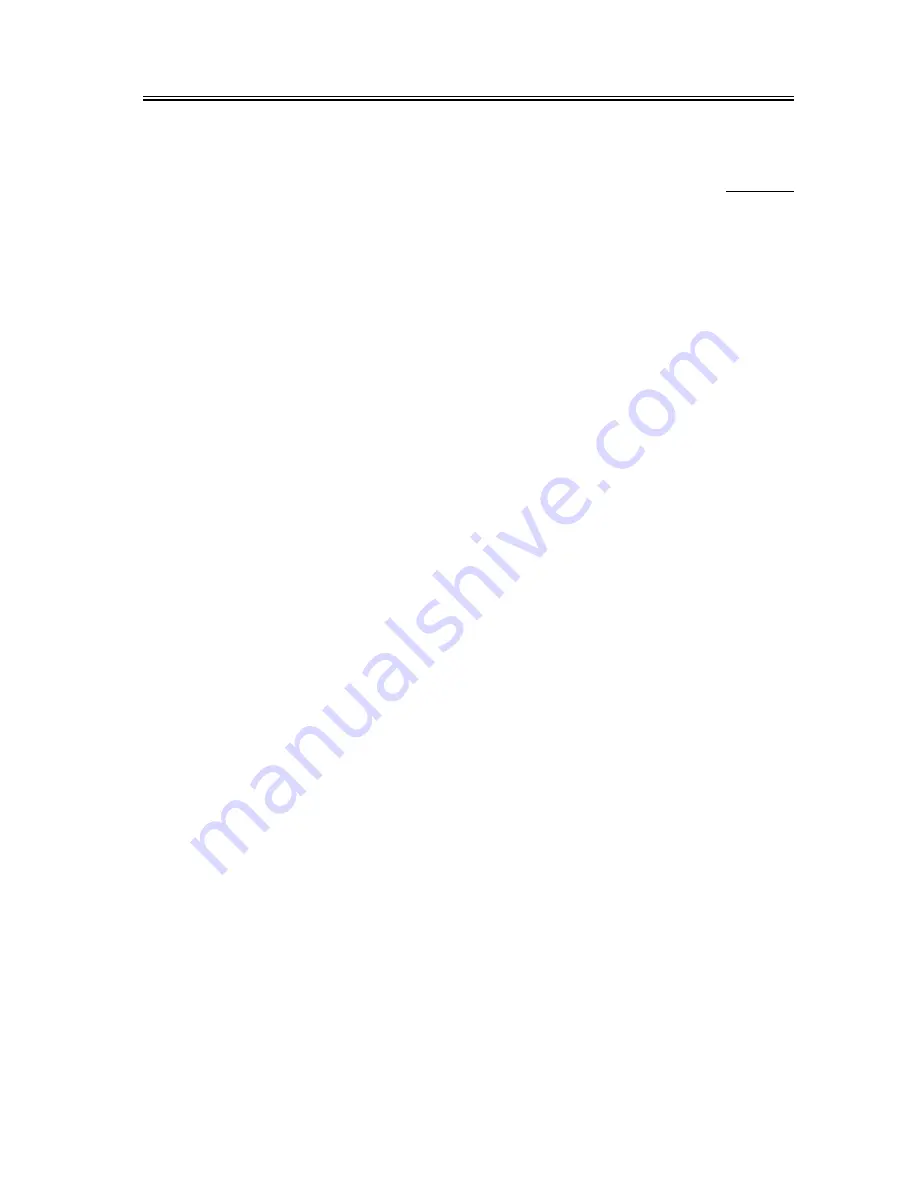
Chapter 17
17-1
17.1
Error Code Details
17.1.1
Error Code Details Table
0006-4868
T-17-1
Code
Detail
Description
Timing of detection
E000
The rise in temperature in the fixing unit at time of power-on is inadequate.
0001
After power-on, the output of the
noncontact thermistor does not
reach 40 deg C within 180 sec.
E001
The fixing unit is overheating.
