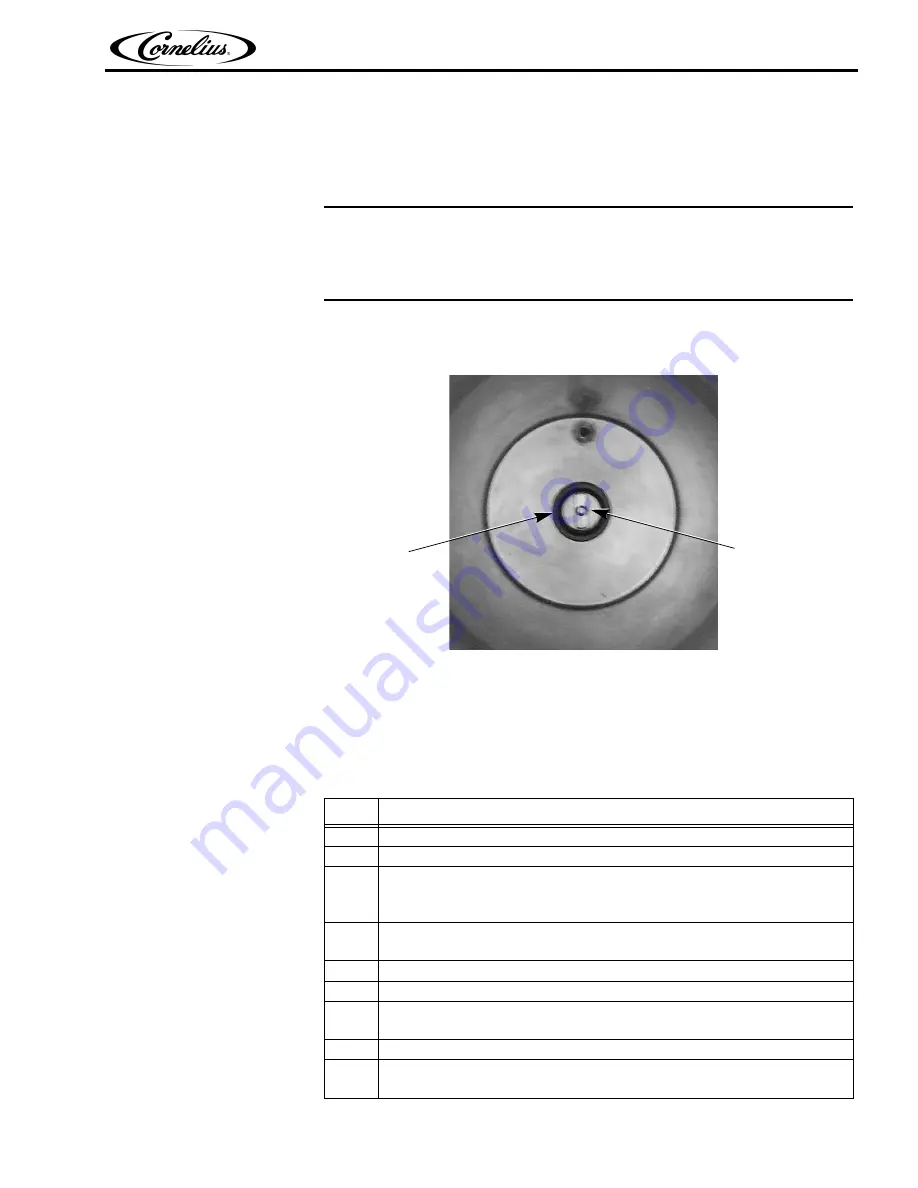
Viper Service Manual
© 2008-2012, IMI Cornelius Inc.
- 61 -
Publication Number: 621260373SER
COMPONENT REPLACEMENT
The following are procedures for servicing the major components of the Viper
system.
B
ARREL
M
OTOR
S
EAL
R
EPLACEMENT
The barrel motor seal is typically replaced during the semi-annual preventative
maintenance procedure. The seal location is shown in Figure 40.
Figure 40. Front View Inside of Barrel w/ Faceplate off
Removing the Existing Seal
To remove the existing barrel seal, perform the procedure in Table 43..
Motor
Seal
Motor
Shaft
Table 43.
Step
Action
1.
Purge the barrel. See “Purging a Barrel” on page 36.
2
When purging is complete, disconnect power from the unit.
3
Open the relief valve on the front of the barrel to ensure that pressure is
released.
CAUTION:
Barrel pressure
MUST
be relieved before removing the
faceplate!
4
Remove the four (4) 3/4 in. nuts from the faceplate and slowly remove the face-
plate from the unit.
5
Carefully pull the blade assembly out of the barrel.
6
Remove any remaining product from the barrel.
7
Rinse and inspect the blade assembly and barrel for signs of wear. (Replace if
necessary)
8
Remove the seal and spacer from the rear of barrel.
9
When old seal and spacer are removed, use a clean soft cloth to clean
between the motor shaft and the barrel to remove any remaining product.
Содержание VIPER 2 FLAVOR
Страница 83: ...Viper Service Manual 2008 2012 IMI Cornelius Inc 74 Publication Number 621260373SER ...
Страница 84: ......
Страница 85: ...IMI Cornelius Inc www cornelius com ...