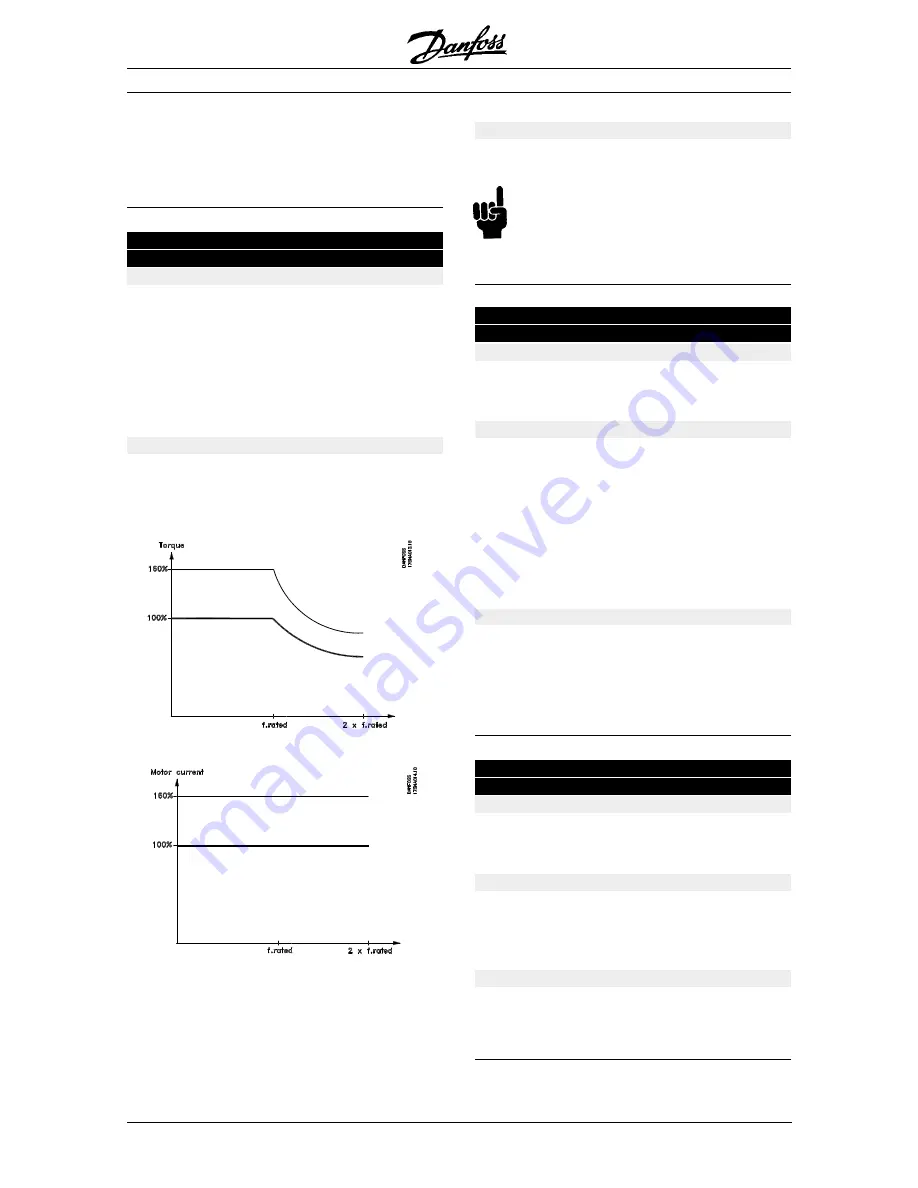
FCM 300 Series
51
MG.03.B6.02 - VLT is a registered Danfoss trademark
229 Frequency bypass, bandwidth
(FREQ BYPASS B.W.)
Settings:
0 (OFF) - 100%
[0-100]
✭
0 (OFF) %
[0]
Function:
Some systems call for some output frequencies to be
avoided because of resonance problems in the
system.
In parameters 230-231 these output frequencies can
be programmed for bypassing (Frequency bypass). In
this parameter (229), a bandwidth can be defined on
either side of these frequency bypasses.
Description of choice:
The bypass band is the bypass fre/- half the
set bandwidth.
A percentage of the setting in parameters 230-231 is
selected.
230 Frequency bypass 1 (FREQ. BYPASS 1)
231 Frequency bypass 2 (FREQ. BYPASS 2)
Settings:
0.0 - 132 Hz (parameter 200)
[0 - ]
✭
0.0 Hz
[0]
Function:
Some systems call for some output frequencies to be
avoided because of resonance problems in the
system.
Description of choice:
Enter the frequencies to be avoided.
See also parameter 229.
Refer
ences and Limits
If
Slow down
has been selected via one of the
terminals 2, 3, 4, or 5 (parameters 332 - 335), the
percentage (relative) value selected in parameter 219
will be deducted from the total reference.
221 Current limit for motor mode
(CURRENT LIMIT)
Settings:
Min. limit (XX.X) - max. limit (XXX.X)
in % of I
RATED
[XXX - XXXX]
✭
Max. limit (XXX.X)
[XXXX]
I
RATED
= rated motor current
Min. limit = magnetising current in % of I
RATED
Max. limit = unit dependent limit in % of I
RATED
Function:
This function is relevant for all application
configurations; speed and process regulation. This is
where to set the current limit for motor operation.
✭
=
factory setting. ( ) = parameter window text. [ ] = value for use in communication via serial communication port
Description of choice:
Set the desired % of current.
NB!
NB!
NB!
NB!
NB!
For motors with 2 poles (0.55 + 1.1 kW), the
setting is limited to 120% which corresponds
to 160% torque, setting 73% corresponds to
100% torque.