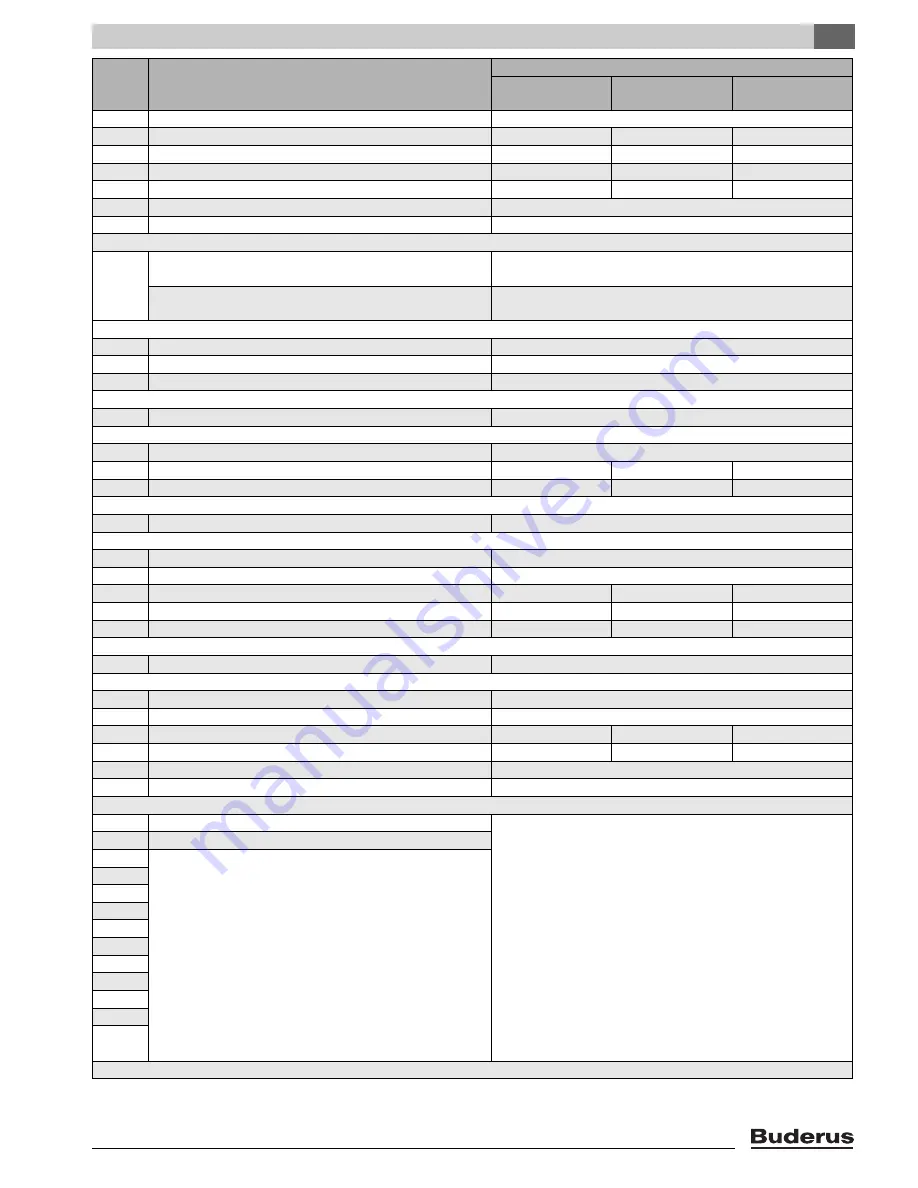
Spare Parts
13
Logano G125 BE - Specifications subject to change without notice.
61
140
Door hinge G105/G115
05327033
141
Gasket DIN125-A10.5-A3K
(x)
(x)
(x)
142
Hex. head bolt ISO4017-M10x25-8.8
(x)
(x)
(x)
150
Hex. head bolt ISO4014-M10x65-8.8
(x)
(x)
(x)
160
Washer DIN125-A10.5-A3K
(x)
(x)
(x)
180
Boiler feet M10x51mm complete
05236440
190
Gasket for flue collar DN130 complete
05354010
200
or
210
Flue silencer DN130 complete, without condensate drain;
higher sound absorption
05074020
Flue silencer D130 with adapter 100mm long, with con-
densate drain, lower sound absorption
05074022
Flue silencer components:
190
Flue collar DN130 complete
05354010
220
Flue collar DN130 complete (step cuff)
05354030
230
Sealing rope10x2000 GP
63020963
250
Burner door complete
63015200
Burner door components:
260
Door hinge
05327020
270
Washer DIN125 A10.5 A3K
(x)
(x)
(x)
280
Hex. head screw ISO4017 M10x25 8.8
(x)
(x)
(x)
290
Observation port cover complete G115/G125/G135
63023634
Observation port cover components:
300
Gasket 30x30x3
63014382
310
Sight glass Tempax 30x30x3.3mm
05447620
320
Sight glass cover plate
(x)
(x)
(x)
330
Hex. head screw ISO4017 M6x12 8.8 A3K
(x)
(x)
(x)
340
Pressure measuring port M6 SW10 V2
(x)
(x)
(x)
350
Burner door insulation G125 W607
63002401
Burner door insulation components:
360
Insulating plate for burner door 24mm
63004169
370
Insulating ring for burner door 10mm
63004170
380
Washer DIN9021 A6,4 A3K
(x)
(x)
(x)
390
Sheet metal screw DIN7981 C ST6.3x25 A3T
(x)
(x)
(x)
400
Sealing rope14x1650 GP
63020965
Glue for securing sealing rope to burner door (a 310ml)
63014361
Mounting material for boiler block G125 "US"
63031288
Components:
1 Hex. head screw M8x16 Ms
2 Distance sleeve R3/8"x39
2 Hex. head nut ISO4032 M10 8 A3K
8 Washer DIN125 A10,5 A3K
4 Washer DIN126 9
4 Hex. head screw ISO4017 M8x25 8.8
4 Hex. head nut DIN6923 M8 8.8 A3K
4 Hex. head screw ISO4017 M10x25 8.8
2 Hex. head screw DIN6921 M10x65 8.8
1 Hex. head screw ISO4017 M6x12 8.8A3K
2 Washer DIN9021 A6.4 A3K
2 Sheet metal screw DIN7981 C ST6.3x25 A3T
Item
Description
Part Number
G125/21-BE
3 Section
G125/28-BE
4 Section
G125/34-BE
5 Section
Table 13 Boiler block and Burner door