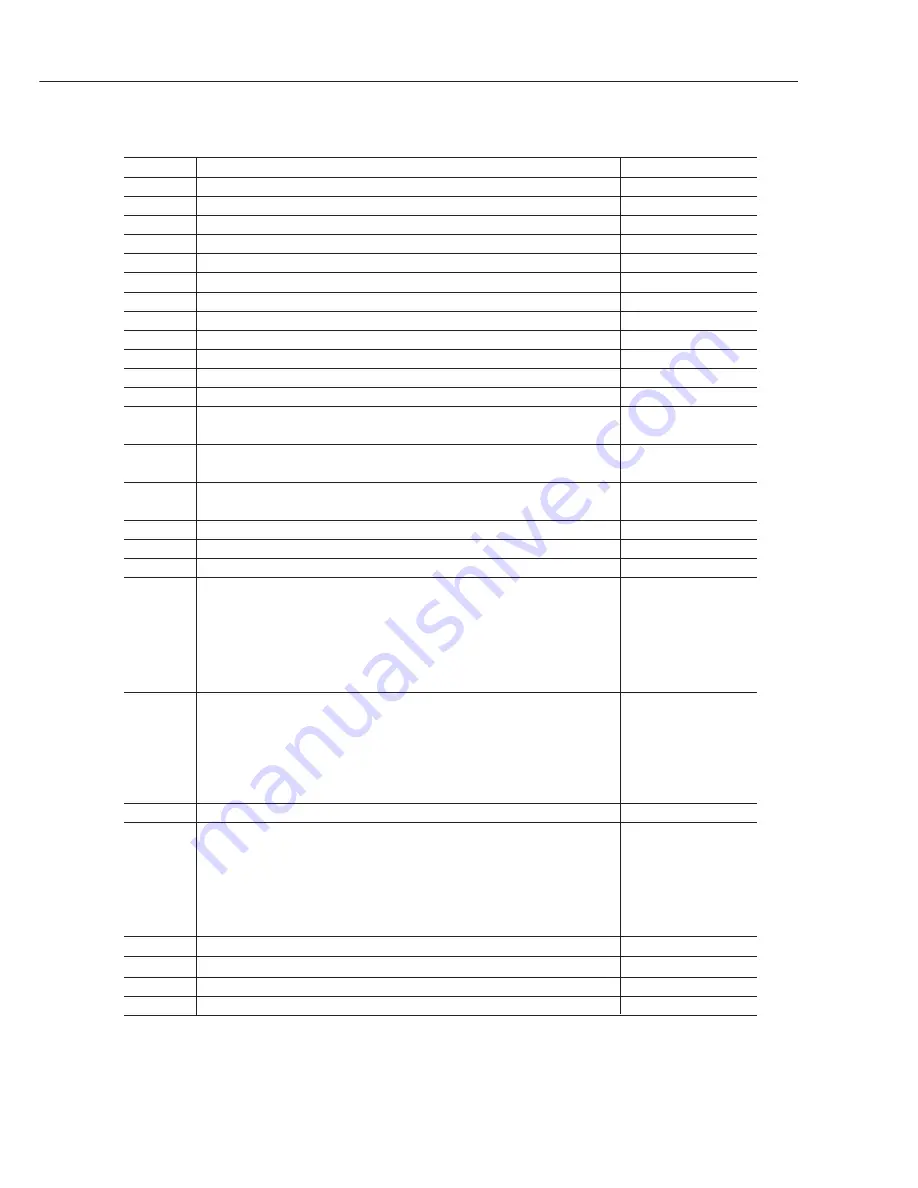
b) Errors
Code*
1
Status
Maintenance No.*
2
E02000
No roll media
7.3.1
E0200A
Paper width not detected
7.3.3
E0200B
Media loading position error
7.3.3
E0200C
Media leading edge not detected
7.3.3
E0200D
Cut sheet trailing edge not detected
7.3.2
E0200E
Media is too small
7.3.3
E0200F
Media is too large
7.3.3
E02010
Media is skewed
7.3.3
E02015
Cutting failure
7.3.4
E02016
Paper became misaligned during printing
7.3.2
E02017
Media right edge not detected
7.3.3
E02018
Media left edge not detected
7.3.3
E02400
Cut sheets were loaded even though the received data
7.3.5
indicated roll media
E02401
Roll media was not loaded even though the received data
7.3.5
indicated roll media
E02402
Cut sheets were not loaded even though the received data
7.3.5
indicated cut sheets
E02403
Media was too small during printing of adjustment pattern
7.3.5
E02404
Borderless printing was specified when cut dust reduction function is set to on
7.3.6
E02405
Invalid paper position for borderless printing
7.3.6
E02500
No ink (Bk)
7.3.7
E02501
No ink (Y)
E02502
No ink (M)
E02503
No ink (C)
E02504
No ink (PM)
E02505
No ink (PC)
E02506
Ink tank not installed (Bk)
7.3.8
E02507
Ink tank not installed (Y)
E02508
Ink tank not installed (M)
E02509
Ink tank not installed (C)
E0250A
Ink tank not installed (PM)
E0250B
Ink tank not installed (PC)
E02520
Displayed before printing when "Ink Check Off" menu is set to "Yes".
