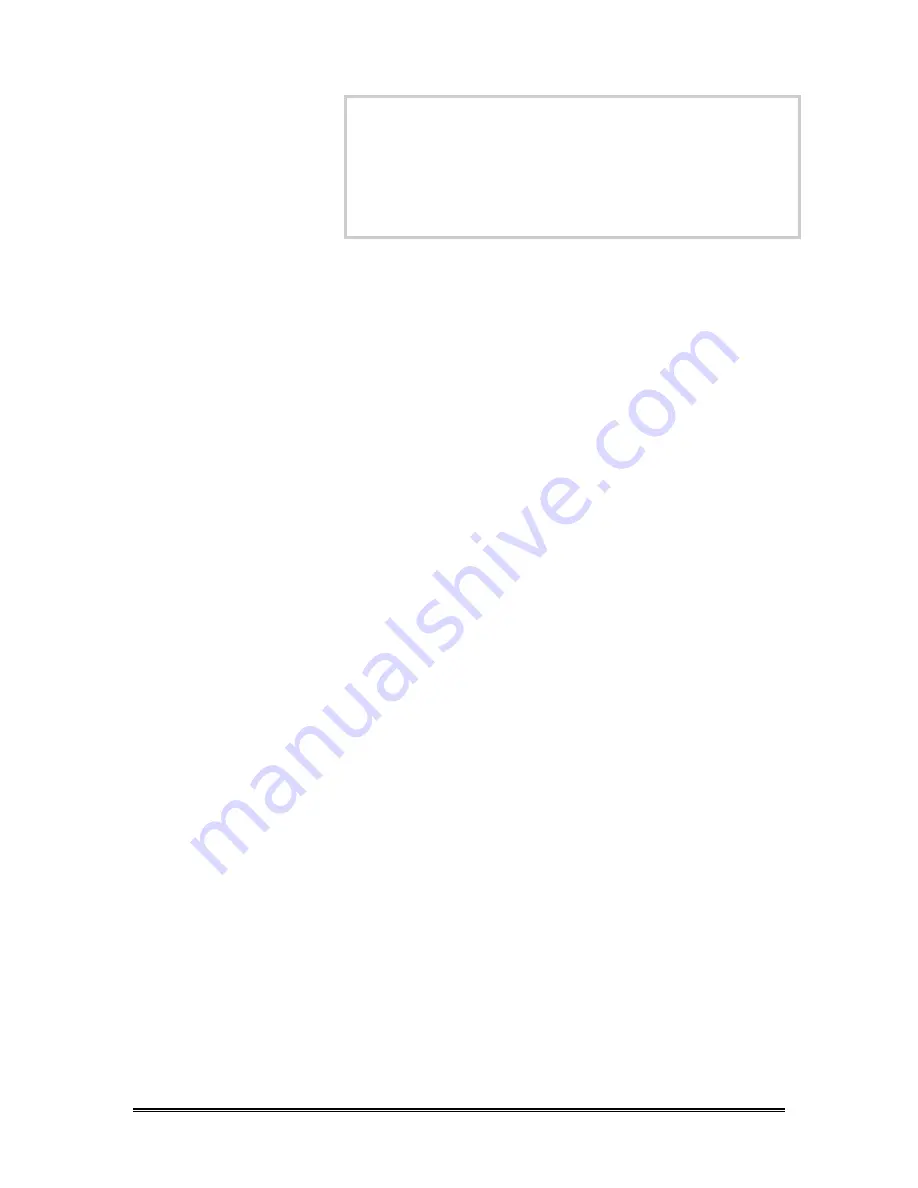
Crest Ultrasonics Corp.
Manual #9907-103-OJSTD
•
Page 43
3.2 USE OF SPECIAL OPTIONS:
Auto Rinse Water Flow Control
(via Resistivity Probe and Controller
in Conjunction with a Solenoid Valve)
F.
Auto Rinse Water Flow Control (via Resistivity
Probe
and Controller in Conjunction with a Solenoid
Valve)
General information:
This optional feature allows
you to determine a relative measure of purity for
liquid in a processing tank and to introduce fresh
water automatically via a solenoid valve to raise the
“freshness level” as required.
A higher resistivity reading indicates a relatively
purer/cleaner state of the water in a tank. A lower
resistivity reading indicates that contaminating
particulates have been introduced into the water
which are conductive (capable of carrying an
electric charge).
When the resistivity monitor option is installed on a
Crest ultrasonic cleaning console, resistivity may
be “read” by a probe that is typically situated in the
overflow weir between two rinse tanks. (Thus, it
“reads” the liquid at the reverse cascade overflow
point from the last rinse tank, i.e., the cleanest tank
of the system, to the previous rinse tank.) The
resistivity level is displayed on a controller, which
consists of a meter and output.
During normal processing, the controller will give
an output signal when resistivity falls below your
pre-set level (indicated by a red light on the
controller). Output goes through a relay, and the
solenoid valve on the incoming clean rinse water
line is triggered to open. Valve allows fresh water
to pass into the subject tank until the resistivity
level surpasses the setpoint (indicated by green
light). Then the valve closes.
For many cleaning applications a resistivity reading
of
1-2 megohm
is sufficient for the final rinse. For
high precision applications, resistivity
up to 10
megohm or greater
may be required.