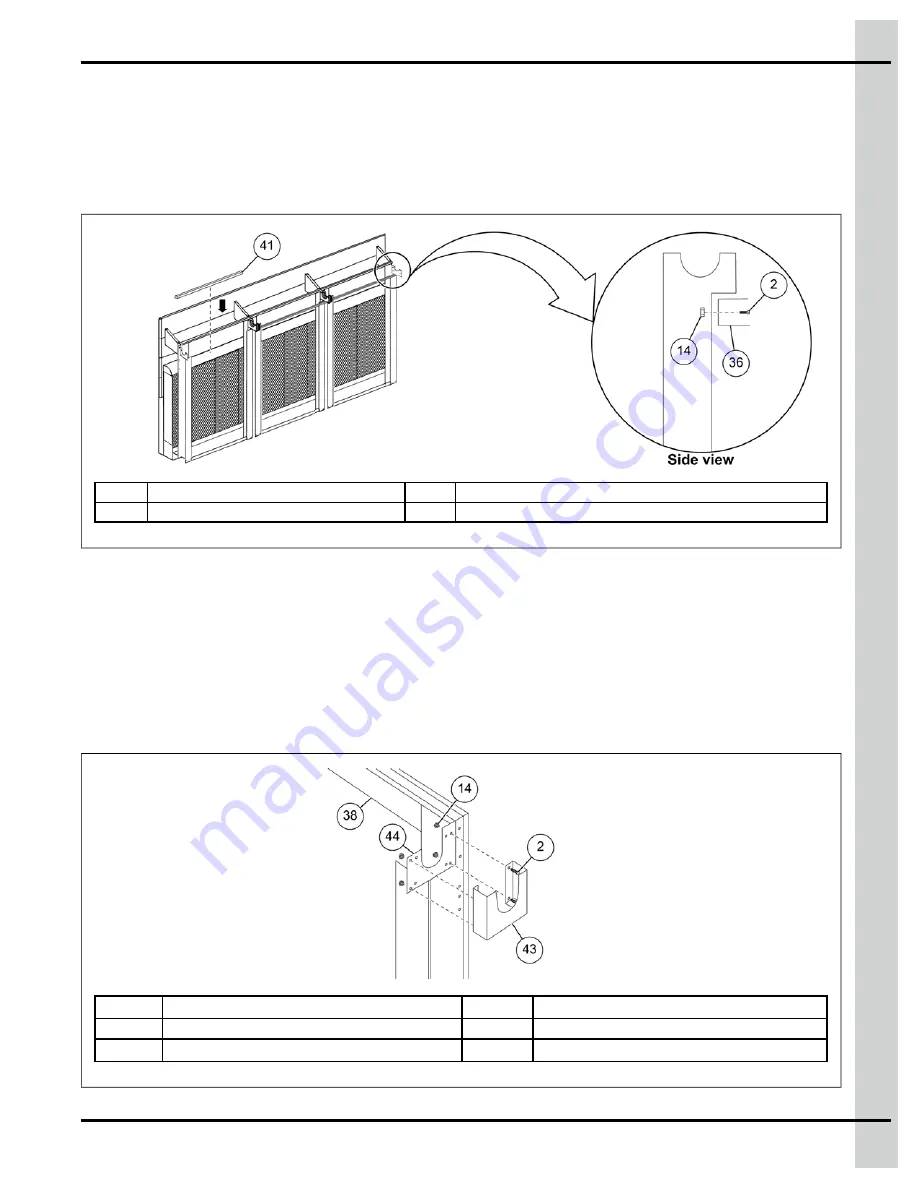
Installing the Top Bar
Mount the top bars (41) to the face of the track with under the mounting brackets (36) using 1/4"-20 x 1/2"
hex bolts (2) and 1/4" hex nuts (14).
NOTE:
Make sure the hook and loop strips are pointed upward.
Figure 3-12
Installing the top bar
2
1/4"-20 x 1/2" hex bolt
36
Mounting brackets
14
1/4" hex nut
41
Top bar
Installing the Bearing Mount
Attach the bearing mount (43) to the track (44) at the end of the system, opposite to the motor using
1/4"-20 x 1/2" hex bolts (2) and 1/4" hex nuts (14) provided.
NOTE:
Install bolts (2) and nuts (14) to the four holes as indicated in the guide bracket.
Figure 3-13
Installing the bearing mount
2
1/4"-20 x 1/2" hex bolt
43
Bearing mount
14
1/4" hex nut
44
Track
38
Back plate
4801-5405
Unitized System Komfort Kool
25