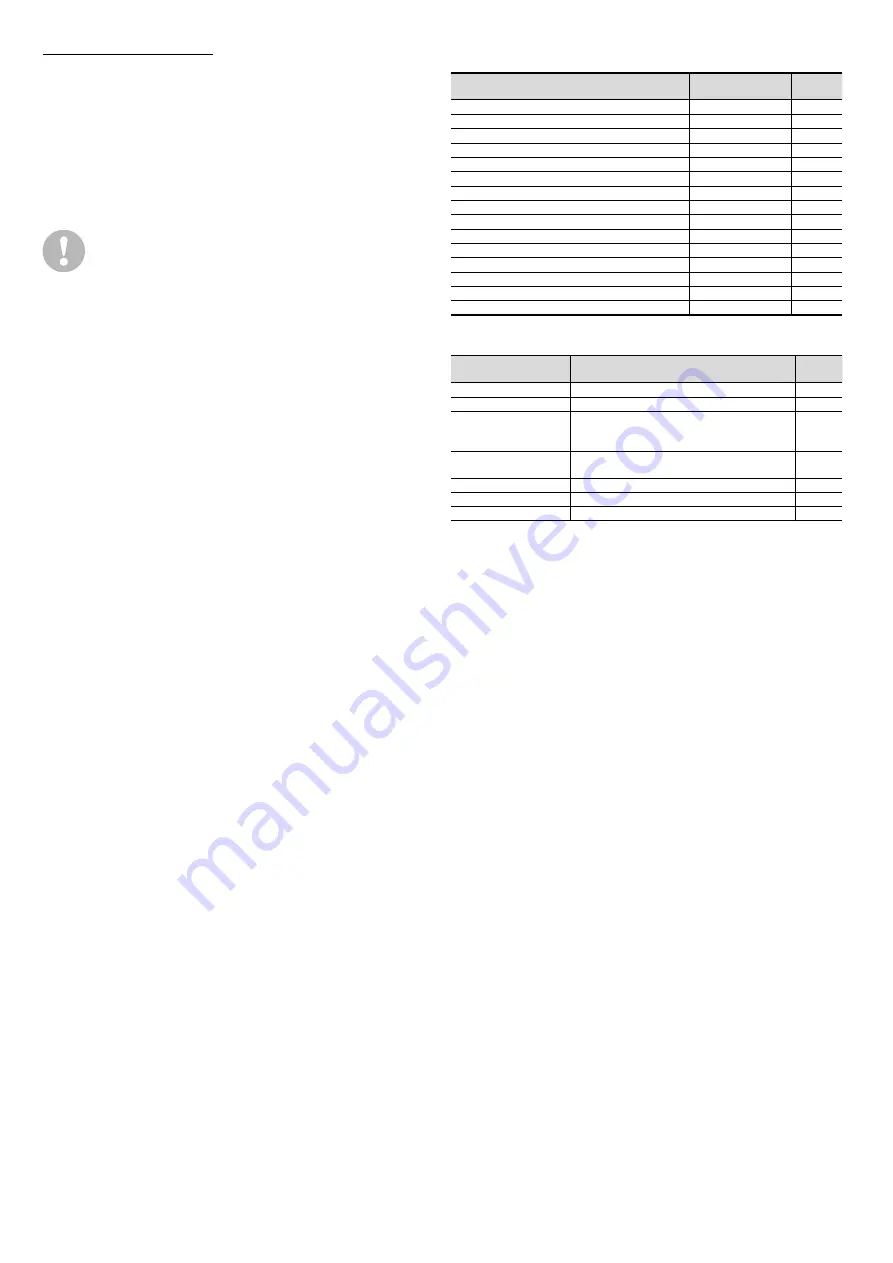
68
Refrigerant circuit checks:
•
The unit is subject to F-gas tight regulatory checks.
Please refer to the table in the introduction.
•
Check the unit operating parameters and compare them
with the previous values,
•
Check the operation of the high pressure switches.
Replace as necessary,
•
Check the fouling of the filter drier. Replace it if necessary,
•
Keep an up-to-date service booklet specific to the
refrigeration unit in question.
Ensure all adequate safety measures are taken for all
these operations: use appropriate PPE (personal
protective equipment), comply with all industry and
local regulations, use common sense.
13.3 - Level 3 maintenance
Maintenance at this level requires specific skills, qualifications,
tools and expertise. Only the manufacturer, his representative
or authorised agent are permitted to carry out this work.
This maintenance work relates to the following:
•
Replacement of major components (compressor, water
heat exchanger).
•
Operations on the refrigerant circuit (handling refrigerant),
•
Modification of factory-set parameters (change of
application).
•
Movement or disassembly of the refrigeration unit,
•
Any operation due to proven lack of maintenance,
•
Any operation covered by the warranty.
•
One or two leak detection operations per year performed
by qualified personnel using a certified leak detector.
•
To reduce waste, the refrigerant and the oil must be
transferred in accordance with applicable regulations,
using methods that limit refrigerant leaks and pressure
drops and with materials that are suitable for the products.
•
Any detected leaks must be repaired immediately
•
The compressor oil that is recovered during maintenance
contains refrigerant and must be treated accordingly.
•
Refrigerant under pressure must not be vented to the
open air.
•
If the refrigerating circuit must be opened, cap all
openings for a period of up to one day. If open for longer,
blanket the circuit with a dry, inert gas (e.g. nitrogen).
13.4 - Tightening of the electrical connections
Component
Designation in the
unit
Value
(N.m)
Welded screw PE, customer connection
-
40
Screw terminal, fuse holder
FU1, FU2, FU3, FU4
10
Screw terminal, fuse holder
FU100
0,8-1,2
Screw terminal, compressor contactor
KM1-->KM12
3-4,5
Brass screw M6, compressor ground
EC-
5
M6 screw, compressor connection
EC-
5
Screw terminal, circuit breakers
QM-
2
Screw terminal, pump contactor
KM90 - KM90A
2,5
M8 screw customer connection (size 160-220)
QS100
15 to 22
M10 screw customer connection (size 260-400)
QS100
30 to 44
M12 screw customer connection (size 430-520)
QS100
50 to 75
Screw terminal, circuit breakers (size 160-400)
QF100
3,2-3,7
Screw terminal, circuit breakers (size 430-520)
QF100
8-10
Screw terminal, fuse holder 32A (opt231)
Fu-
2,5
Screw terminal, fuse holder 100A (opt231)
Fu-
3,5- 4
13.5 - Tightening torques for the main fastenings
Screw type
Use
Value
(N.m)
Metal screw D=4.8
Condensing module, Casing, Supports
4,2
Metal screw D=6,3
Plastic volute
4,2
Taptite M10 screw
Condensation module, chassis-structure,
electrical box fixing, plate heat exchanger and
pump
30
Taptite M6 screw
Pipe supports, enclosure, variable frequency
drive supports
7
Oil equalisation screw
Oil equalisation line
145
H M6 screw
Pipe clip
10
H M10 nut
Compressor chassis, Compressor fixing
30
Содержание 30RBM 160
Страница 75: ......