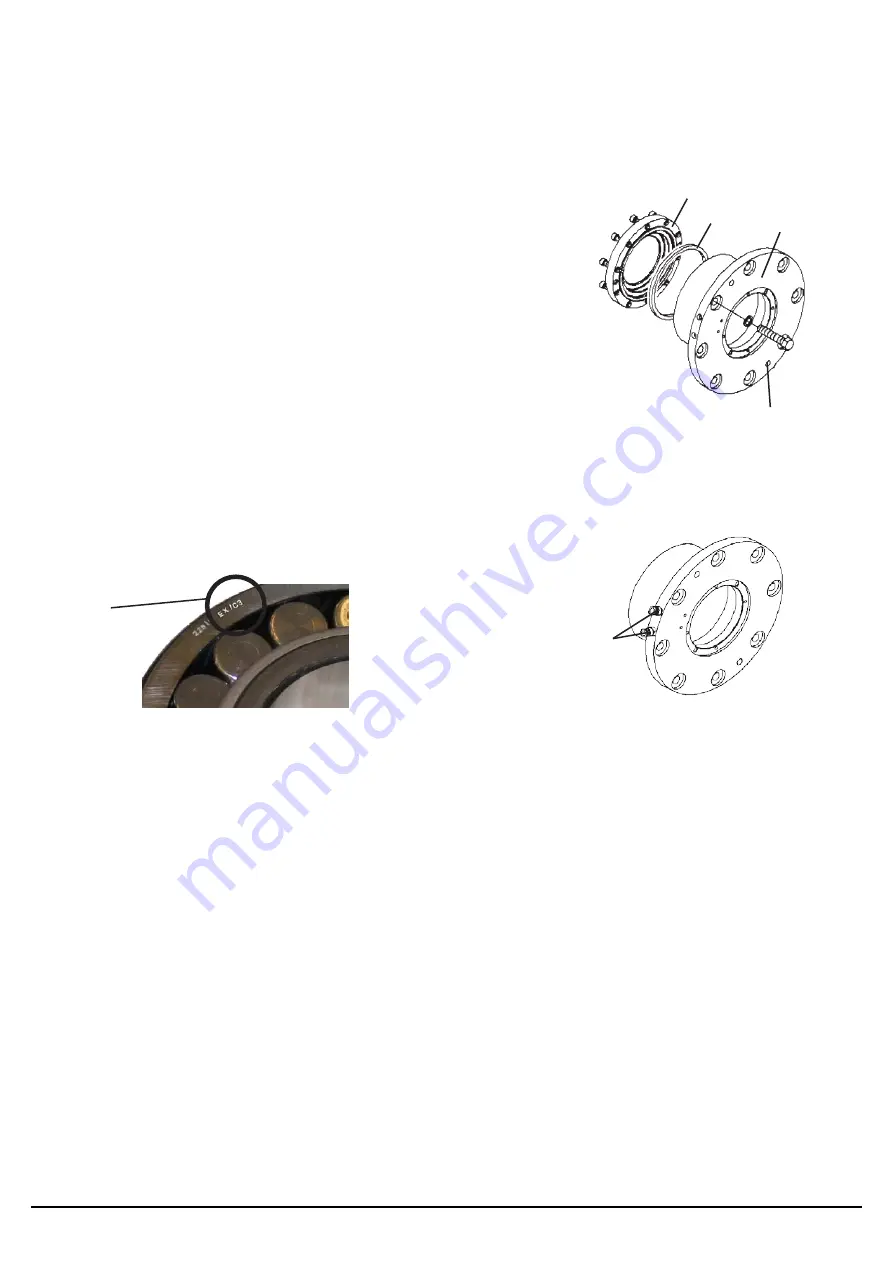
38
M
N
L
8.
Remove the eight .50” cap screws from the bearing housing
(L) and install two of them into the push off holes to aid in the
removal of the bearing housing. Remove the bearing housing.
NOTE:
When removing the cap screws on the left lower bearing housing
the grease fitting protection guard will also be removed.
9.
Remove the ten socket head cap screws from the inner seal cap
(M) and remove the inner seal cap and spacer ring (N - right
side bearing only).
NOTE:
Two of the cap screws may need to be installed into the push
off holes in the inner seal cap for removal.
10.
Slide or press the bearing out the back of the housing (L).
11.
Inspect the inside of the bearing housing, the withdrawal sleeve
and rotor shaft for defects, such as burrs, worn surfaces or any
surface imperfections. Inspect the rotor shaft seals for damage.
NOTE:
It is recommended to replace rotor shaft seals when replacing
bearings.
PUSH OFF HOLE
C3
LOWER RIGHT HOUSING
IDENTIFICATION
LOWER RIGHT BEARING IDENTIFICATION
NOTICE:
Although the left and right bearings look alike they are different. Be sure to identify and
install the correct bearing during replacement. The right side bearing #600-158 will have a “C3” on
the bearing rim while the left bearing #115439 will not. All other identification marks, letters and
numbers are related to manufacturer and do not have any significance in distinguishing between the
two bearings. Take extra care to install the correct bearing into the correct housing. The right bearing
housing will have the grease and relief ports on the outside flange diameter of the housing while the
left side bearing housing will have the grease and relief ports on the outside flange face of the
bearing housing.
12.
Clean all lower bearing components and rotor shaft, removing all grease and contaminants.
Apply a light coat of machine oil to the inside of the bearing housing and install the new bearing
with the smaller side of the taper in the bearing inner race to the inside of the housing. Check
diagram for correct bearing orientation.
a. Position the bearing as straight as possible with the bearing housing.
b. Position a tube over the bearing, contacting the outer race of the bearing only, and
lightly tap until the bearing is aligned with the housing.
c. Once alignment has been achieved the left side bearing will easily slide into place
while the right side bearing will need a press. Ensure right bearing is fully seated into
the housing.
NOTE:
Apply force to the outer race of the bearing only to prevent damage.
MAINTENANCE & SERVICE
QUALIFIED TECHNICIAN MAINTENANCE
PM-000102-A OCTOBER 2017
37
Содержание Magnum II Series
Страница 2: ......
Страница 56: ...Australian Designed and Manufactured PM 000102 A...