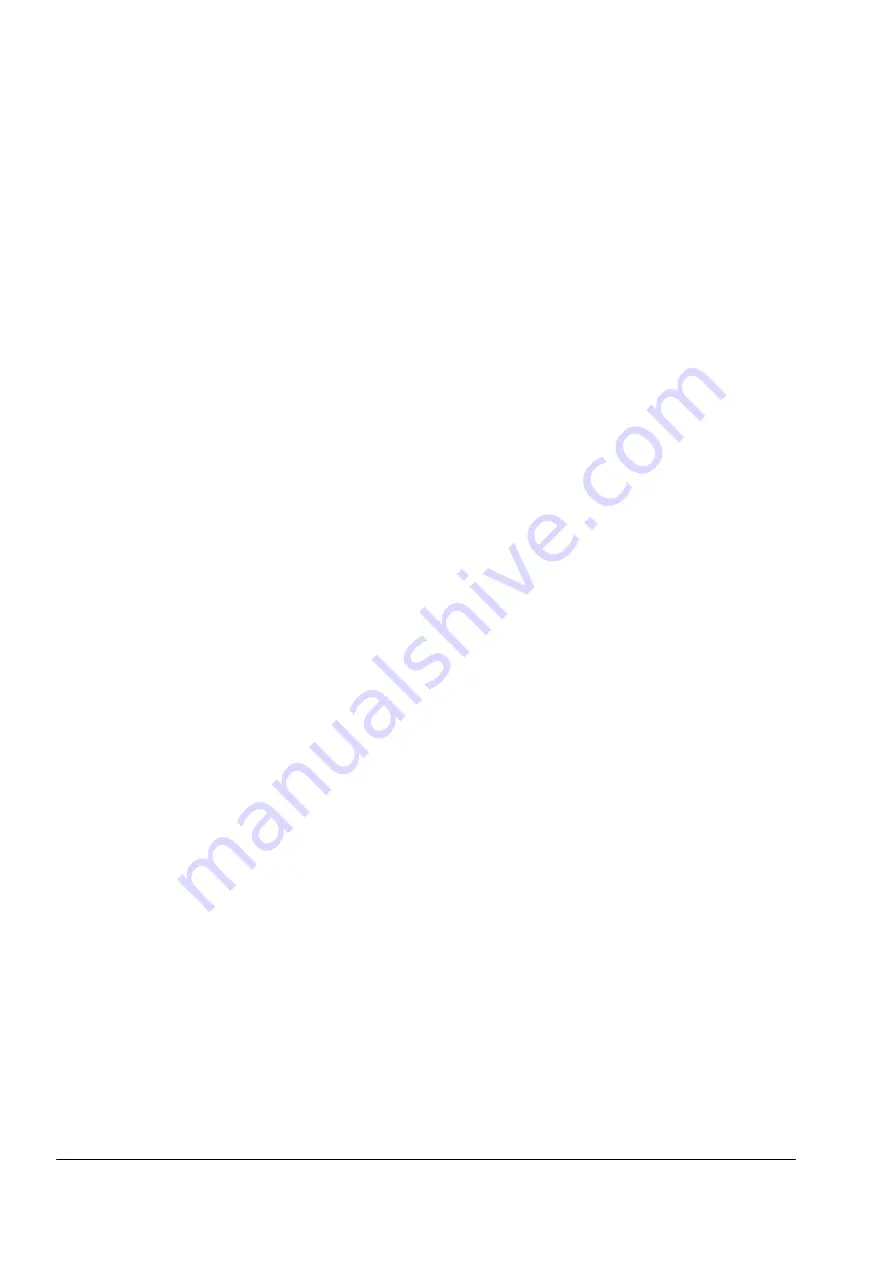
26.04.2005
Overview
advanced speed ramping functionality within the Speed Control block. The Speed Control is
implemented in software, with operating characteristics set by programmable parameters.
2.1.4 F
LUX CONTROL
The motor flux is controlled within the Flux Control. The Magnetization Current, which produces
the motor flux, and the Slip Gain, which is reciprocally proportional to the Magnetization Current,
is the outputs from the Flux Control. Since the motor flux depends on the motor speed, the
measured motor speed is used to determine the optimal magnetization flux level.
2.1.5 S
LIP AND STATOR FREQUENCY ESTIMATION
The Slip Speed and the Stator Frequency is estimated in the Slip and Stator Frequency
Estimation. The Slip Speed is computed from the Slip Gain and the Torque Current. The Stator
Frequency that is integrated in the Current Control to get the position of the dq-plane is computed
as the sum of the Actual Speed (electrical) and the Slip Speed.
2.1.6 C
URRENT CONTROL AND
SPWM-
SYM
The dq-plane implemented current controller (so called vector control) controls the magnetization
current and the torque producing current independently of each other. The software implemented
Current Control is able to compensate for temperature and frequency related changes in motor
winding impedance as well as variations in the DC-supply voltage, thereby providing precise
control of motor flux and torque over a wide range of operating conditions. The Current Control
computes the required motor voltage, which is then realized by SPWM-sym (Sinusoidal Pulse
Width Modulation with symmetrisation). The output from the SPWM-sym block is the MOSFET
gate pulses.
2.1.7 P
OWER CONVERSION SECTION
The principal drive output, a variable frequency, variable amplitude, three phase current, is
produced by the Power Conversion section from a DC power source.
circuit configuration. Depending on its current rating, a SuperDrive may employ more or less
transistors than illustrated in
. During braking, regenerated energy from the motor is
returned to the battery.
All power components are mounted and thermally bonded to a large heatsink that forms one
surface of the drive. Heatsink temperature and DC supply voltage are sensed and monitored for
control and protection purposes.
Utilizing efficient MOSFET power transistors, the Power Conversion section amplifies three PWM
(Pulse Width Modulated) current commands supplied by the Current Regulator producing three
PWM voltages (see
). These PWM voltage waveforms, when applied to the inductance
of the stator, produce currents in the motor, which approximate sine waves.
User's Guide 1.0
Item No.
89Y05120A
15
Содержание SuperDrive ACS24 Series
Страница 12: ......
Страница 34: ......
Страница 38: ......
Страница 79: ...26 04 2005 Troubleshooting guide User s Guide 1 0 Item No 89Y05120A 79...
Страница 81: ...26 04 2005 Troubleshooting guide User s Guide 1 0 Item No 89Y05120A 81...
Страница 82: ...Troubleshooting guide 26 04 2005 Item No 89Y05120A User s Guide 1 0 82...
Страница 86: ...Troubleshooting guide 26 04 2005 7 7 11 CAN TIME OUT Error Code 0x8100 Item No 89Y05120A User s Guide 1 0 86...
Страница 92: ......