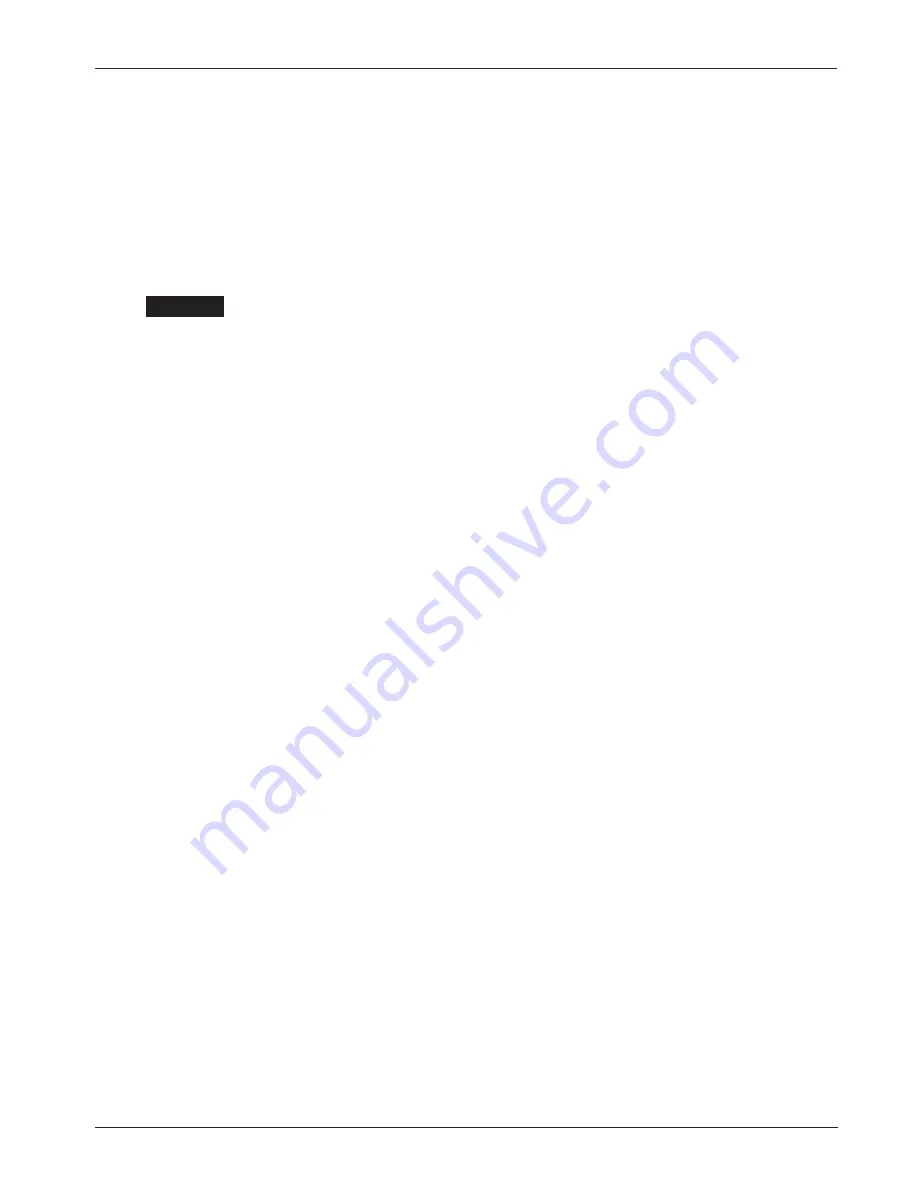
Curtis 1243
GEN
2 Manual
16
2 — INSTALLATION & WIRING:
Emerg. Reverse and Aux Driver
☞
C A U T I O N
WIRING: Emergency Reverse
To implement the emergency reverse feature, Pin 13 (the emergency reverse
input) must be connected to battery voltage as shown in the standard wiring
diagram, Figure 3.
The controller provides maximum braking torque as soon as the emer-
gency reverse switch is closed. The vehicle will then be automatically driven in
the reverse direction at the programmed emergency reverse current limit until
the emergency reverse switch is released.
CAUTION:
The polarity of the
S1
and
S2
connections will affect the
operation of the emergency reverse feature. The forward and reverse switches
and the
S1
and
S2
connections must be con
fi
gured so that the vehicle drives
away from the operator when the emergency reverse button is pressed.
WIRING: Emergency Reverse Check
An optional wire connected directly to the emergency reverse switch provides for
broken wire detection when that feature is programmed On (see Section 3,
page 43). The emergency reverse check output wire periodically pulses the
emergency reverse circuit to check for continuity in the wiring. If there is no
continuity, the controller output is inhibited until the wiring fault is corrected.
The emergency reverse check wire is connected to Pin 10 as shown by the
dotted line in the standard wiring diagram, Figure 3. If the option is selected
and the check wire is not connected, the vehicle will not operate. If the option
is not selected and the check wire is connected, no harm will occur
—
but
continuity will not be checked.
WIRING: Auxiliary Driver
The 1243
GEN
2 provides an auxiliary driver at Pin 8. This low side driver is
designed to energize an electromagnetic brake coil, as shown in the standard
wiring diagram (Figure 3). The output is rated at 2 amps and is overcurrent
protected. A coil suppression diode is provided internally to protect the driver
from inductive spikes generated at turn-off. The recommended wiring is shown
in the standard wiring diagram, Figure 3. The contactor coil or driver load
should not be connected directly to B+, which would cause the controller to be
always biased On via a path through the coil suppression diode to the KSI input.
Although it is typically used to drive an EM brake, the auxiliary driver can
be used to drive a pump contactor or hydraulic steering assist in applications
not requiring an EM brake.
Note: Because the auxiliary driver is typically used for an EM brake, the
programmable parameters related to this driver are described in the electromag-
netic brake parameter group; see page 28.