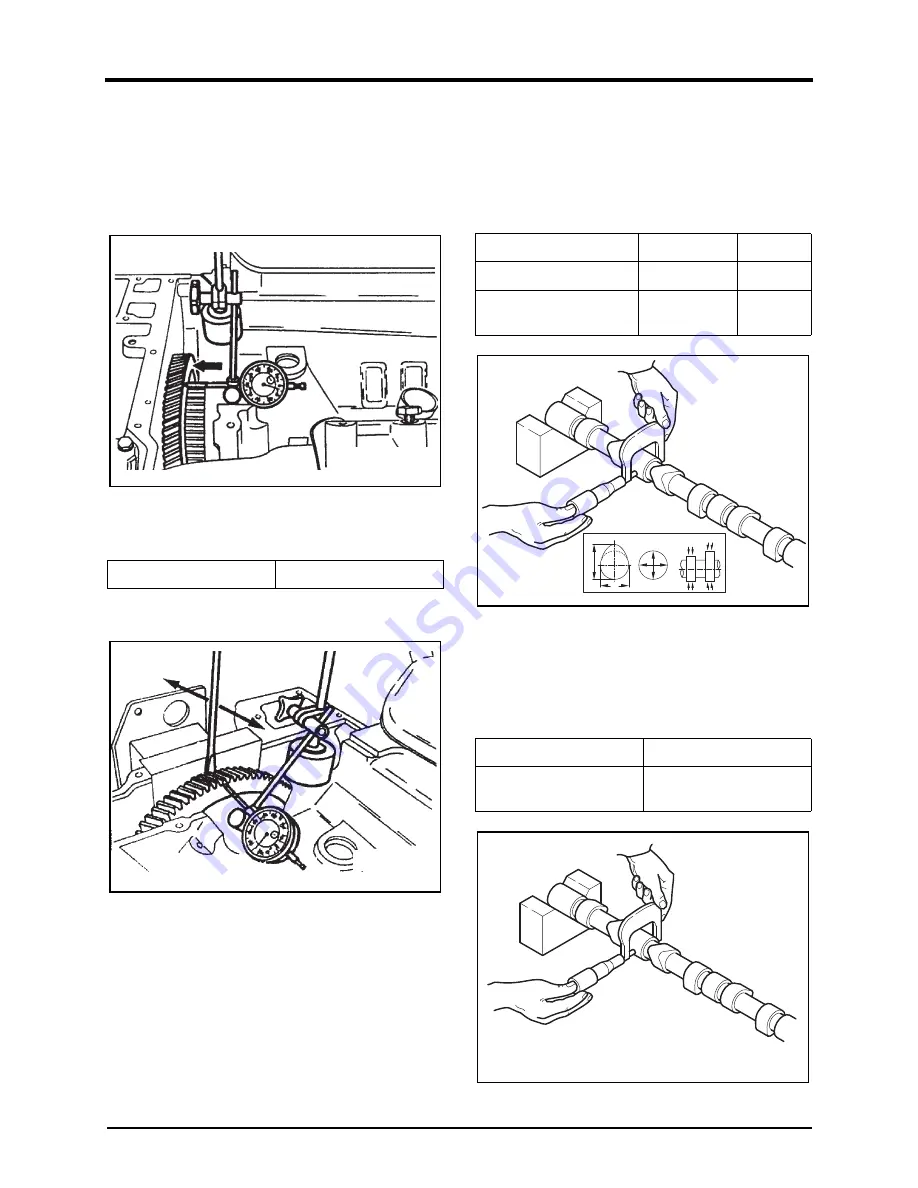
10. Cylinder block/head
179
Camshaft
Camshaft End Play
Measure the camshaf’st axial end play.
1. Push the camshaft toward the pulley side.
2. Place a dial gauge onto the camshaft gear.
DV2213130A
3. Measure the camshaft’s axial end play, moving the
camshaft gear by means of driver.
4. If excessive end play, assembly it by means of other
thrust washer.
DV2213131A
Check of Cam
1. Visual check: With inspecing the cam surface for any
damage with naked eyes and correct any minor
scratches by means of an oil stone grinding and if
severe, replace it.
2. Cam lobe height: Use a micrometer to measure the
cam lobe height and journal diameter. If the measured
number is less than the specified limit, the camshaft
must replaced.
DV2213132A
Check of camshaft
1. Camshaft bearing outer diameter: Using an outer
diameter micrometer, measure the outer diameter of
the camshaft bearing.
DV2213133A
Limit
Below 0.2 ~ 0.9mm
Item
Standard
Limit
Cam lobe height(C)
47.7mm
46.5mm
Cam bearing outside
(A,B)
Ø
56.0mm
Ø
55.6mm
Item
Standard
Camshaft bearing outer
diameter
Ø
69.91 ~
Ø
69.94mm
C
A
A
B
B
D
I II
I II