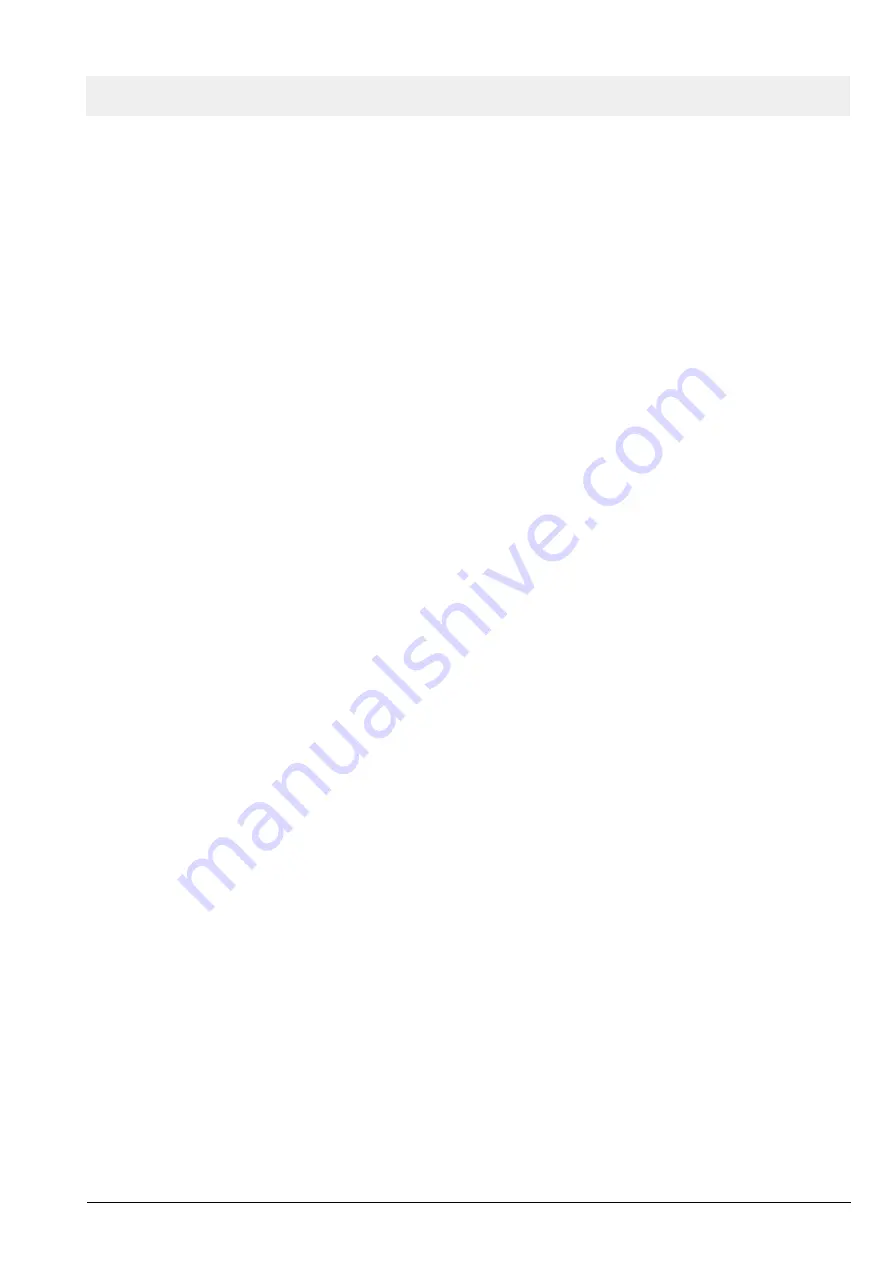
5133.001
All rig
ht
s reserved.
Copyright
re
se
rved.
V
e
rs
io
n
1
.0_
R
e
le
a
s
ed
_Pr
in
ted
on
_04
.05
.0
6_F5
13
300
1_
PC
B_
Box.
fm
19
Zeus
Function Description
The supply voltage for the TurboVent is externally stabilised in the power
supply unit to 48 V and has a current limit of 3 A. An external 68000 uF
capacitor is included to deal with the high peak currents of the motor.
The function of the blower power stage is to provide phase-adjusted activa-
tion of the motor coil with the aid of the Hall sensors built into the motor and to
control the speed of the motor. The Hall signals are formatted by an inverter
and passed to the Hall decoder. This module decodes the Hall signals of the
motor and codes the activation signals of the MOSFET driver from them. The
power MOSFETs are activated by a MOSFET driver. The output stage com-
prises 3 half-bridges each with two identical n-channel MOSFETs. At a Tur-
boVent electronics supply voltage below 38 V a protective circuit disables the
MOSFET activation. As the motor is run in a highly dynamic mode at high
speeds, the power stage is rated for a peak power output of approximately
480 W. The mean load in operation is approximately 100 W.
The fan delivers one pulse per fan wheel revolution. This pulse is filtered by
an RC element and routed to a retriggerable monoflop. If the pulses are not
received, the monoflop drops out and disables the power electronics for the
TurboVent. This ensures that the TurboVent is only activated when the fan is
running. This prevents harmful overheating or excessive oxygen concentra-
tion build-up at the TurboVent motor.
The Vent Power PCB also contains the activation electronics for the valves in
the breathing system and their interface to the TurboVent control computer.
Additionally, the Ventilator-OFF signal is evaluated by the DIANA PCB to cut
the power to the driver stages.
The A-cone valve is a single-turn bipolar valve. The turn must be activated in
bipolar mode by a voltage pulse. This valve driver is independent of the Ven-
tilator-OFF signal.
The power electronics for the flow valves are located directly at the pneu-
matic interface underneath the valves, and not on this PCB. However, the
valves are shut off by the Ventilator-OFF signal by way of a HIGH-side FET
switch on this module. The switch cuts the supply voltage to the flow valves.
The valves, seal, fresh gas, switch-over and BAG are controlled by a low-side
MOSFET switch. This module has a monitoring output which is routed to the
TurboVent control computer. The monitoring covers short-circuit and open
load.
3.4
External Flow PCB
3.4.1
Purpose
The “Alveon” flow sensor is designed for adult patient-local directional flow
measurement and is built into the patient Y-piece. The External Flow PCB
digitises the sensor signals and supplies the data via SPI.
3.4.2
External Flow PCB func-
tion
The External Flow PCB circuitry is divided into 3 areas (
Figure 6
):
–
Supply voltage with electrical isolation from the overall system
–
Analog measurement processing
–
Digital measurement processing with data interface and electrical isola-
tion from VERONA PCB via SPI
Содержание Zeus
Страница 1: ...5133 001 9036190 Revision 3 0 Because you care Technical Documentation Zeus Anesthetic workstation ...
Страница 2: ......
Страница 8: ...All rights reserved Copyright reserved K5133001IECIVZ fm 03 05 06 VI Contents ...
Страница 9: ...1 General ...
Страница 10: ...2 ...
Страница 15: ...7 Function Description ...
Страница 16: ...8 ...
Страница 85: ...77 Maintenance Procedures ...
Страница 86: ...78 ...
Страница 115: ...107 Schematics and Diagrams ...
Страница 116: ...108 ...
Страница 127: ......
Страница 128: ...119 Annex Technical Documentation acc to EMV standard IEC EN 60601 1 2 2001 Test List Spare Parts Catalogue ...
Страница 129: ...120 ...
Страница 133: ......
Страница 163: ......
Страница 165: ......
Страница 178: ......