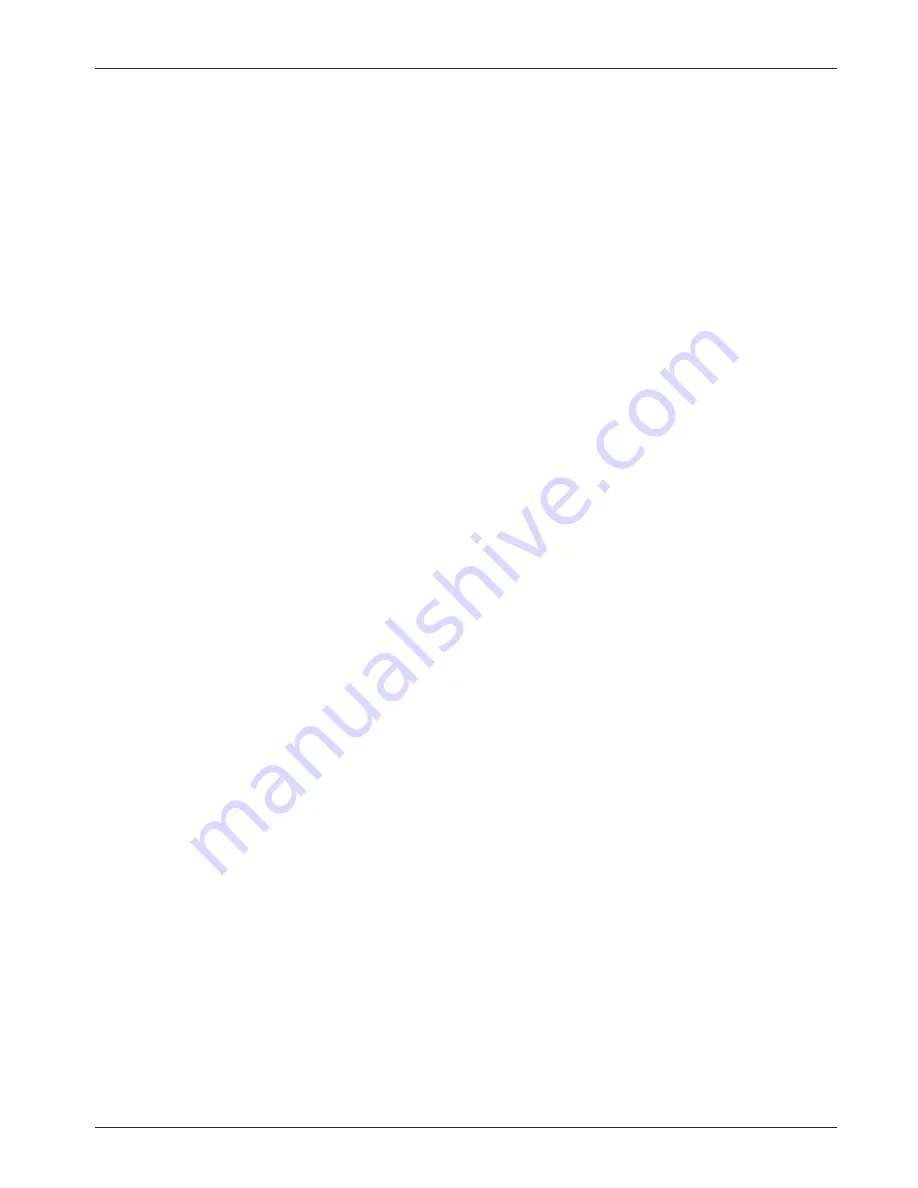
Curtis 1243
GEN
2 Manual
A-3
APPENDIX A: EMC & ESD DESIGN CONSIDERATIONS
applied to the base material. If the ohmic contact itself is not continuous, the
shielding effectiveness can be maximized by making the joints between adjacent
pieces overlapping rather than abutted.
The shielding effectiveness of an enclosure is further reduced when a wire
passes through a hole in the enclosure. RF energy on the wire from an external
fi
eld is re-radiated into the interior of the enclosure. This coupling mechanism
can be reduced by
fi
ltering the wire at the point where it passes through the
boundary of the shield. Given the safety considerations involved with connect-
ing electrical components to the chassis or frame in battery powered vehicles,
such
fi
ltering will usually consist of a series inductor (or ferrite bead) rather than
a shunt capacitor. If a capacitor is used, it must have a voltage rating and leakage
characteristics that will allow the end product to meet applicable safety regula-
tions.
The B+ (and B-, if applicable) wires that supply power to the throttle
control panel
—
such as for the keyswitch
—
should be bundled with the remain-
ing throttle wires so that all these wires are routed together. If the wires to the
control panel are routed separately, a larger loop area is formed. Larger loop
areas produce more ef
fi
cient antennas which will result in decreased immunity
performance.
ELECTROSTATIC DISCHARGE (ESD)
Curtis motor controllers contain ESD-sensitive components, and it is therefore
necessary to protect them from ESD damage. Electrostatic discharge (ESD)
immunity is achieved either by providing suf
fi
cient distance between conduc-
tors and the outside world so that a discharge will not occur, or by providing an
intentional path for the discharge current such that the circuit is isolated from
the electric and magnetic
fi
elds produced by the discharge. In general the
guidelines presented above for increasing the radiated immunity will also
provide increased ESD immunity.
It is usually easier to prevent the discharge from occurring than to divert
the current path. A fundamental technique for ESD prevention is to provide
adequately thick insulation between all metal conductors and the outside
environment so that the voltage gradient does not exceed the threshold required
for a discharge to occur. If the current diversion approach is used, all exposed
metal components must be grounded. The shielded enclosure, if properly
grounded, can be used to divert the discharge current; it should be noted that
the location of holes and seams can have a signi
fi
cant impact on the ESD
suppression. If the enclosure is not grounded, the path of the discharge current
becomes more complex and less predictable, especially if holes and seams are
involved. Some experimentation may be required to optimize the selection and
placement of holes, wires, and grounding paths. Careful attention must be paid
to the control panel design so that it can tolerate a static discharge.