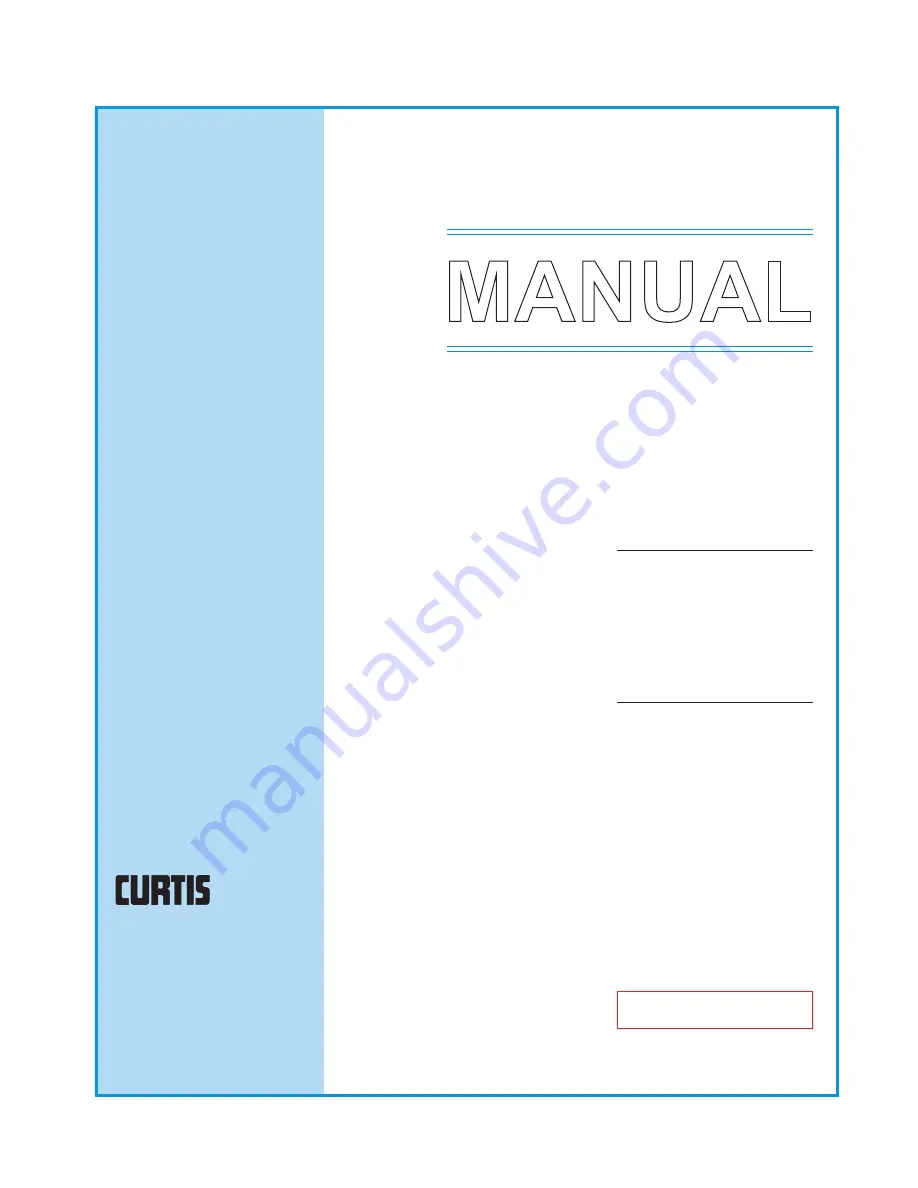
MANUAL
© 2002 CURTIS INSTRUMENTS, INC.
DESIGN OF CURTIS PMC 1200 SERIES
CONTROLLERS PROTECTED BY U.S.
PATENT NO. 4626750.
CURTIS INSTRUMENTS, INC.
200 Kisco Avenue
Mount Kisco, NY 10509 USA
Tel: 914-666-2971
Fax: 914-666-2188
www.curtisinst.com
1243
GEN
2 Manual, p/n 37044
Rev. A: October 2002
1 2 4 3
M
O
D
E
L
MultiMode™
MOTOR CONTROLLER
Generation 2