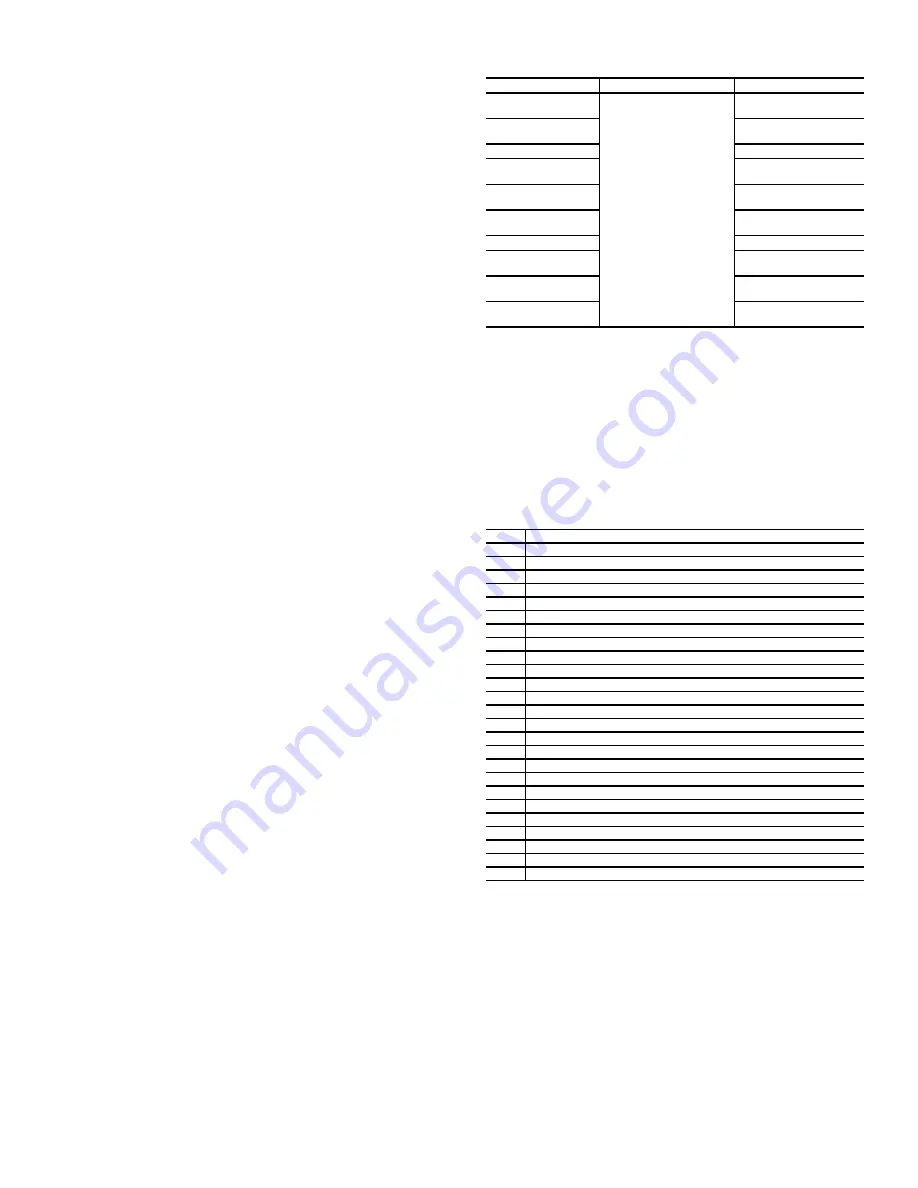
47
ALARM EQUIPMENT PRIORITY
The ComfortVIEW software uses the equipment priority value
when sorting alarms by level. The purpose of the equipment
priority value is to determine the order in which to sort alarms
that have the same level. A priority of 0 is the highest and
would appear first when sorted. A priority of 7 would appear
last when sorted. For example, if two chillers send out identical
alarms, the chiller with the higher priority would be listed first.
The default is 4. This variable can only be changed when using
the ComfortVIEW software, or Network Service Tool. This
variable cannot be changed with the Carrier Controller display.
To configure this option with the Network Service Tool, navi-
gate to point
EQP_TYP
in table
ALARMDEF
.