0001
The high-temperature detection
port continues to remain ON for
500 msec.
0003
The reading of the no-contact
thermistor remains 250 deg C for
500 msec.
0004
The difference in temperature
between the non-contact thermistor
and the end thermistor remains 80
deg C or more for 500 msec.
0005
At the end of initial rotation, the
difference in temperature between
the sub (end) thermistor and the
main (non-contact) thermistor is 20
deg C or more for 100 msec.
(A reversal in temperature (caused,
for example, by a piece of residual
paper) is detected.)
E002
The rise in temperature of the fixing unit is inadequate.
0002
The output of the non-contact
thermistor does not reach 60 deg C
within 240 sec after it has reached
40 deg C.
0003
The output of the non-contact
thermistor does not reach 90 deg C
within 180 sec after it has reached
60 deg C.
Содержание iR C3200 Series
Страница 1: ...Dec 3 2004 Service Manual iR C3200 Series iR C3220N PRT ...
Страница 2: ......
Страница 6: ......
Страница 40: ...Contents ...
Страница 41: ...Chapter 1 Introduction ...
Страница 42: ......
Страница 44: ......
Страница 73: ...Chapter 2 Installation ...
Страница 74: ......
Страница 144: ...Chapter 2 2 68 ...
Страница 145: ...Chapter 3 Basic Operation ...
Страница 146: ......
Страница 148: ......
Страница 158: ...Chapter 3 3 10 ...
Страница 159: ...Chapter 4 Basic Operations As a Printer ...
Страница 160: ......
Страница 162: ......
Страница 171: ...Chapter 5 Main Controller ...
Страница 172: ......
Страница 212: ...Chapter 5 5 38 ...
Страница 213: ...Chapter 6 Original Exposure System ...
Страница 214: ......
Страница 250: ...Chapter 6 6 34 ...
Страница 251: ...Chapter 7 Image Processing System ...
Страница 252: ......
Страница 254: ......
Страница 260: ...Chapter 7 7 6 ...
Страница 261: ...Chapter 8 Laser Exposure ...
Страница 262: ......
Страница 264: ......
Страница 279: ...Chapter 8 8 15 F 8 19 Main scanning direction angle correction lens Main scanning direction correction motor ...
Страница 285: ...Chapter 9 Image Formation ...
Страница 286: ......
Страница 291: ...Contents ...
Страница 292: ......
Страница 396: ...Chapter 9 9 104 ...
Страница 397: ...Chapter 10 Pickup Feeding System ...
Страница 398: ......
Страница 406: ...Contents ...
Страница 434: ...Chapter 10 10 28 8 1 2 3 4 9 1 2 3 4 5 10 thereafter repeats 7 through 10 1 2 3 4 5 11 1 2 3 4 5 12 1 2 3 4 5 ...
Страница 437: ...Chapter 10 10 31 9 1 2 3 10 1 2 3 ...
Страница 574: ...Chapter 10 10 168 ...
Страница 575: ...Chapter 11 Fixing System ...
Страница 576: ......
Страница 580: ......
Страница 650: ...Chapter 11 11 70 ...
Страница 651: ...Chapter 12 Externals and Controls ...
Страница 652: ......
Страница 658: ...Contents ...
Страница 729: ...Chapter 13 MEAP ...
Страница 730: ......
Страница 731: ...Contents Contents 13 1 Overview 13 1 13 2 MEAP Counter 13 2 13 3 Construction of the MEAP Platform 13 4 ...
Страница 732: ......
Страница 737: ...Chapter 14 Maintenance and Inspection ...
Страница 738: ......
Страница 740: ......
Страница 749: ...Chapter 15 Standards and Adjustments ...
Страница 750: ......
Страница 752: ......
Страница 766: ...Chapter 15 15 14 ...
Страница 767: ...Chapter 16 Correcting Faulty Images ...
Страница 768: ......
Страница 785: ...Chapter 16 16 11 6 Mottled Image F 16 12 7 Flow image on Side F 16 13 8 Toner Stray F 16 14 ...
