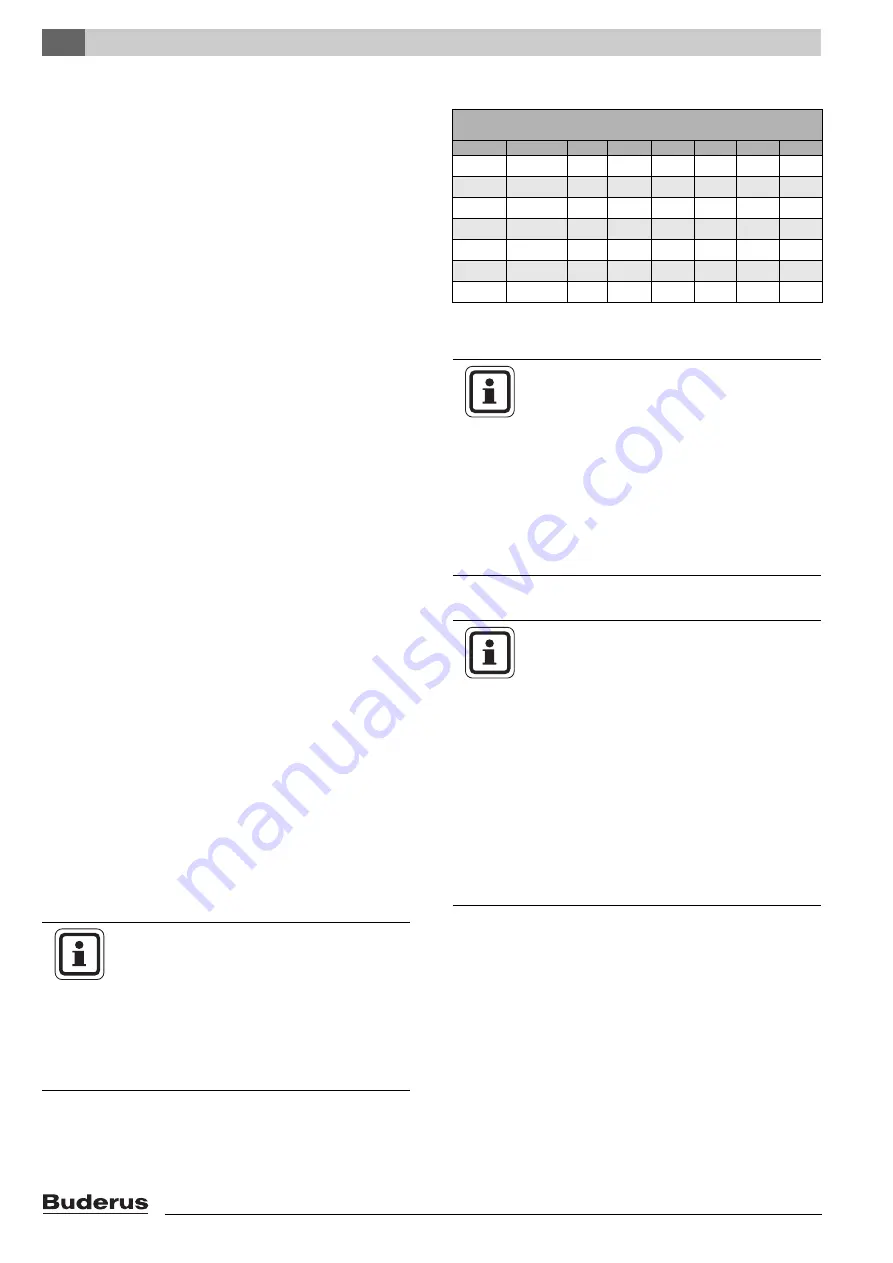
Installation
7
Logano plus SB615 - Technical specifications are subject to change without prior notice.
22
Air supply for combustion from outside the building
If the combustion air supply is brought in from outside, the
room should have two permanent air vents to the outside.