COMMUNICATION FAILURE RETRY TIME
This variable specifies the amount of time that will be allowed
to elapse between alarm retries. Retries occur when an alarm is
not acknowledged by a network alarm acknowledger, which
may use either ComfortVIEW software or TeLink. If acknowl-
edgment is not received, the alarm will be re-transmitted after
the number of minutes specified in this decision. This variable
can only be changed when using the ComfortVIEW software,
or Network Service Tool. This variable cannot be changed with
the Carrier Controller display. To configure this option with the
Network Service Tool, navigate to point
RETRY_TM
in table
ALARMDEF
.
RE-ALARM TIME
This variable specifies the amount of time that will be allowed
to elapse between re-alarms. A re-alarm occurs when the con-
ditions that caused the initial alarm continue to persist for the
number of minutes specified in this decision. Re-alarming will
continue to occur at the specified interval until the condition
causing the alarm is corrected. This variable can only be
changed when using the ComfortVIEW software, or Network
Service Tool. This variable cannot be changed with the Carrier
Controller display. To configure this option with the Network
Service Tool, navigate to point
RE_ALARM
in table
ALARMDEF
.
ALARM SYSTEM NAME
This variable specifies the system element name that will ap-
pear in the alarms generated by the unit control. The name can
be up to 8 alphanumeric characters in length. This variable can
only be changed when using the ComfortVIEW™ software or
Network Service Tool. This variable cannot be changed with
the Carrier Controller display. To configure this option with the
Network Service Tool, navigate to point
ALRM_NAM
in ta-
ble
ALARMDEF
.
Daylight Savings Time Configuration
The 30XV chiller with Greenspeed
®
Intelligence control con-
tains software which can automatically correct for daylight sav-
ings time. This software is accessible from the Carrier Controller
display, ComfortVIEW software, or Network Service Tool.
To enable this feature, Daylight Savings Select must be set to
1. The start of daylight saving must be configured by setting
the Month, Day of Week, and Week of Month. The end for
Daylight Saving must also be configured. To configure this op-
tion with the Carrier Controller display, see Table 30.
Table 30 — Daylight Savings Time Configuration
Capacity Control Overrides
The following capacity control overrides (
Main Menu
Maintenance Menu
Capacity Control
Override Capaci-
ty Nb A, B
) will modify the normal operation routine. If any of
the override conditions listed below is satisfied, the override
will determine the capacity change instead of the normal con-
trol. Overrides are listed by priority order and are often linked
to unit operating modes. See Table 31 for a list of capacity con-
trol overrides. See the Operating Modes section on page 56 for
more information regarding operating modes.
Table 31 — Capacity Control Overrides
Override #2: Low Suction Pressure
This override is activated when the Expansion Valve (EXV) is
not in DSH (discharge superheat) mode and the Saturated Suc-
tion Temperature (SST) goes below 13.25°F (–10.4°C) for wa-
ter or below (13.25°F – (34°F – Brine Freeze Setpoint)) for
units configured with brine. The controller at this point starts to
unload the unit until the SST exceeds 34°F (1.1°C).
Override #6: EWT < Control Point
This override stops the compressors without alarms.
Override #7: Ramp Loading
No capacity increase will be made if the unit is configured for
ramp loading and the rate of change of the leaving water is
greater than Ramp Loading Rate.
DISPLAY NAME
PATH
VALUE
Activate
Main Menu
Configuration Menu
Broadcast Menu
Brocasts
1 or 2
Default = 2
Daylight
Savings Select
Enable
Default = Disable
Entering
Month
Enter Starting Month for
Daylight Saving
Day of Week
(1=Monday)
Enter the Day of the Week
Daylight Saving Starts
Week of Month
Enter Week of the Month
Daylight Saving Starts
Leaving
Month
Enter Ending Month for
Daylight Saving
Day of Week
(1=Monday)
Enter the Day of the Week
Daylight Saving ends
Week of Month
Enter Week of the Month
Daylight Saving ends
NO.
