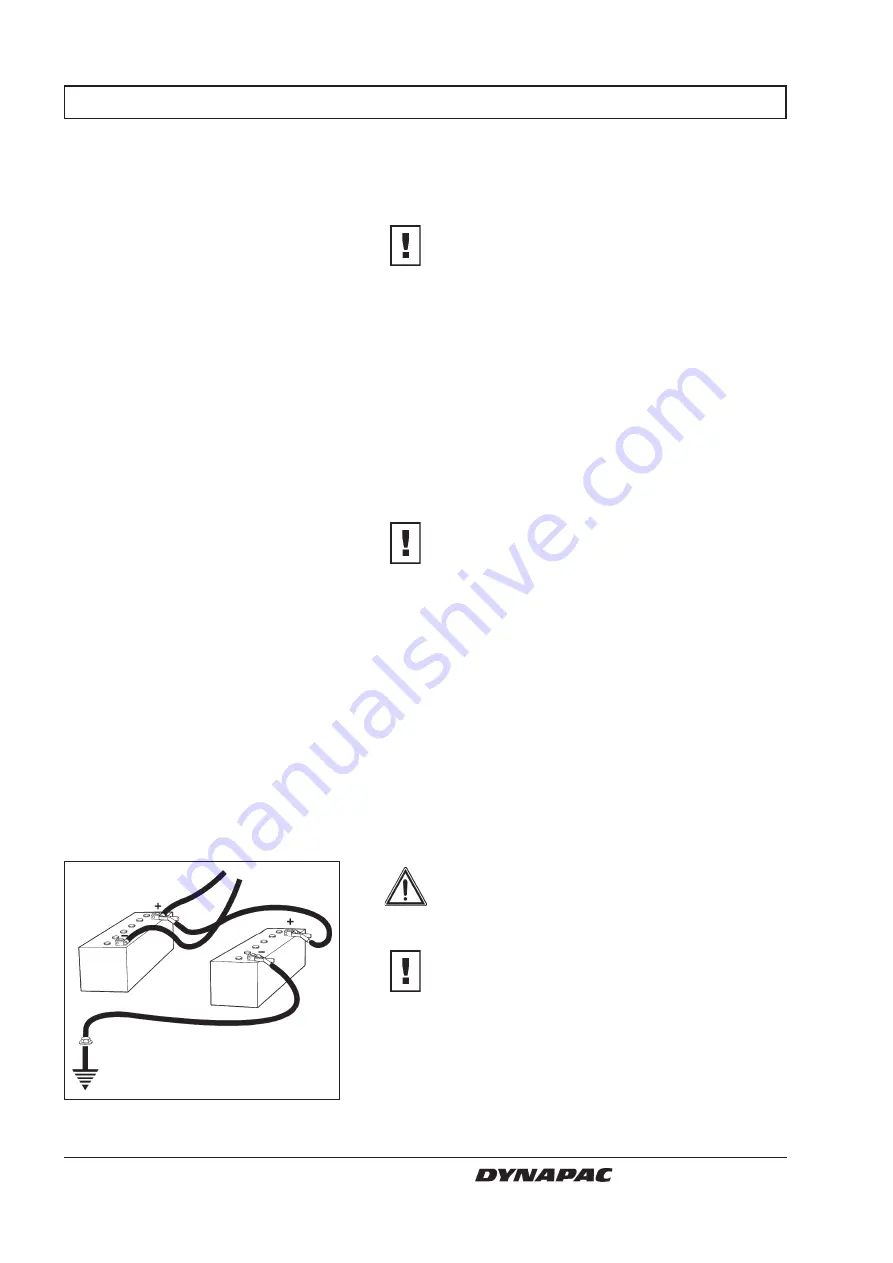
24
CC82/92 M092EN3
SPECIAL INSTRUCTIONS
Do not connect the negative cable to the
negative pole of the discharged battery,
because in the event of a spark, the oxyhy-
drogen gas that is emitted around the bat-
tery could explode.
Always ensure that voltage of the jump-start
battery is the same as that of the discharged
battery.
Switch off the ignition and all power consuming items.
Switch off the engine in the assisting machine. First
connect the positive pole of the jump-start battery to the
positive pole of the discharged battery and then connect
the negative pole of the jump-start battery to a bolt or the
engine lifting lug in the machine to the discharged
battery. Start the engine of the assisting machine and let
it run for a while. Attempt to start the other machine.
Disconnect the cables in the reverse order.
Standard oils and other
recommended fluids
Higher ambient temperature
above +40°C (104°F)
The temperature limits apply to standard versions of the roller.
Rollers that are fitted with additional equipment, such as
noise suppression, etc, may require extra observation in
the higher temperature ranges.
Temperature
High-pressure washing
Never aim a water jet directly at the cap of the
fuel tank or hydraulic reservoir. This is
especially important when using a high-
pressure jet.
Do not spray water directly on electric components or
the instrument panel. Put a plastic bag over the filler
cap of the fuel tank and secure with an elastic band.
This will prevent water from entering the venting hole in
the filler cap. This could otherwise cause operational
disturbance, such as a clogged filter.
In the event of fire in the machine, use an ABE powder
fire extinguisher if possible. A BE-type carbon dioxide
fire extinguisher may also be used.
If the roller is equipped with a protective structure
(ROPS, Roll Over Protective Structure), or protective
cab, the structure or cab must on no account be
subjected to welding or the drilling of holes. Never
attempt to repair a damaged structure or cab; they
must be replaced with new ones.
Fire fighting
Protective structure (ROPS)
On leaving the factory, the various systems and
components are filled with oil or fluid as indicated in the
Lubrication specification and are thus suitable for
operation in ambient temperatures between -10°C and
+40°C (14°F-104°F)
A maximum temperature of +35°C (95°F)
applies for biological hydraulic fluid.
The following recommendations apply for operation in
higher ambient temperatures, up to a maximum of
+50°C (122°F):
The diesel engine can be run at this temperature using
the normal oil, but for other components the following
fluids must be used: Hydraulic system using mineral
fluid Shell Tellus TX100 or equivalent. Other
components using transmission oil: Shell Spirax HD
85W/140, or equivalent.
Starting aid
Fig. 37 Starting aid
CAUTION
CAUTION
CAUTION
WARNING
Содержание CC 82
Страница 2: ...19 ILF015WO1...