Each vent should have a clear aperture of at least 30 in²
per 10,000 BTU/hr (80 cm² per 1.2 kW) of maximum rated
output of all combustion devices in the boiler room.
If the air is supplied via air ducts, two ducts must be used.
Vertical ducts and openings must have a clear aperture of
at least 2.5 in² per 10,000 BTU/hr (6 cm² per 1.2 kW) of
maximum rated output of all combustion devices in the boil-
er room. Horizontal ducts and openings must have a clear
aperture of at least 1-1/4" per 10,000 BTU/hr (6 cm² per
0.6 kW) of maximum rated output of all combustion devic-
es in the boiler room.
When calculating the clear aperture of the vents, restric-
tions due to screens and guards must be taken into ac-
count. The advice of the air screen manufacturer should be
sought with regard to the percentage of net air space. If the
net air space is not known, the following figures can be tak-
en as a general guide: metal air screens have a net air
space of approx. 60-70% and wooden air screens approx.
20-25%. Air screens should be permanently fixed or linked
to an opening device so that they automatically open when
the system is started up. The air supply vents should be ar-
ranged as follows: the upper opening should be within 9'
(300 cm) of the ceiling and the lower opening within
9'
(300 cm) of the floor as specified in NFPA 54.
Air supply for combustion from adjacent room
Where the air supply for combustion is drawn from within
the building, the air in the boiler room must be supplied by
two vents from inside the building. Each vent must have a
clear aperture of at least 1-1/4" per 10,000 BTU/hr (6 cm²
per 0.6 kW) of maximum rated output of all combustion de-
vices in the boiler room. The air supply vents should be ar-
ranged as follows: the upper opening should be 9' (within
300 cm)
of the ceiling and the lower opening 9' (within 300
cm) of the floor as specified in NFPA 54.
Flue systems
The flue system is designed as a positive pressure
system. The minimum diameter of the flue pipe is
6" (150 mm). Horizontal flues must be supported at least
every 6 feet (160 cm) by wall brackets and vertical flues
must be supported along their horizontal runs to prevent
heavy stresses in those places.
Permissible flue pipe lengths for SB615 boiler
Condensate drainage
The flue system must be supported at least once every 3'
(1,000 mm). This allows the condensate to run back to the
boiler. Low points in the flue system where condensate
could collect must be avoided. The condensate can be
drained off using a plastic hose or PVC drain pipe. The
condensate drain should be installed in such a way that
kinking of the drain hose is not possible. The condensate
neutralizer must be installed below the level of the drain. If
the there is no floor drain and the condensate has to be
pumped away, run it through the neutralizer on gravity first,
then collected in a container and pumped away.
WARNING
Use only approved flue pipe connections
and flue pipes made by the same manufac-
turer for Buderus SB boilers. Never mix com-
ponents from different systems. Doing so
could cause the flue system to fail resulting
in the escape of flue gases leading to injury
or even death.
Maximum height of flue pipe for SB615 boiler
(in feet)
Model Diameter 150
150
180
200
250
300
145
6"
30
124
144
165
185
6"
60
132
165
240
8"
120
165
310
8"
27
132
165
400
10"
14
165
174
510
12"
165
174
640
12"
75
174
Tab. 5
Maximum height of flue pipe
USER NOTE
All lengths quoted are for horizontal and ver-
tical flues and an angle of 87° for conden-
sate to flow back to the boiler. For
every additional 45° the length of the flue
pipe reduces by 4' (1200 mm) (1.2 m) and
by 6' (2000mm) (2.0 m)for every additional
87°.
The flue system operates at a pressure of
0.06" W.C. (15 Pa).
NOTICE:
Condensate has to be disposed off accord-
ing to local regulations. Condensate neutral-
ization may be required.
z
Ensure that untreated condensate is only
passing through hoses and pipening sui-
table for very low pH-levels.
z
If the building is connected to a municipal
sewage system, observe the rules and re-
gulations for disposal into the system.
z
If the building is connected to a septic
system, a neutralizer is recommended to
avoid damage to the system.