Страница 789: ...Chapter 16 16 15 2 20 to 30 mm White Spot F 16 23 3 White Spots Leading Edge F 16 24 ...
Страница 790: ...Chapter 16 16 16 4 Fine White Spot Near 30 mm of Trailing Edge F 16 25 5 Line Along Trailing Edge F 16 26 ...
Страница 791: ...Chapter 16 16 17 6 Poor Parallel Reproduction Along Trailing Edge F 16 27 7 Rub off Along Trailing Edge F 16 28 ...
Страница 826: ...Chapter 16 16 52 F 16 45 ...
Страница 835: ...Chapter 16 16 61 Image1 F 16 50 Image2 F 16 51 ...
Страница 977: ...Chapter 17 Self Diagnosis ...
Страница 978: ......
Страница 979: ...Contents Contents 17 1 Error Code Details 17 1 17 1 1 Error Code Details Table 17 1 ...
Страница 980: ......
Страница 1002: ...Chapter 17 17 22 ...
Страница 1003: ...Chapter 18 Service Mode ...
Страница 1004: ......
Страница 1128: ...Chapter 18 18 122 ...
Страница 1129: ...Chapter 19 Upgrading ...
Страница 1130: ......
Страница 1132: ......
Страница 1141: ...Chapter 19 19 9 5 Click Register Firmware F 19 8 6 Click Register from selected folder F 19 9 ...
Страница 1146: ...Chapter 19 19 14 8 Select the model of the machine F 19 16 9 Select the unit you want and click Connect F 19 17 ...
Страница 1147: ...Chapter 19 19 15 10 Click Set host name F 19 18 11 The machine s IP address is entered automatically click OK F 19 19 ...
Страница 1153: ...Chapter 19 19 21 3 Click Set host name F 19 26 4 The machine s IP address is entered automatically click OK F 19 27 ...
Страница 1156: ...Chapter 19 19 24 T 19 5 F 19 32 T 19 6 Normal Mode Safe Mode ...
Страница 1162: ...Chapter 19 19 30 3 Click Set host name F 19 38 4 The machine s IP address is entered automatically Click OK F 19 39 ...
Страница 1164: ...Chapter 19 19 32 7 Click System Software Download F 19 42 8 Select the version to download and click Start F 19 43 ...
Страница 1169: ...Chapter 19 19 37 1 Click To Next under Download upload F 19 48 2 Select language for the iRC3200 and click Connect F 19 49 ...
Страница 1170: ...Chapter 19 19 38 3 Click Set host name F 19 50 4 The machine s IP address will be entered automatically click OK F 19 51 ...
Страница 1172: ...Chapter 19 19 40 7 Click Language Download F 19 54 8 Select the version to download and click Start F 19 55 ...
Страница 1180: ...Chapter 19 19 48 7 Click Boot ROM Download F 19 66 8 Select the version to download and click Start F 19 67 ...
Страница 1185: ...Chapter 19 19 53 2 Select DCON and click Connect F 19 73 3 Click Set host name F 19 74 ...
Страница 1192: ...Chapter 19 19 60 2 Select G3FAX and click Connect F 19 84 3 Click Set host name F 19 85 ...
Страница 1199: ...Chapter 19 19 67 2 Select SYSTEM under iRC3200 and click Connect F 19 95 3 Click Set host name F 19 96 ...
Страница 1205: ...Chapter 19 19 73 2 Select SYSTEM under iRC3200 and click Connect F 19 105 3 Click Set host name F 19 106 ...
Страница 1206: ...Chapter 19 19 74 4 The machine s IP address is entered automatically click OK F 19 107 5 Click OK to start a connection F 19 108 ...
Страница 1209: ...Chapter 20 Service Tools ...
Страница 1210: ......
Страница 1211: ...Contents Contents 20 1 Special Tools 20 1 20 2 Solvents and Oils 20 2 ...
Страница 1212: ......
Страница 1215: ...Dec 3 2004 ...
Страница 1216: ......