately 780 V DC
and then back off at 756 V DC. During this stage, the braking transistor and
the brake resistor will be active continuously.
Device series
Mains
connection
Voltage class
Braking chopper
on
Braking chopper
off
DC1-12…
Single-phase
230 V
390 V
378 V
DC1-32…
Three-phase
230 V
390 V
378 V
DC1-34…
Three-phase
400 V
780 V
756 V