7.3.9
E02521
Remaining ink low (Bk)
7.3.10
E02522
Remaining ink low (Y)
E02523
Remaining ink low (M)
E02524
Remaining ink low (C)
E02525
Remaining ink low (PM)
E02526
Remaining ink low (PC)
E02800
No head
7.3.11
E02801
Head overheating
7.3.11
E02802
Incorrect head was installed
7.3.11
E02803
Head EEPROM error
7.3.11
*1: The codes correspond to the numbers shown on the display in the service mode.
Codes in parentheses are not shown on the display when error occurs.
*2: The maintenance numbers correspond to the section title numbers in
Part 5: 7
TROUBLESHOOTING
.
Part 3: Operations
W6200
3-42
Содержание imagePROGRAF W6200
Страница 2: ...1003 N 0 00 0 ...
Страница 3: ......
Страница 16: ...XII This page is intentionaly left blank ...
Страница 80: ... PRINT PATTERN SCALE Maintenance test pattern 3 33 W6200 Part 3 Operations Figure 3 28 SCALE Image ...
Страница 121: ...Part 4 Technical Reference W6200 4 12 This page intentionally left blank ...
Страница 167: ...5 1 4 Paper path system Part 4 Technical Reference W6200 4 58 Feed sensor Figure 4 40 Layout paperpath sensor ...
Страница 266: ...Part 5 Maintenance W6200 5 98 9 CIRCUIT DIAGRAM Refer to Parts Catalog for the part layouts on each board ...
Страница 267: ...5 99 W6200 Part 5 Maintenance This page intentionally left blank ...
Страница 272: ...Part 5 Maintenance W6200 5 104 1 System Controller 1 15 F E D C B A 2 3 4 5 6 7 8 IC1 1 4 9 2 System Controller ...
Страница 273: ...Part 5 Maintenance W6200 5 105 1 System Controller 2 15 F E D C B A 2 3 4 5 6 7 8 IC1 4 4 ...
Страница 274: ...Part 5 Maintenance W6200 5 106 1 System Controller 3 15 F E D C B A 2 3 4 5 6 7 8 IC1 3 4 ...
Страница 275: ...Part 5 Maintenance W6200 5 107 1 System Controller 4 15 F E D C B A 2 3 4 5 6 7 8 ...
Страница 276: ...Part 5 Maintenance W6200 5 108 1 System Controller 5 15 F E D C B A 2 3 4 5 6 7 8 ...
Страница 277: ...Part 5 Maintenance W6200 5 109 1 System Controller 6 15 F E D C B A 2 3 4 5 6 7 8 ...
Страница 278: ...Part 5 Maintenance W6200 5 110 1 System Controller 7 15 F E D C B A 2 3 4 5 6 7 8 IC2 2 5 IC1 2 4 ...
Страница 279: ...Part 5 Maintenance W6200 5 111 1 System Controller 8 15 F E D C B A 2 3 4 5 6 7 8 IC2 2 5 ...
Страница 280: ...Part 5 Maintenance W6200 5 112 1 System Controller 9 15 F E D C B A 2 3 4 5 6 7 8 IC2 4 5 ...
Страница 281: ...Part 5 Maintenance W6200 5 113 1 System Controller 10 15 F E D C B A 2 3 4 5 6 7 8 IC2 5 5 IC15 IC14 ...
Страница 282: ...Part 5 Maintenance W6200 5 114 1 System Controller 11 15 F E D C B A 2 3 4 5 6 7 8 IC2 3 5 ...
Страница 283: ...Part 5 Maintenance W6200 5 115 1 System Controller 12 15 F E D C B A 2 3 4 5 6 7 8 IC16 ...
Страница 284: ...Part 5 Maintenance W6200 5 116 1 System Controller 13 15 F E D C B A 2 3 4 5 6 7 8 ...
Страница 285: ...Part 5 Maintenance W6200 5 117 1 System Controller 14 15 F E D C B A 2 3 4 5 6 7 8 ...
Страница 286: ...Part 5 Maintenance W6200 5 118 1 System Controller 15 15 F E D C B A 2 3 4 5 6 7 8 ...
Страница 311: ...This document is printed on 100 recycled paper PRINTED IN JAPAN IMPRIME AU JAPON CANON INC ...