DESCRIPTION
0
Normal Operation
2
Low Suction Pressure
6
EWT < control point
7
Ramp Loading
9
Demand Limit Reached
10
Flow switch is open
11
Customer Interlock is closed
12
Flow Available Delay
14
Low LWT
15
Compressor Disabled
16
High Discharge Pressure
23
Low SP
25
Oil Recovery
34
Low SST
53
ON-OFF-ON Delay
56
Evaporator Heater Isolation Valve Opening Delay
59
Low Oil Level
62
High Compressor Motor Temperature
66
High Discharge Gas Temperature
67
DGT Off Protection
70
Low Refrigerant Protection
71
Low Refrigerant Protection
77
Oil Pressure at Start
78
Bad VFD Spd At Start
91
Demand Limit
Содержание AquaForce 30XV140
Страница 79: ...79 Fig 76 VFD Communication Wiring Compressor A B Fan VFD A1 A2 B1 B2...
Страница 82: ...82 Fig 81 VFD Compressor Locations 30XV225 325 30XV350 500 30XV140 325 COMPRESSOR A VFD COMPRESSOR B VFD...
Страница 228: ...228 Fig 90 30XV Typical Field Wiring Schematic cont...
Страница 229: ...229 Fig 91 30XV Standard Tier 140 275 All Voltages Power Schematic NOTE See Legend on page 226...
Страница 230: ...230 Fig 92 30XV Standard Tier 300 325 All Voltages Power Schematic NOTE See Legend on page 226...
Страница 231: ...231 Fig 92 30XV Standard Tier 300 325 All Voltages Power Schematic cont NOTE See Legend on page 226...
Страница 232: ...232 Fig 93 30XV Standard Tier 350 500 380 400 415 440 460 575v Power Schematic NOTE See Legend on page 226...
Страница 233: ...233 Fig 93 30XV Standard Tier 350 500 380 400 415 440 460 575v Power Schematic cont NOTE See Legend on page 226...
Страница 234: ...234 Fig 94 30XV High Tier 350 450 All Voltages Mid Tier 350 500 All Voltages Power Schematic NOTE See Legend on page 226...
Страница 235: ...235 Fig 95 30XV Mid Tier 140 All Voltages 160 275 380 400 415 440 460 575v Power Schematic NOTE See Legend on page 226...
Страница 236: ...236 Fig 96 30XV High Tier 140 200 380 400 415 440 460 575v Power Schematic NOTE See Legend on page 226...
Страница 237: ...237 Fig 97 30XV High Tier 140 200 208 230v Mid Tier 160 200 208 230v Power Schematic NOTE See Legend on page 226...
Страница 238: ...238 Fig 98 30XV High Tier 225 325 All Voltages Mid Tier 300 325 All Voltages Power Schematic NOTE See Legend on page 226...
Страница 240: ...240 Fig 99 30XV Communication Wiring...
Страница 241: ...241 Fig 100 30XV 115V Control Wiring All Tonnages All Voltages...
Страница 242: ...242 Fig 101 30XV 24V Control Wiring 30XV140 325 All Voltages...
Страница 243: ...243 Fig 101 30XV 24V Control Wiring 30XV140 325 All Voltages cont...
Страница 244: ...244 Fig 102 30XV 24V Control Wiring 30XV350 500 All Voltages...
Страница 245: ...245 Fig 102 30XV 24V Control Wiring 30XV350 500 All Voltages cont...
Страница 246: ...246 Fig 103 Component Arrangement Diagram for 30XV140 325...
Страница 247: ...247 Fig 103 Component Arrangement Diagram for 30XV140 325 cont...
Страница 248: ...248 Fig 104 Component Arrangement Diagram for 30XV350 500...
Страница 337: ...337 APPENDIX J FACTORY SUPPLIED PUMPS cont Fig L System Information...
Страница 338: ...338 APPENDIX J FACTORY SUPPLIED PUMPS cont Fig M Unit and Language Settings...
Страница 339: ...339 APPENDIX J FACTORY SUPPLIED PUMPS cont Fig N Hand Off Auto This is set in Auto mode for sensorless operation...
Страница 341: ...341 APPENDIX J FACTORY SUPPLIED PUMPS cont Fig P Data Input 2...
Страница 342: ...342 APPENDIX J FACTORY SUPPLIED PUMPS cont Fig Q Data Input 3...
Страница 347: ...347 APPENDIX J FACTORY SUPPLIED PUMPS cont Fig U Pump Wiring Diagram...