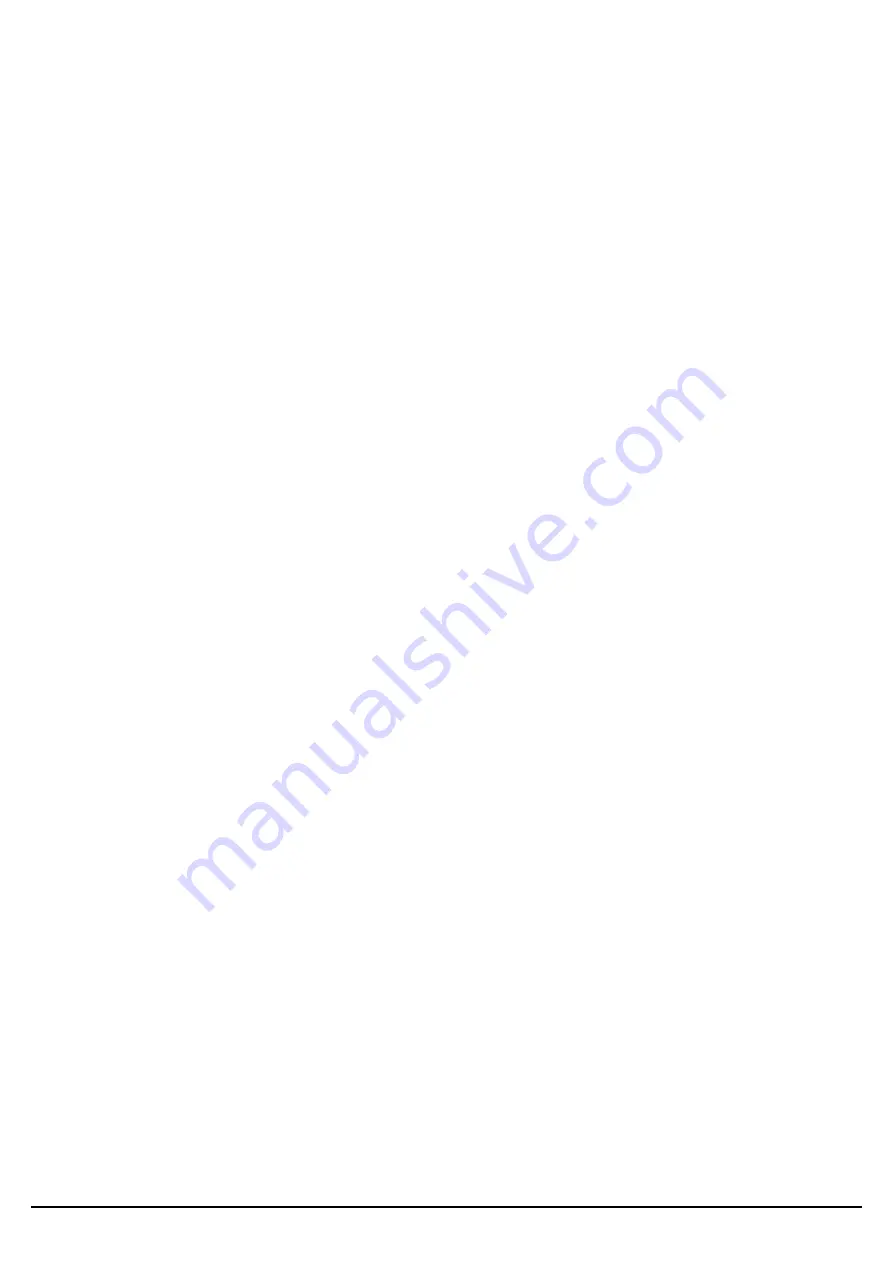
41
a.
Rotate rotor several times to seat bearing rollers. Left side bearing should be mounted
with minimum 0.0010” of internal radial clearance.
b.
Using a feeler gauge, insert a 0.0010” blade between two unloaded rollers at top of
bearing. Rotate rotor until blade is over a roller. The feeler gauge blade should pull out
with minimal force. Continue to rotate rotor and check in four different places.
c.
If feeler gauge blade cannot be pulled from bearing at all four locations, the bearing lock
nut is too tight. Remove bearing lock nut and pull withdrawal sleeve out slightly. Re-
peat process at less torque.
NOTE:
If a minimum of 400 ft. lbs. of torque cannot be achieved, contact your local Digga dealer.
d.
Remember a bearing lock washer tab must align with a slot in bearing lock nut.
21.
Remove rotor supports. After verifying that rotor spins freely, bend lock washer tab over tolock
bearing lock nut in place. Never back the bearing lock nut off to align lock washer tab, always
tighten bearing lock nut to achieve tab alignment.
22.
Reconnect the relief and grease lines (right lower bearing assembly only). Pump grease into the
bearing assemblies to be sure grease is coming out through the rollers of the bearing.
NOTE:
Use NLGI Grade 2 Lithium grease only. Grease must not contain any graphite or molybdenum
additives which will cause premature bearing failure.
23.
With outer seal cap removed, pump grease into bearing housing until it is approximately half full.
Do not over grease since this will cause excess heat generation during operation.
24.
Apply a light film of grease to o-ring and install on outer seal cap. Pack grease between dual lips
of shaft seal. Install outer seal cap onto bearing assembly.
NOTE:
Push off holes in the outer seal cap should be aligned with counter bore holes in housing to
prevent damage to housing during future maintenance. Secure in place using existing .25” socket
head cap screws and loctite 271. Torque to 12 ft. lbs.
25.
RIGHT LOWER BEARINGASSEMBLY
: Reinstall the belt, sprocket & covers following the
belt and sprocket installation procedure.
REPLACING AND/OR SERVICING THE OVERHUNG LOAD ADAPTER AND
HYDRAULIC MOTOR
NOTE:
An overhead hoist is recommended when removing the hydraulic motor and overhung load
adapter assembly.
NOTICE:
Due to the complexity of servicing the drive shaft, bearings and housing, these parts are
not replaceable. Hydraulic motor and overhung load adapter maintenance and service is limited to
replacing the gasket, seals and o-rings. All other field service will void warranty.
Remanufactured overhung load adapters are available from the factory. (Part #115443r = 2-bolt flange
overhung load adapter and part #115444r = 4-bolt flange overhung load adapter.) Contact customer
service for detailed instructions. Do not disassemble.
MAINTENANCE & SERVICE
QUALIFIED TECHNICIAN MAINTENANCE
PM-000102-A OCTOBER 2017
40
Содержание Magnum II Series
Страница 2: ......
Страница 56: ...Australian Designed and Manufactured PM 000102 A...