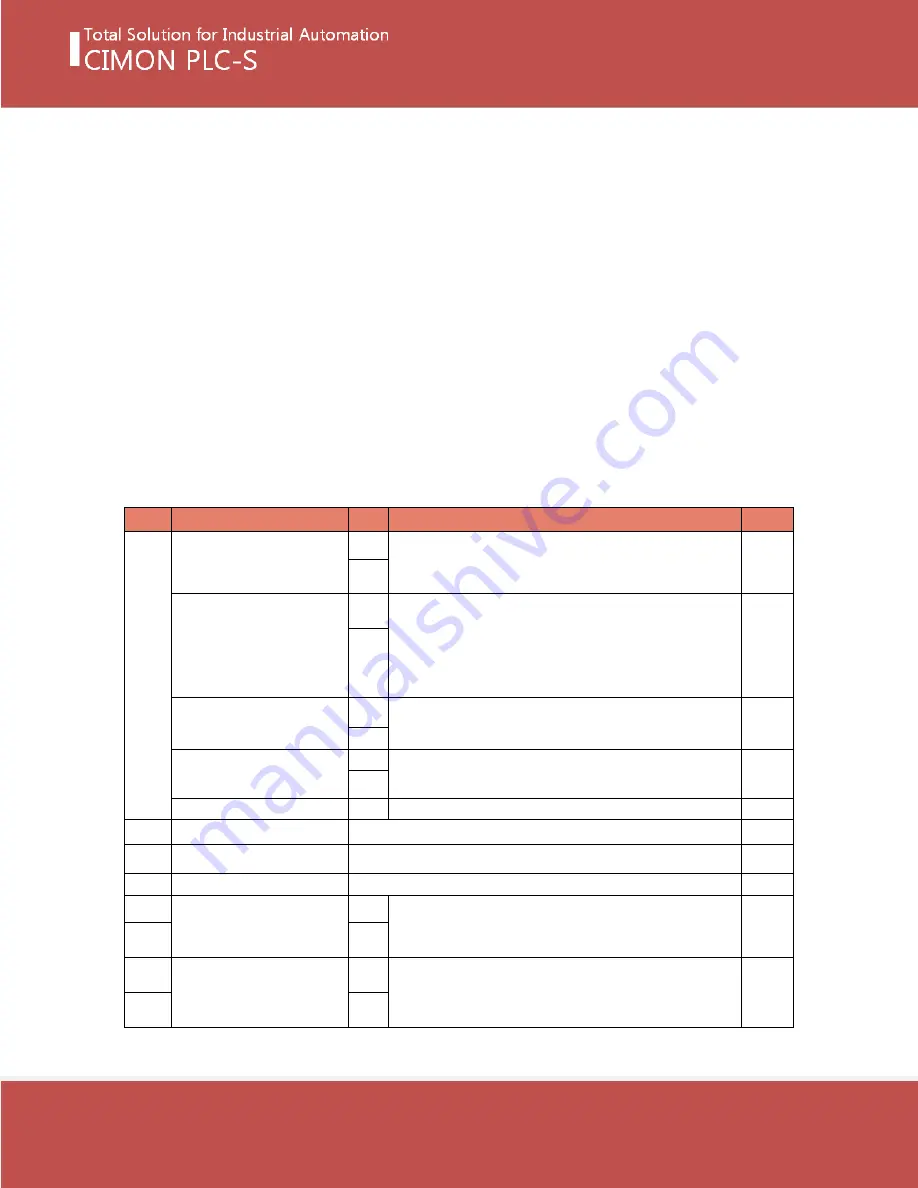
Positioning User Manual
22
1.7
Position Data
The basic controls such as position control and speed control are executed by setting the
required items in this ‘Position Data.’
The special program named “Positioning Program for PLC-S” provides a tool for ‘Position Data.’
Maximum of 30 ‘position data’ can be configured for each axis.
A ‘position data’ occupies 8 word-sized memory.
The same structure of 8 word memory is applied to ‘POSCTRL’ instruction.
Control Code must be ‘0’ at the end of ‘position data’ list.
While in operation, if the control code is zero (0), PLC-S terminates the series of positioning
control and does not go onto the next item on the list.
When a set value is written on the device used as indirect data in the sequence program, the
set value of the ‘position data’ gets modified.
Offset
Item
Bit
Description
Unit
0
Control Pattern
0
00 = Single step control
01 = Continuous control
1
Interpolation
2
00 = Non-Interpolation
01 = Main Axis : Y (Linear Interpolation)
10 = Main Axis : X (Linear Interpolation)
3
Accelerate Time
4
Acc/Dec No. (0 ~ 3)
5
Decelerate Time
6
Acc/Dec No. (0 ~ 3)
7
Control Code
8..F
See ‘Control Code’ table
1
2
Dwell Time
0
~
65,535 or indirect data (device memory)
mSec
3
4
Operation Speed
L
1 ~ 100,000
or indirect data (device memory)
PPS
5
H
6
Target Position Address
L
-2,147,483,648 ~ 2,147,483,647
or indirect data (device memory)
Pulse
7
H