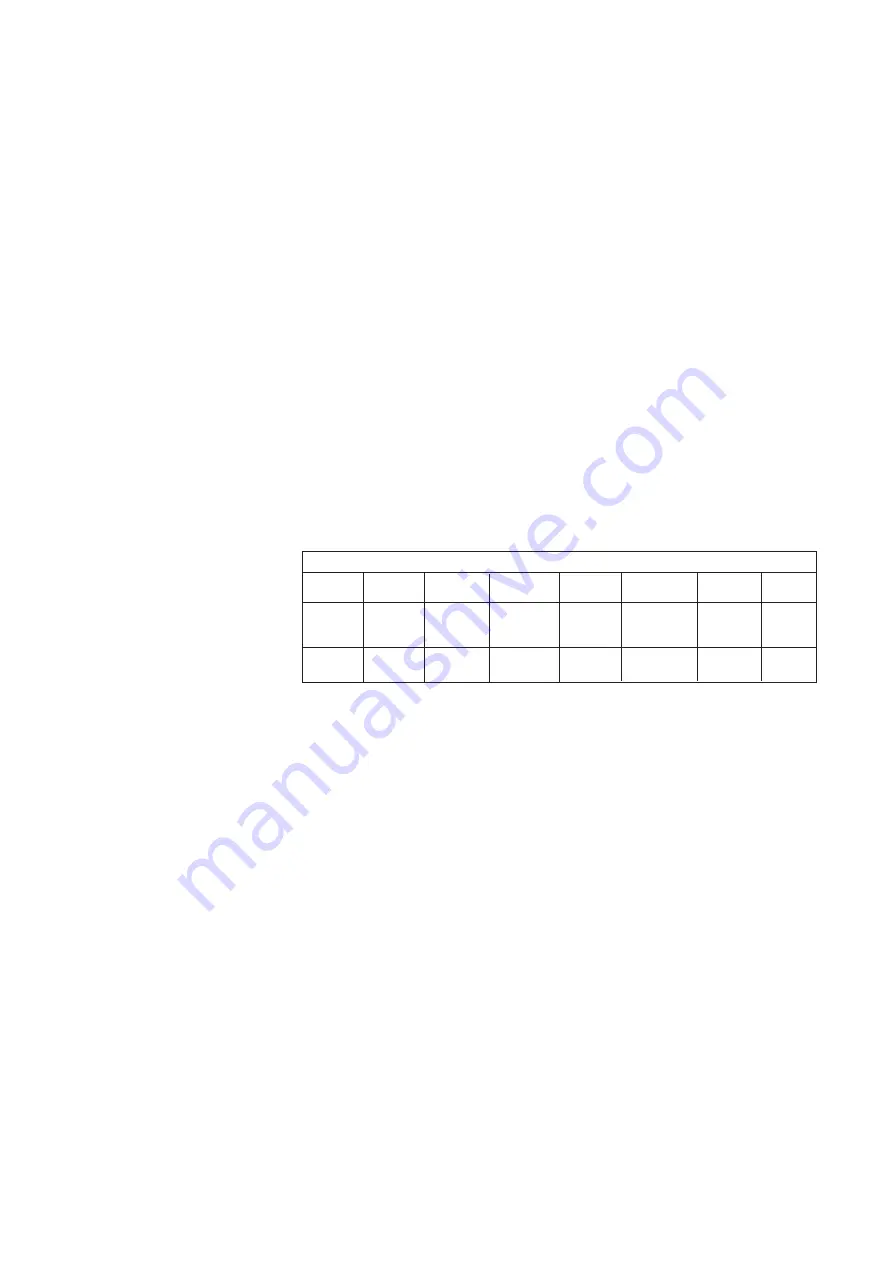
33
Installation and Operation Manual
X-DPT-Profibus-Interface-eng
PN 541-C-068-AAG
November, 2008
4. EEPROM error
: During operation the backup parameter database, located
in EEPROM is continuously checked by comparing the contents of each
parameter in the operational database (including the checksum) with the
contents of the backup database. If a mismatch is found between two
parameter values, the backup database is considered to have become
invalid. Bit 3 will be set in the second diagnostics byte, and the system is
shutdown. The error can not be masked.
5. Sensor zero error
: If after a sensor zero command the processor has
been unable to achieve a residual sensor zero signal of less then 5%, the
flow sensor measurement accuracy can no longer be guaranteed. Bit 4 will
be set in the second diagnostics byte, and the system is shutdown. The
error can not be masked.
4.5.4 Primary non-fatal system errors
Table 5-4 below shows the bit-mapped alarm bits of the third extended diagnos-
tics byte, the primary non-fatal system errors. These error bits all indicate a
primary (i.e. system hardware related) non-fatal system alarm. At the occur-
rence of one or more of these alarms the device will continue to operate as
best as possible. Erroneous signal levels are limited to operational levels before
processing and the alarm will disappear if the situation returns to normal. All of
these error/alarm message bits can be disabled through the parameterization
message.
Table 5-4: Diagnostics: Primary non-fatal system error/alarm bits.
Diagnostics byte 2: Primary non-fatal system errors/alarms
Bit 7
Bit 6 *
Bit 5
Bit 4
Bit 3 *
Bit 2
Bit 1
Bit 0
Valve
Analogue Flow
Setpoint
Analogue
Temp.
Flow
Reserved out of
output
sensor
over
output out
sensor
sensor
range
error
of range
range
of range
error
error
0
0=OK
0=OK
0=OK
0=OK
0=OK
0=OK
0=OK
1=Alarm
1=Alarm
1=Alarm
1=Alarm
1=Alarm
1=Alarm
1=Alarm
* Applies to controller models only. For meter models these bits will never be set.
Explanation of error/alarm bits:
1.
Flow sensor error
: This error occurs if the sensor signal level drops below
a minimum level. This may result from a disconnected sensor, but also
from reversed flow.
2.
Temperature sensor error
: This error occurs if the sensor signal level
drops below a minimum level. This may result from a disconnected
sensor.
3.
Analogue output error
: The analogue output error is generated if the
analogue output signal level differs more then 10% from the expected level.
It may result from defective electronics.
4.
Setpoint overrange
: The setpoint overrange alarm is set if the setpoint
signal, either analogue or through the network exceeds 105%. The setpoint
used in processing is limited to 105%.
5.
Flow sensor out of range
: This error occurs if the sensor signal exceeds
the maximum physical signal level. The sensor signal level is limited to this
maximum before processing.
6.
Analogue output out of range
: This error occurs if the analogue output
signal to be set exceeds the maximum physical signal level allowed with
the electronics. The analogue output level set is the maximum physical
value achievable with the electronics.
7.
Valve out of range
: This error occurs if the control value set on the valve
has reached the maximum possible level. The actual value set is limited to
the maximum value allowed. This error may result from a situation where
there is no gas supplied and yet a setpoint exceeding 0% is present.